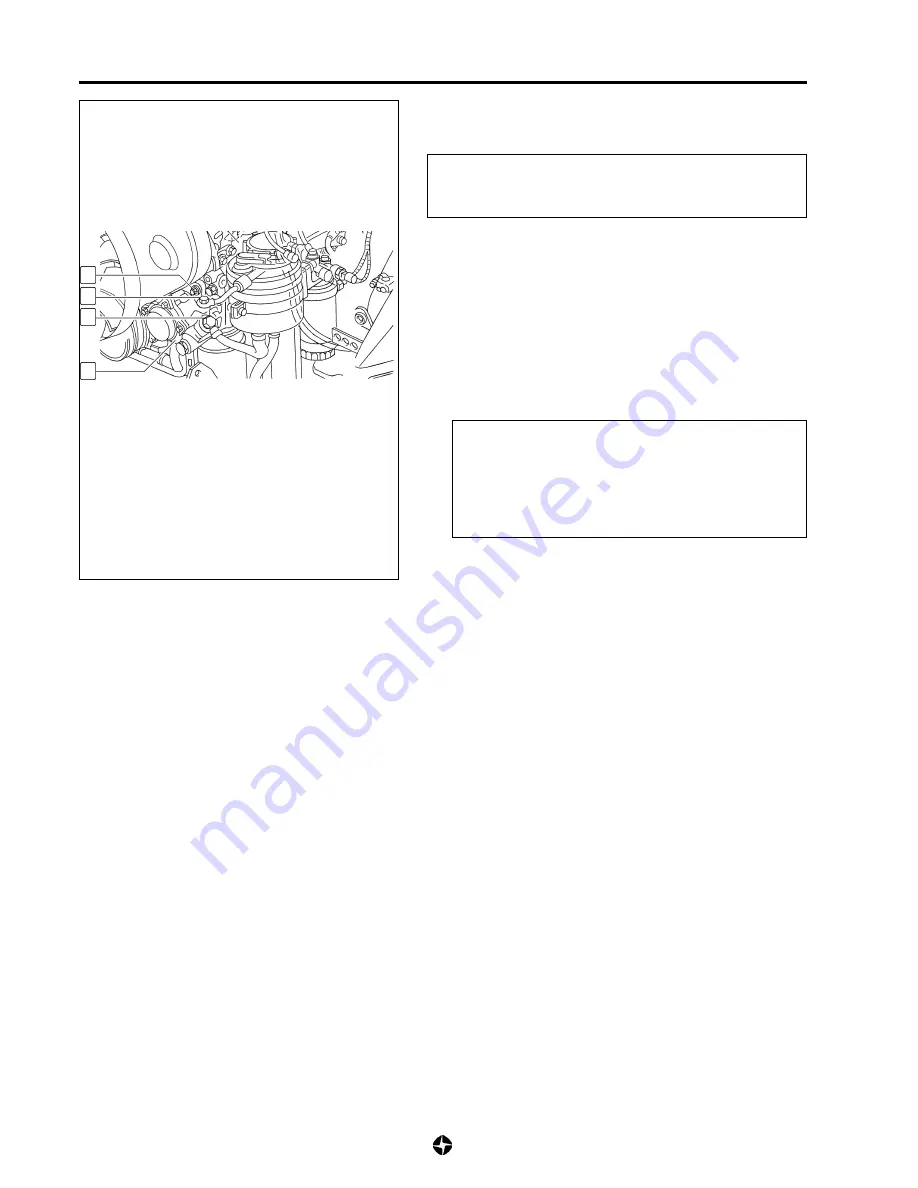
6A-64 ENGINE REPAIR
DISMANTLING AND ASSEMBLY OF THE SERVO
STEERING HYDRAULIC PUMP
CAUTION:
Before starting dismantling clean thoroughly
components to be dismantled and around them.
Dismantling
1) Dismantle water radiator and air radiator (intercooler) (see
6B-8).
2) Disconnect inlet linkage (3) of hydraulic oil to pump and
pour the content of the tank in an adequate container.
3) Disconnect outlet linkage (2) of pressurized oil at pump.
4) Dismantle nuts (1) fixing hydraulic pump (4) to body of the
auxiliary organs group.
5) Take away hydraulic pump (4).
CAUTION:
Plug with appropriated caps air, water and
hydraulic circuits holes while they keep appearing
during dismantling because the entry of alien bodies
in the conductions could seriously damage the
component in question.
Assembly
NOTE:
Clean carefully touching contact areas of pumps, linkages
and lodgings in auxiliary organs group.
1) Proceed to assemble reversing the dismantling order paying
attention to the following tasks:
• Assemble the new impermeabilizing gaskets, washers and
pieces showing any damage.
• Continue assembly applying specified tightening torque's.
Tightening torque:
• Screw linkage at hydraulic pump oil outlet:
3 ÷ 4 Kg-m (30 ÷ 40 Nm)
• Screw linkage at hydraulic pump oil inlet:
3 ÷ 4 Kg-m (30 ÷ 40 Nm)
• Nuts fixing hydraulic pump:
3,5 Kg-m (35 Nm)
1
2
3
4
2) Proceed to fill and purge the hydraulic circuit of the servo
steering (see 0B-27).
Содержание PS-10
Страница 1: ......
Страница 2: ......
Страница 5: ......
Страница 50: ......
Страница 53: ...BUMPERS FRONTHOODANDFRONTAL2 3 REAR BUMPER 1 Rear bumper 2 Side pad 3 Center pad 2 3 3 1 2 ...
Страница 57: ...BUMPERS FRONTHOODANDFRONTAL2 7 FRONTAL 1 Front Grille 2 Fender 3 Register Cover 4 Front Frame 3 4 2 1 ...
Страница 69: ......
Страница 90: ......
Страница 123: ...WHEELS AND TIRES 3F 7 TIGHTENING TORQUE SPECIFICATIONS Wheel nuts 11 17 110 170 ELEMENT TORQUE Kg m Nm ...
Страница 124: ......
Страница 149: ......
Страница 163: ......
Страница 209: ......
Страница 420: ...6C 38ENGINEFUELANDEMISSIONCONTROLSYSTEM CONNECTION DIAGRAM FROM CONTROL BOARD TO ENGINE COMPONENTS CONNECTOR A ...
Страница 422: ...6C 40ENGINEFUELANDEMISSIONCONTROLSYSTEM CONNECTIONS DIAGRAM FROM CONTROL UNIT TO VEHICLE COMPONENTS CONNECTOR B ...
Страница 447: ...TRANSMISSION 7 1 SECTION 7 TRANSMISSION CONTENTS GEARBOX 7A CLUTCH 7C TRANSFER BOX 7D FRONT AND REAR DIFFERENTIAL 7E 7 ...
Страница 448: ......
Страница 489: ......
Страница 505: ......
Страница 594: ...BODYSERVICE9 31 FRAME MAIN DIMENSIONS ...
Страница 595: ...9 32BODYSERVICE FRAME MAIN DIMENSIONS ...
Страница 601: ...ELECTRICAL DIAGRAMS ...
Страница 602: ...ELECTRICAL DIAGRAMS 2 ONLY COMMON RAIL POWER SUPPLY DIAGRAM ...
Страница 603: ...ELECTRICAL DIAGRAMS 3 ONLY COMMON RAIL ENGINE CONTROL SYSTEM ELECTRONIC FUEL INJECTION CONNECTOR A ...
Страница 604: ...ELECTRICAL DIAGRAMS 4 ONLY COMMON RAIL ENGINE CONTROL SYSTEM ELECTRONIC FUEL INJECTION CONNECTOR B ...
Страница 605: ...ELECTRICAL DIAGRAMS 5 ONLY COMMON RAIL STARTING HEATER VALVE DIAGRAM ...
Страница 606: ...ELECTRICAL DIAGRAMS 6 ONLY COMMON RAIL GLOW PLUG STARTING HEATER RELAY DIAGRAM ...
Страница 607: ...ELECTRICAL DIAGRAMS 7 ONLY COMMON RAIL FUEL FILTER SENSORS DIAGRAM ...
Страница 608: ...ELECTRICAL DIAGRAMS 8 ONLY COMMON RAIL DOUBLE STOP SWITCH ...
Страница 609: ...ELECTRICAL DIAGRAMS 9 ONLY COMMON RAIL FUEL PUMP ...
Страница 610: ...ELECTRICAL DIAGRAMS 10 ONLY COMMON RAIL DIAGNOSIS DIAGRAM ...
Страница 611: ...ELECTRICAL DIAGRAMS 11 ONLY COMMON RAIL A C DIAGRAM ...
Страница 612: ...ELECTRICAL DIAGRAMS 12 ONLY MECHANICAL INJECTION POWER SUPPLY DIAGRAM ...
Страница 613: ...ELECTRICAL DIAGRAMS 13 ONLY MECHANICAL INJECTION GLOW PLUG RELAY DIAGRAM ...
Страница 614: ...ELECTRICAL DIAGRAMS 14 ONLY MECHANICAL INJECTION INSTRUMENT PANEL ...
Страница 615: ...ELECTRICAL DIAGRAMS 15 ONLY MECHANICAL INJECTION COMBINATION METER DIAGRAM ...
Страница 616: ...ELECTRICAL DIAGRAMS 16 ONLY MECHANICAL INJECTION COOLING SYSTEM ...
Страница 617: ...ELECTRICAL DIAGRAMS 17 GENERAL DIAGRAMS HEADLAMP LEVELING SYSTEM DIAGRAM ...
Страница 618: ...ELECTRICAL DIAGRAMS 18 GENERAL DIAGRAMS REVERSE LAMP DIAGRAM ...
Страница 619: ...ELECTRICAL DIAGRAMS 19 GENERAL DIAGRAMS RADIO REAR WINDOW DEFOGGER ...
Страница 620: ...ELECTRICAL DIAGRAMS 20 GENERAL DIAGRAMS REAR DEMISTER STOP LAMP DIAGRAM ...
Страница 621: ...ELECTRICAL DIAGRAMS 21 GENERAL DIAGRAMS HORN DIAGRAM ...
Страница 622: ...ELECTRICAL DIAGRAMS 22 GENERAL DIAGRAMS TURN SIGNAL HAZARD LAMP DIAGRAM ...
Страница 623: ...ELECTRICAL DIAGRAMS 23 GENERAL DIAGRAMS LAMPS DIAGRAM ...
Страница 624: ...ELECTRICAL DIAGRAMS 24 GENERAL DIAGRAMS WASHER WIPER DIAGRAM ...
Страница 625: ...ELECTRICAL DIAGRAMS 25 GENERAL DIAGRAMS CHARGING SYSTEM DIAGRAM ...
Страница 626: ...Prepared by SANTANA MOTOR S A After Sales Service Department 1st Ed October 2002 Printed in Spain Printed October 2002 ...
Страница 627: ......