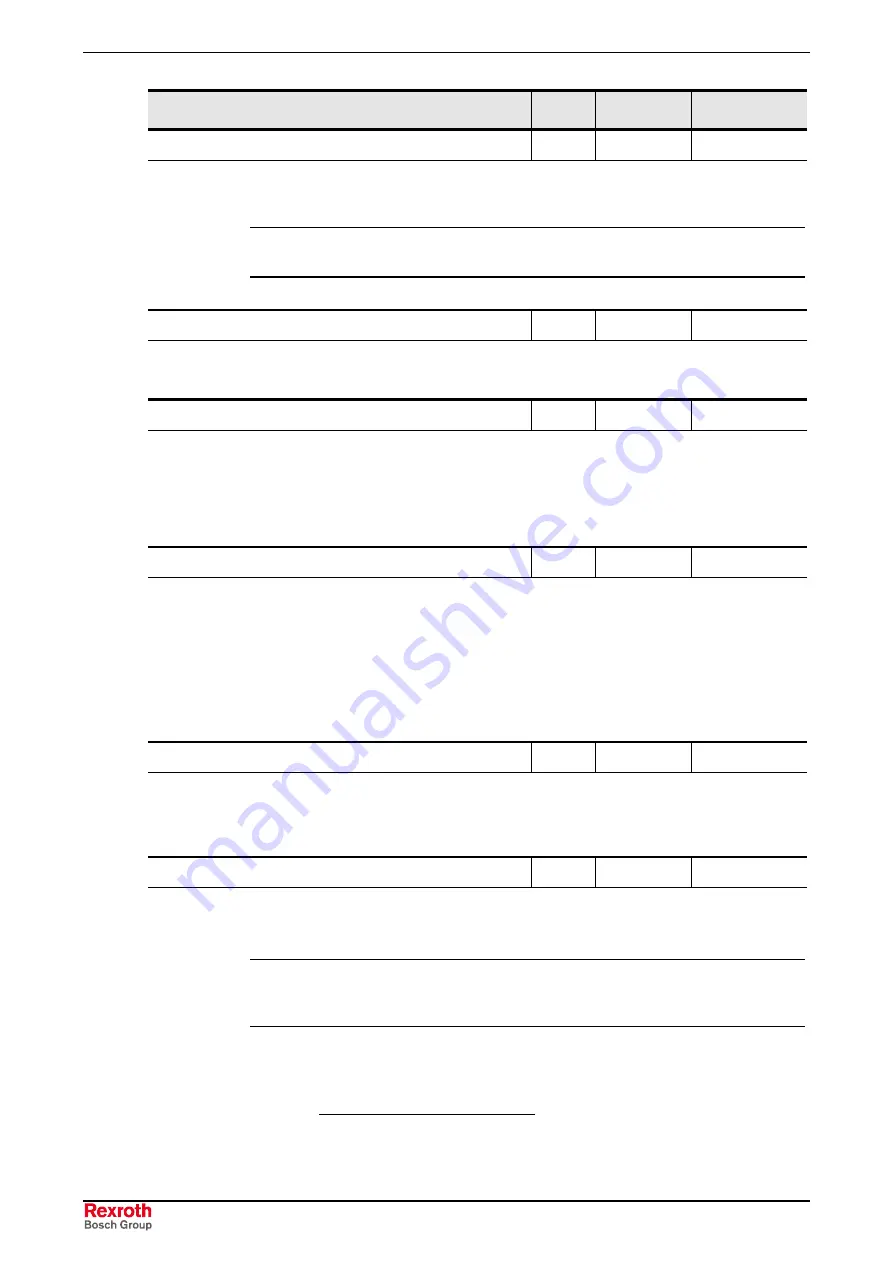
11-14
Parameterization
Rexroth IndraDrive FCS01.1
DOK-INDRV*--FCS01*****-IB01_EN-P
Parameter
Setting value / description / note
Device
Supervisor
Parameter
record
P209
No-load current
S
P
0.1 ... 300.0 A
[
******
]
This value is always calculated automatically from the motor data when parameter >cos
ϕ
<
P206 and parameter >Rated current< P203 are modified.
Note:
For direct input of the value, it must be set as the last value of the motor
data. This is the only way to ensure that the value will not be overwritten.
P210
Increase of static boost
S
P
0 ... 400 %
[ 100 ]
The static boost influences the current which determines the magnetic field. It corresponds
the no-load current of the motor in question, i.e. it is load-independent. For typical
applications, the factory setting of 100% is sufficient.
P211
Increase of dynamic boost
S
P
0 ... 150 %
[ 100 ]
The dynamic boost influences the current which determines the torque. This is a load-
depending factor. Here, too, the factory setting of 100% is considered sufficient for typical
applications.
An excessively high value can result in overcurrent at the FC. Then, the output voltage is
increased excessively under load. An excessively low value results in an excessively low
torque.
P212
Slip compensation
S
P
0 ... 150 %
[ 100 ]
Slip compensation increases - in dependence on the load - the output frequency to keep
the speed of an asynchronous DS motor more or less constant.
When asynchronous DS motors are used and the motor data is set correctly, the factory
setting of 100% is optimum.
When several motors (of different loads or powers) are operated at one FC, slip
compensation P212 should be set =0%. This excludes the possibility of a negative influence.
This also applies for synchronous motors whose design precludes any slip.
P213
Amplification of ISD control
S
P
25 ... 400 %
[ 100 ]
This parameter influences the control dynamics of the current vector control (ISD control) of
the FC. High settings make the controller fast, low settings make it slow.
Depending on the type of application, this parameter must be adjusted, for example to
prevent instable operation.
P214
Rate-action torque
S
P
-200 ... 200 %
[ 0 ]
This function allows for teaching the current controller a value for the torque requirement to
be expected. This function can be used for lifting gears to provide better load transfer
during startup.
Note:
With phase sequence right, motor-driven torques are entered with
positive signs, and regenerative torques are marked with negative
signs. With phase sequence left, it is vice versa.
***
These settings depend upon the selection in parameter P200.
Содержание IndraDrive Fc FCS01
Страница 28: ...5 2 Delivery Rexroth IndraDrive FCS01 1 DOK INDRV FCS01 IB01_EN P ...
Страница 34: ...6 6 Certifications and Types Rexroth IndraDrive FCS01 1 DOK INDRV FCS01 IB01_EN P ...
Страница 56: ...8 20 Installation Rexroth IndraDrive FCS01 1 DOK INDRV FCS01 IB01_EN P ...
Страница 88: ...10 4 Commissioning Rexroth IndraDrive FCS01 1 DOK INDRV FCS01 IB01_EN P ...
Страница 237: ......