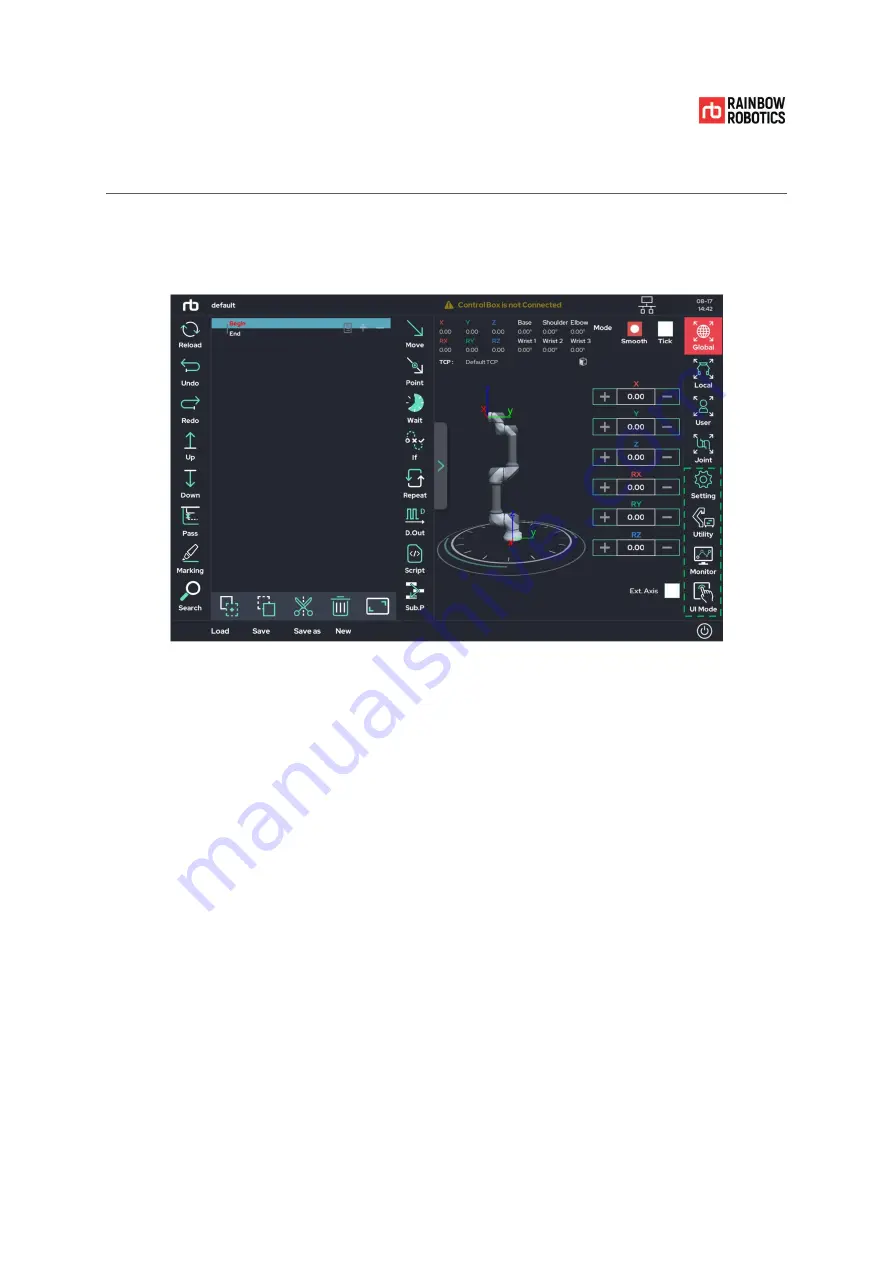
RAINBOW ROBOTICS
RB SERIES _ USER MANUAL
© RAINBOW ROBOTICS Inc. All rights reserved.
316
7.7
OPERATION
UTILITIES
On the right side of the Make screen, there are other utility functions to help a user operate
the system.
Utility
: Comprises a collection of additional functions, such as the posture saving
function, the system input / output information view function, and the system
output test function. These functions are also frequently used.
Setting
: Allows the user to use the jog function, as well as other utility functions
to help the user’s experience.
Monitor
: Provides a window that allows the user to monitor both system and user
variables in real time.
UI Mode
: UI mode can be selected according to the user's level and the user's
purpose.
Содержание RB Series
Страница 1: ...RAINBOw English RB SERIES USER MANUAL V 3 9 1 Update 2021 09...
Страница 2: ...RAINBOW ROBOTICS RB SERIES _ USER MANUAL RAINBOW ROBOTICS Inc All rights reserved 2...
Страница 80: ...RAINBOW ROBOTICS RB SERIES _ USER MANUAL RAINBOW ROBOTICS Inc All rights reserved 80 Program only Mode...
Страница 195: ...RAINBOW ROBOTICS RB SERIES _ USER MANUAL RAINBOW ROBOTICS Inc All rights reserved 195...
Страница 206: ...RAINBOW ROBOTICS RB SERIES _ USER MANUAL RAINBOW ROBOTICS Inc All rights reserved 206...
Страница 265: ...RAINBOW ROBOTICS RB SERIES _ USER MANUAL RAINBOW ROBOTICS Inc All rights reserved 265...