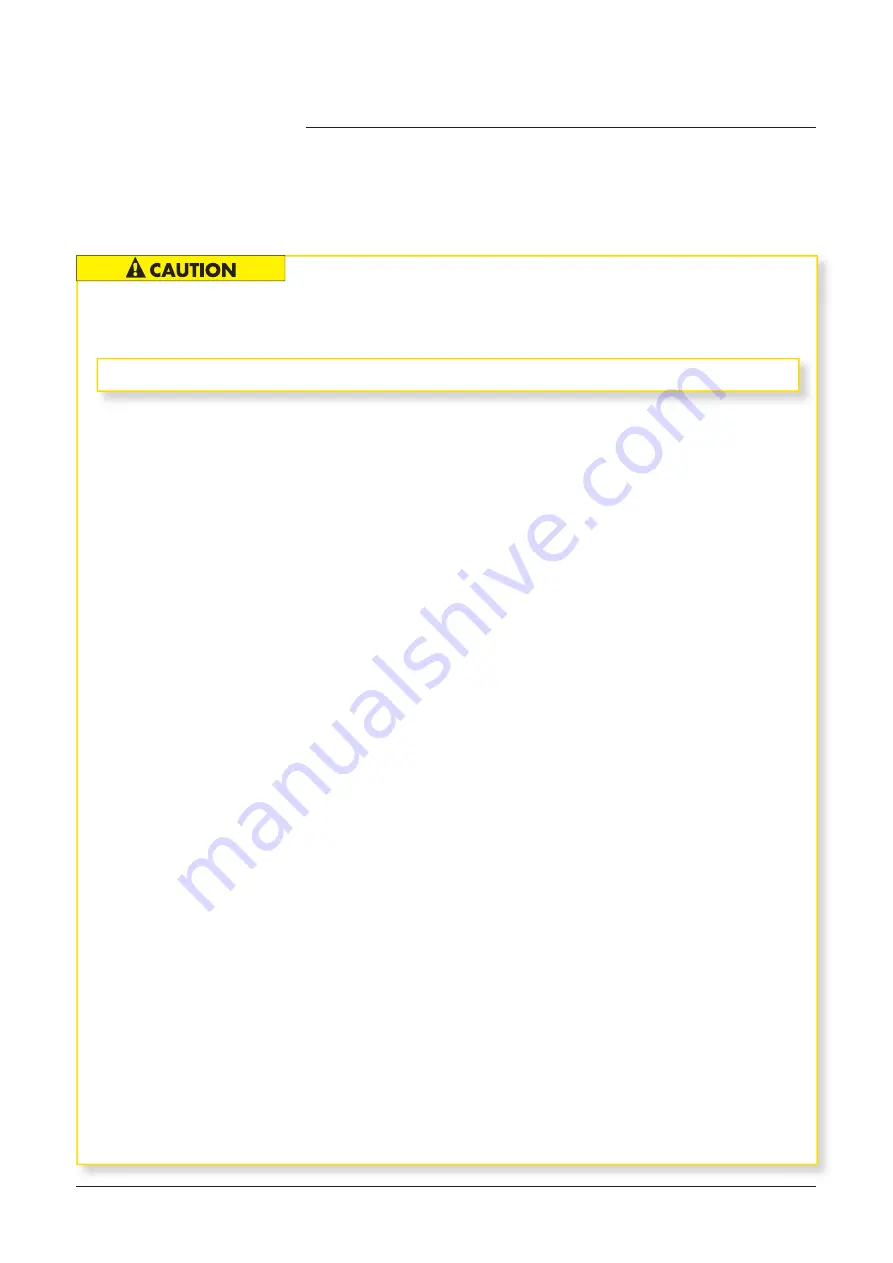
2/3
C 00
Safety recommendations
for harsh processes
G 04128 - Edition 03 - Oct 13
SAFETY INFORMATION related to SIH
4
/H
2
PROCESSES
Processes using high H
2
or SiH
4
flows require extended safety to prevent any problem. In order to avoid
any safety issue or risks relative to process and pumping conditions, it is necessary to set up the pump
with correct settings, following adixen recommendations.
Concerned processes : PECVD Si : (a/μc-Si using both SiH
4
and H
2
) ; PECVD SiN (using SiH
4
)
On these applications, and depending on working conditions (flows ratio and working pressure), two risks
can easily been identified.
– Explosion of Si dust,
– Ignition of SiH
4
/H
2
trapped into powders.
Explosion of Si dust : (PECVD Si)
Some PECVD Si produces a lot of an orange/brown powder which is composed of very thin particles of Si.
Depending on exact process conditions, size of these particles may vary from 0,1 to 100 μm. In this range,
a mix of Si dust and air in a cloud is considered as highly explosive as its ignition energy is very low.
Friction between particles or air flow inrush is sufficient. Overpressure generated by this kind of mix is
10-11 times initial pressure.
Explosion due to ignition of SiH
4
trapped in by-products : (PECVD Si & SiN)
Another well known phenomena is explosion due to trapped silane. As PECVD Si and SiN produce a lot of
powder which deposits into vacuum line, pump, exhaust line… The different layers of powder have the ability
to retain/trap process gases. These gases can be released suddenly and ignite in case of violent air inrush.
Explosion consequences:
An explosion, either in vacuum line or pump or exhaust line, is a complex chemical reaction.. An explosion
can also generate a leak which will generate a second explosion…
Another important point is that vacuum pumps are also compressors. Depending on pressure in volume
to evacuate, pressure in different pump’s stages can be much greater than Atmosphere. Consequently,
explosion can generate very high local overpressure.
GENERAL RECOMMENDATION
It is necessary to pay particular attention to:
Leak tightness of the whole system:
– Be sure there is no air leak on pumping system itself and on vacuum line. Leak rate has to be lower
than 10
-6
hPa.l/sec of Helium. A leak from outside to inside may lead to uncontrolled reaction between
SiH
4
and O
2
. If the leak is big enough, H
2
/O
2
mix could be ignited by decomposition of SiH4. In the
worst case, explosion can occur.
– End user mustguarante vacuum line and exhaust line leak-tightness
– Be sure there is no leak at pump exhaust. An overpressure Helium leak test has to be performed.
Maximum leak rate is 5.10
-5
hPa.l/sec.
N2 purge:
– Be sure pump is purged with N
2
. Air is prohibited.
– This purge could be stopped when process gases are off, but it has to be in a safe and robust procedure.
– Be
sure
N
2
purge warning and alarm are enabled
– Be
sure
N
2
purge is prolonged at least 10 min after pump stop to evacuate residual process gases after
pump stop
Communication with tool:
– global warning and alarm and specific N
2
warning and alarm has to be sent to the tool which must
shut off active gases.
– Immediate corrective actions must be scheduled in case of N
2
signals (warning or alarm).
adixen Vacuum Products - Operating instructions - A3P Series