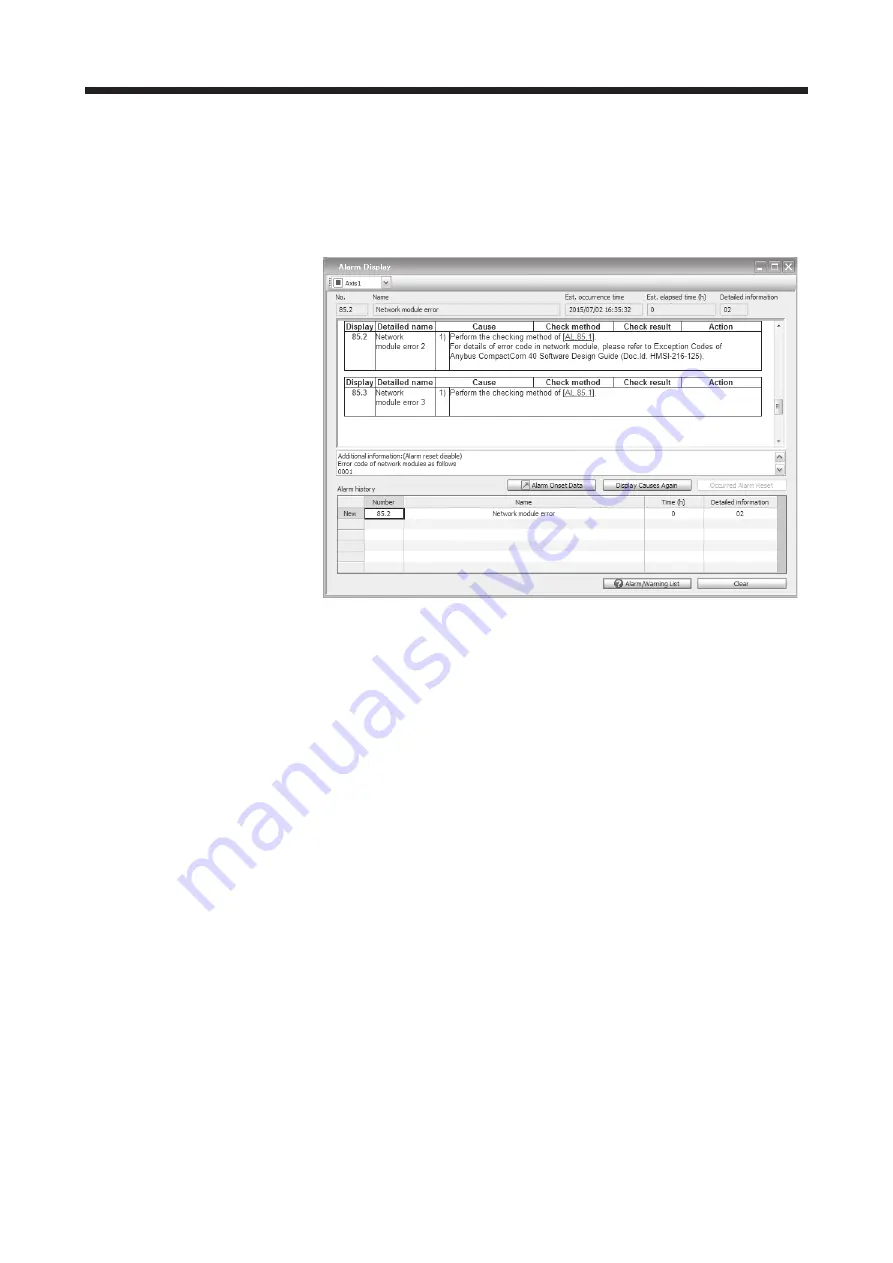
1. TROUBLESHOOTING FOR SERVO AMPLIFIER (DRIVE UNIT)
1 - 129
1.7 Network module error codes
If an error occurs in the network module, a network module error code will be displayed in "Alarm Display" of
MR Configurator2.
For details of the network module error codes, refer to "Exception Codes" of "Anybus CompactCom 40
Software Design Guide (Doc.Id. HMSI-216-125)".
Содержание MELSERVO MR-J4-B-RJ Series
Страница 7: ...2 MEMO ...
Страница 137: ...1 TROUBLESHOOTING FOR SERVO AMPLIFIER DRIVE UNIT 1 130 MEMO ...
Страница 145: ...2 TROUBLESHOOTING FOR MR CV_POWER REGENERATION CONVERTER UNIT 2 8 MEMO ...
Страница 155: ...3 TROUBLESHOOTING FOR MR CR55K 4 RESISTANCE REGENERATION CONVERTER UNIT 3 10 MEMO ...
Страница 171: ...MEMO ...