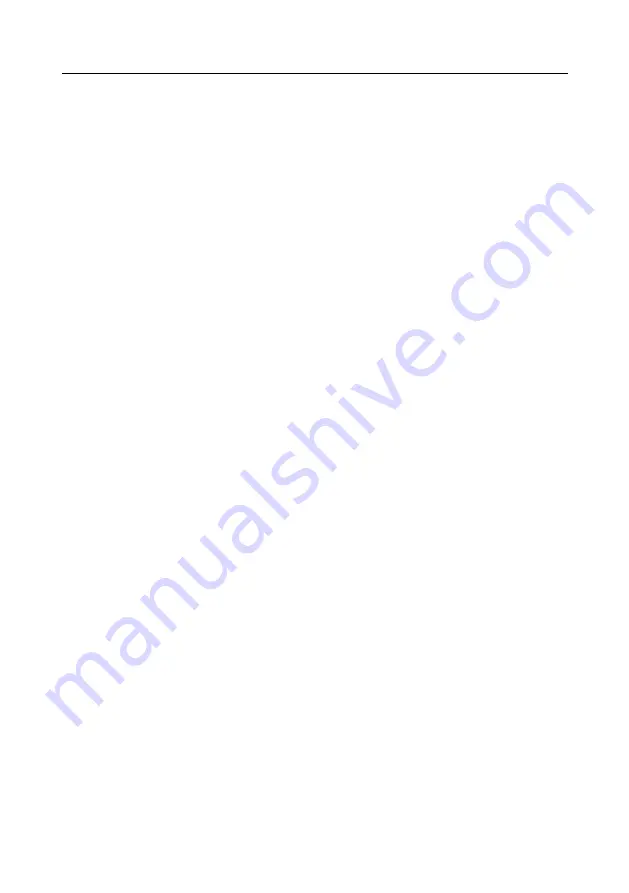
Goodrive350 series high-performance multifunction VFD
Basic operation guidelines
-124-
Step 1
–4: These four steps are the same with the first four steps of the commissioning procedures for
closed-loop vector control, which aim to fulfill the control requirements of closed-loop vector control,
thus realizing spindle positioning function in either position control or speed control mode.
Step 5: Set P22.00.bit0=1 to enable spindle positioning, set P22.00.bit1 to select spindle zero input. If
the system adopts encoder for speed measurement, set P22.00.bit1 to 0 to select Z pulse input; if the
system adopts photoelectric switch for speed measurement, set P22.00.bit1 to 1 to select
photoelectric switch as zero input; set P22.00.bit2 to select zero search mode, set P22.00.bit3 to
enable or disable zero calibration, and select zero calibration mode by setting P22.00.bit7.
Step 6: Spindle zeroing operation
a) Select the positioning direction by setting P22.00.bit4;
b) There are four zero positions in P22 group, you can choose one out of four zeroing positions
by setting zeroing input terminal selection (46, 47) in P05 group. When executing zeroing function,
the motor will stop accurately at corresponding zeroing position according to the set positioning
direction, which can be viewed via P18.10;
c) The positioning length of spindle zeroing is determined by the deceleration time of
accurate-stop and the speed of accurate-stop;
Step 7: Spindle division operation
There are seven scale-division positions in P22 group, you can choose one out of seven
scale-division positions by setting scale-division input terminal selection (48, 49, 50) in P05 group.
Enable corresponding scale-division terminal after the motor stops accurately, and the motor will
check the scale-division position state and switch to corresponding position incrementally, at this point,
you can check P18.09.
Step 8: Priority level of speed control, position control and zeroing
The priority level of speed running is higher than that of the scale division, when the system runs in
scale-division mode, if spindle orientation is prohibited, the motor will turn to speed mode or position
mode.
The priority level of zeroing is higher than that of the scale division.
Scale-division command is valid when the scale-division terminal is from 000 state to non-000 state,
eg, in 000
–011, the spindle executes scale division 3. The transition time during terminal switchover
needs to be less than 10ms; otherwise, wrong scale division command may be executed.
Step 9: Hold positioning
The position loop gain during positioning is P21.03; while the position loop gain in
positioning-completion-hold state is P21.02. In order to keep sufficient position-hold force and ensure
no system oscillation occurred, adjust P03.00, P03.01, P20.05 and P21.02.
Step 10: Positioning command selection (bit6 of P22.00)
Electric level signal: Positioning command (zeroing and scale division) can be executed only when
there is running command or the servo is enabled.