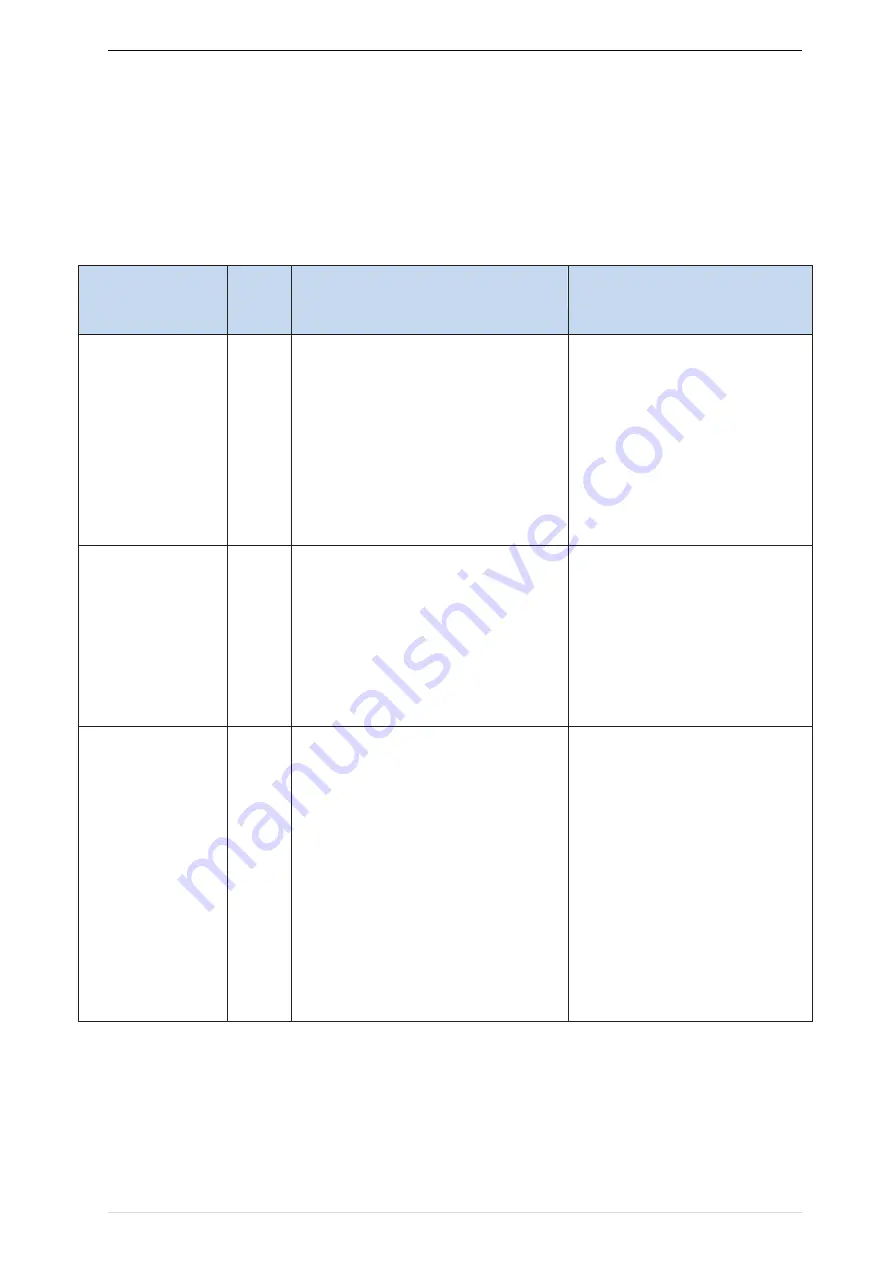
Chapter 6 Fault diagnosis and
solutions
ICON500 high performance vector control frequency inverter user
manual
- 90
-
Chapter 6 Fault Diagnosis and Solution
ICON500 inverter has 24 types of warning information and protection function. In case of abnormal
fault,the protection function will be invoked, the inverter will stop output, and the faulty relay contact
of the inverter will start, and the fault code will be displayed on the display panel of the inverter.
Before consulting the service department, the user can perform self-check according to the prompts
of this chapter, analyze the fault cause and find out solution. If the fault is caused by the reasons as
described in the dotted frame, please consult the agents of inverter or factory directly.
Fault Name
Display
Possible Causes
Solutions
Inverter unit
protection
Er. SC
1: The output circuit is grounded or
short circuited.
2: The connecting cable of the motor is
too long.
3: The IGBT overheat.
4: The internal connections become
loose.
5: The main control board is faulty.
6: The drive board is faulty.
7: The inverter IGBT is faulty.
1: Eliminate external faults.
2: Install a reactor or anoutput
filter.
3: Check the air filter and the
cooling fan.
4: Connect all cables properly.
5: Ask for technical support
6: Ask for technical support
7: Ask for technical support
Ground short circuit
Er.SC1
1. Short circuit of motor to ground
2, the motor and inverter wiring is too
long
3, module overheating
4. The internal wiring of the inverter is
loose
5. Control board is fault
6, Drive board is fault
7, inverter module is fault
1. Replace cable or motor
2. Install reactor or output filter
3. Check whether the air duct is
blocked, the fan is working
properly and eliminate the existing
problems
4. Plug in all the connections
5. Ask for technical support
6. Ask for technical support
7. Ask for technical support
Over current
during
acceleration
Er.OC1
1: The output circuit is grounded or
short circuited.
2: Motor auto-tuning is not performed.
3: The acceleration time is too short.
4: Manual torque boost or V/F curve is
not appropriate.
5: The voltage is too low.
6: The startup operation is performed
on the rotating motor.
7: A sudden load is added during
acceleration.
8: The frequency inverter model is of
too small power class.
1: Eliminate external faults.
2: Perform the motor auto-
Tuning in cold state
3: Increase the acceleration
time.
4: Adjust the manual torque
boost or V/F curve.
5: Adjust the voltage to normal
range.
6: Select rotational speed
tracking restart or start the
motor after it stops.
7: Remove the added load.
8: Select a frequency inverter
Ofhigher power class.