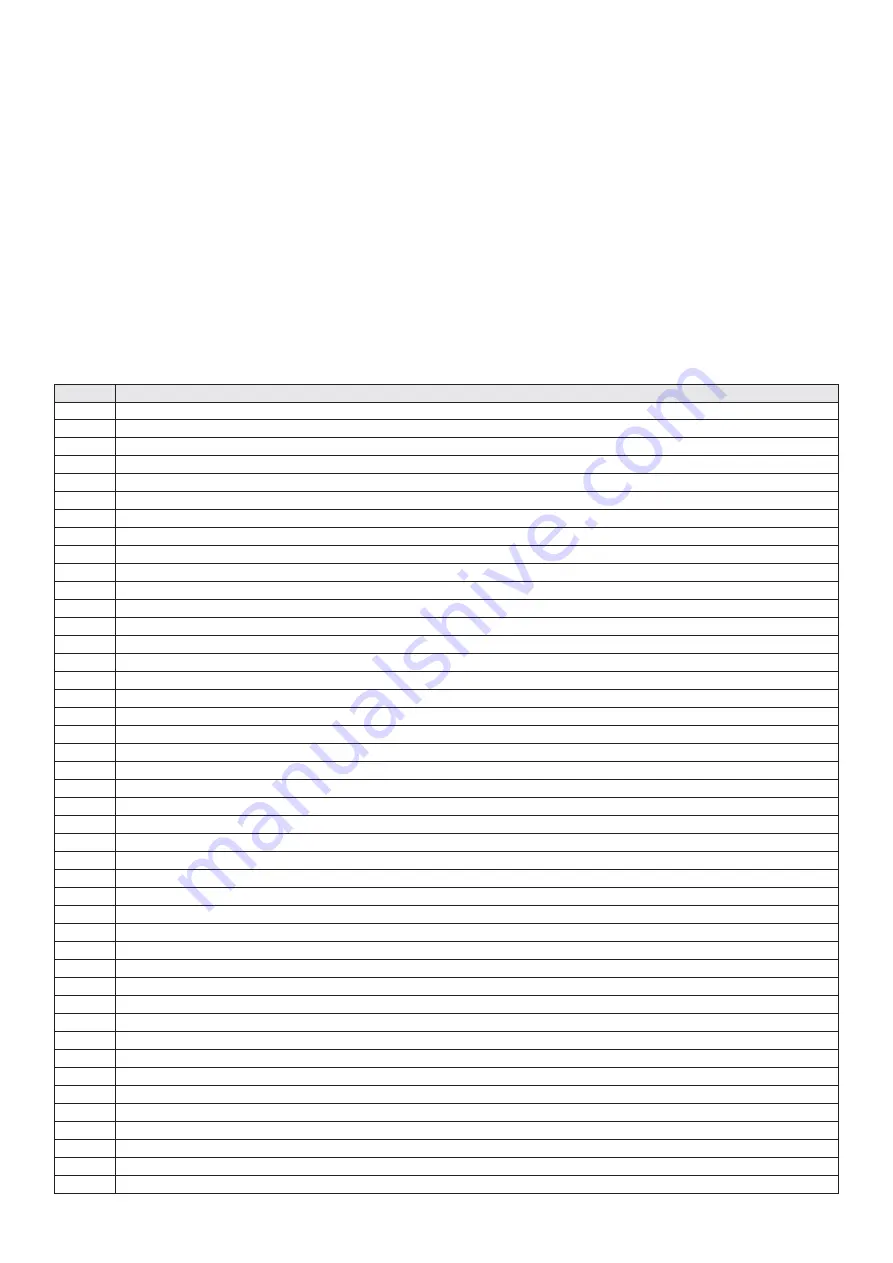
81
CHAPTER 6
SERVICE CODES
6.1 INTRODUCTION
The service codes are used to:
Ø
Calibrate module
Ø
Change setting.
Ø
Show and check measured values of screen of certain signals, system information.
Ø
Upgrade software
6.2 TABLE OF SERVICE CODES
The service codes are not the same for all balancers. The box below indicates all service codes available for this
balancer as follows:
C
Description
0
Set to default profi le and settings
1
Resolution of unbalance readings
2
Suppression of minor unbalance readings
3
Measurement units of unbalance readings
4
Compensation of adaptor unbalance
5
Automatic braking when the wheel guard is opened
6
Number of revolutions for measurement
8
Threshold value for suppression of minor unbalance readings in units selected with C3
10
Saving the user seetings in the the POs (permanent memory)
11
Position brake after measuring run
12
Indication of total numbers of measurement runs-> Type of counters depends on brand
13
Starting measurement run by closing the wheel guard
14
User calibration
21
Indication of the program version number
22
Lock power clamp in clamped position
23
Change pedal functionality (down= brake, up=(un)clamp or opposite)
28
Display the last 10 error codes
43
Reset counters
45
Unbalance Calculation parameters
47
Select machine model
54
Checking the incremental encoder on the main shaft
55
Indication the line voltage
56
Indication of the circuit state of the wheel guard switch
57
Indication of temperature
59
Indication of the residual unbalance compensated for using code C84
60
Motor
: Indication of RPM of main shaft
61
Indication of correction values for user calibration
63
Continuous measurement (with statistics)
64
Indication of the transducer sensitivity as measured with C code 83
66
Display calibration values as measured with C code 83 (virtual dimensions)
67
Display phase stability of the vibratory system as measured with C code 83
71
Display angular deviation of the vibratory system as measured with C code 83
72
Measurement of angular deviation
74
Indication of position counter and basic incremental encoder test
75
Display values from AD converter
80
Calibration of the inner SAPE gauge arm and the AutoStopSystem
81
Measuring the adaptor fl ange and the zero plane.
82
Calibration of the outer Sonar sensor
83
Calibration of the unbalance measurement with wheel/test rotor.
84
Compensation of unbalance of main shaft
85
Copy content of serial EEPROM (EEP) from micro-controller EEP to incremental encoder EEP.
86
Copy content of serial EEPROM (EEP) from incremental encoder EEP to micro-controller EEP.
88
Calibration of the 12 o’clock position for fi tting position of weights
90
Saving the adjustments data in the PO’s
SM HOF GEODYNA 7600 Rel.D