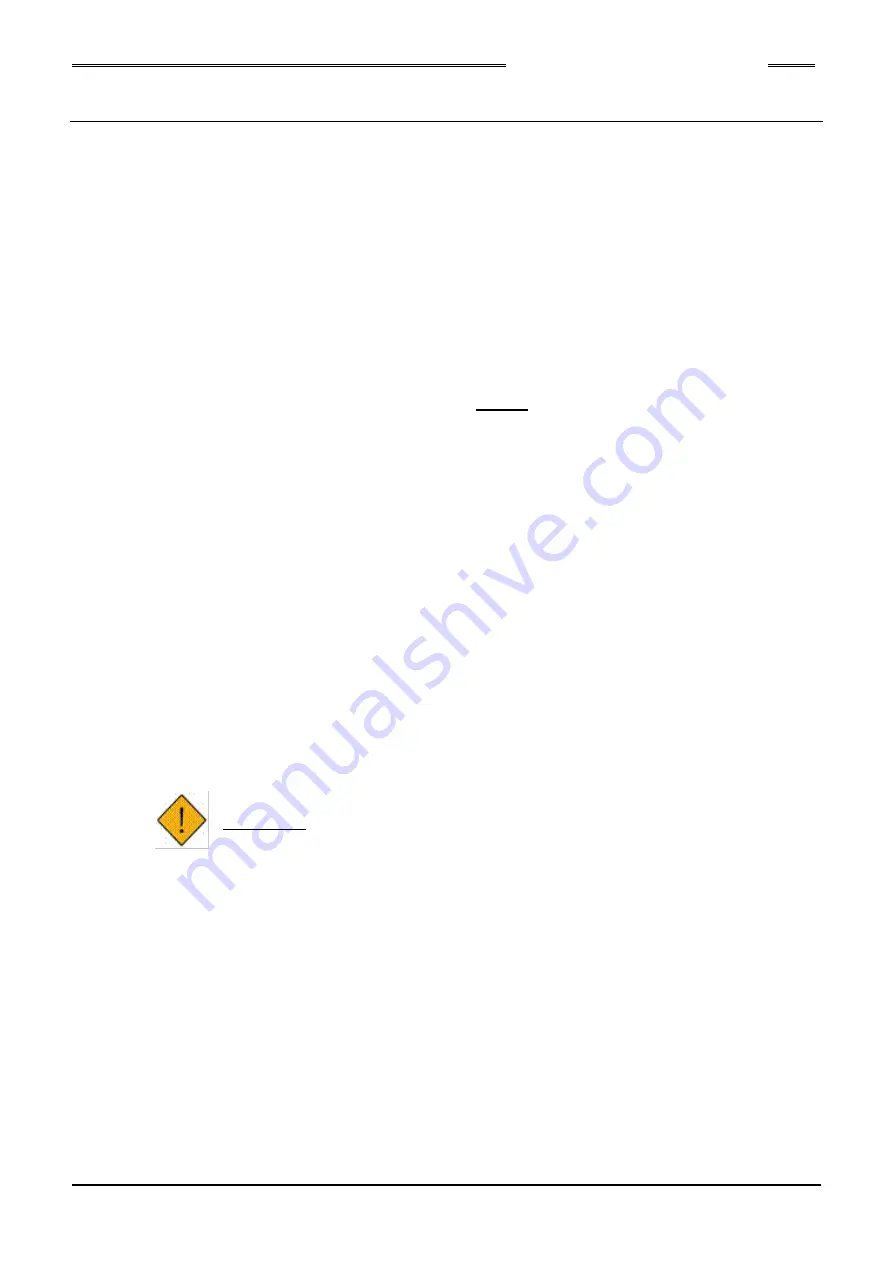
Chapter 6 Fastening Operation
PAGE 6-37
Recommended Parameter Set-up for Tubenut Head
The following parameters are recommended for setting up the Tubenut head function.
1.
Gear Head Option Setup
[SYS], [D-No]-03
6 (Default Setting “0”)
**(Can only be set using the front display keypad)
Change for use with Tubenut head
(Set as below)
0: Standard Head
1
: Tubenut Head (Bottom socket - CW fastening)
2
: Tubenut Head (Top Socket - CCW fastening)
2.
External Gear Ratio
[SYS], [D-No]-04
(Can be changed using software)
Default is “
1.000
”.
If the gear ratio is other than 1:1, then the gear ratio must be adjusted
here or torque/angle readings will not be correct when fastening.
(ex. If gear ratio is 1:1.132, then “1.132” should be entered here)
WARNING: Setup proper CW / CCW rotation PRIOR to running the tool with the Tubenut
head attached or Tubenut Head damage may occur! (The Tubenut head stop detail
which re-
aligns the “open” slot in the socket gear may be broken if too much force is
applied)
3.
Calibration Torque [PAR]-01(thru-64), [D-No]-100
This value is used to adjust the calibration of the tool / tubenut gearing. Typically tubenut
heads will have a 20
– 35% loss of torque through the gearing and minor adjustments can
be made using this value. Large torque losses (that cannot be adjusted in the range of
this setting) must be adjusted internally in the Torque transducer internal settings (tool ID)
This value changes with tool size and capacity.
4.
Torque Inhibit Limit [PAR]-01(thru-64), [D-No]-111
When using the Tubenut function, the Torque Inhibit Limit parameter sets the MAX.
amount of torque that can be sensed during the Torque Inhibit Revolution setting. This is
used to set the max. torque to be sensed during the start of rotation of the socket or until
the socket “U” opening moves to a closed position.
This will protect from damage
anything being inserted into the path of the socket as it rotates in the OPEN space.
If this torque value is exceeded during the Torque Inhibit Revolution (Work
– 01 (thru-16)
D-No-61), a REJECT will result.
This cannot be set too low or nuisance REJECTS will
occur during normal motor start-up.
Recommended setting: .75
– 1.5Nm
NOTE: This setting will vary by tool size and Tubenut head configuration.
WARNING!
–
Do not set this ABOVE the recommended setting or personnel injury
may result!
5.
Torque Inhibit Angle [PAR]-01(thru-64), [D-No]-205
Set Torque Inhibit angle so that the torque can be checked during motor start-up (Just
enough angle revolution for the socket to close the “U” opening) Recommended setting:
15 - 30degrees
6.
Initial Time [PAR]-01(thru-64), [D-No]-310
Set Initial Time so that revolution time/speed is slow during motor start-up (the time that
the socket is rotating in the socket “U” opening)
Recommended setting: .4sec
7.
Initial Speed [PAR]-01(thru-64), [D-No]-400
Set Initial Speed for slow rotation while socket is rotating through the “U” opening.
Recommended setting: 30 - 60rpm max.
8.
Reverse 1 Speed [PAR]-01(thru-64), [D-No]-405
Reverse speed is used to re-align the socket after a fastening.
Recommended setting: 40 - 60 rpm max.
Содержание Handheld Nutrunner HFC3000
Страница 2: ...www fec usa com Copyright 2017 FEC AUTOMATION SYSTEMS All Rights Reserved ...
Страница 14: ...Notes ...
Страница 15: ...Chapter 1 Outline PAGE 1 1 Chapter 1 Outline 1 ...
Страница 21: ...Chapter 2 Specifications PAGE 2 1 Chapter 2 Specifications 2 ...
Страница 28: ...Chapter 2 Specifications PAGE 2 8 Blank Page ...
Страница 29: ...Chapter 3 Sysytem Description PAGE 3 1 Chapter 3 System Description 3 ...
Страница 36: ...Chapter 3 System Description PAGE 3 8 Memo ...
Страница 37: ...Chapter 4 Installation and Wiring PAGE 4 1 Chapter 4 Installation Wiring 4 ...
Страница 67: ...Chapter 5 Power Up and Operational Tests PAGE 5 1 Chapter 5 Power Up and Operational Tests 5 ...
Страница 71: ...Chapter 6 Fastening Operation PAGE 6 1 Chapter 6 Fastening Operation 6 ...
Страница 151: ...Chapter 7 Troubleshooting PAGE 7 1 Chapter 7 Troubleshooting 7 ...
Страница 169: ...Chapter 8 Options PAGE 8 1 Chapter 8 Options 8 ...
Страница 181: ...Chapter 9 Fieldbus I O Interfaces PAGE 9 1 Chapter 9 Fieldbus I O Interfaces 9 ...
Страница 207: ...Chapter 9 Fieldbus I O Interfaces PAGE 9 27 9 3 2 Description of the hardware RUN LED ERROR LED CC Link Connector ...
Страница 229: ...Chapter 9 Fieldbus I O Interfaces PAGE 9 49 Blank Page ...
Страница 230: ......
Страница 231: ......