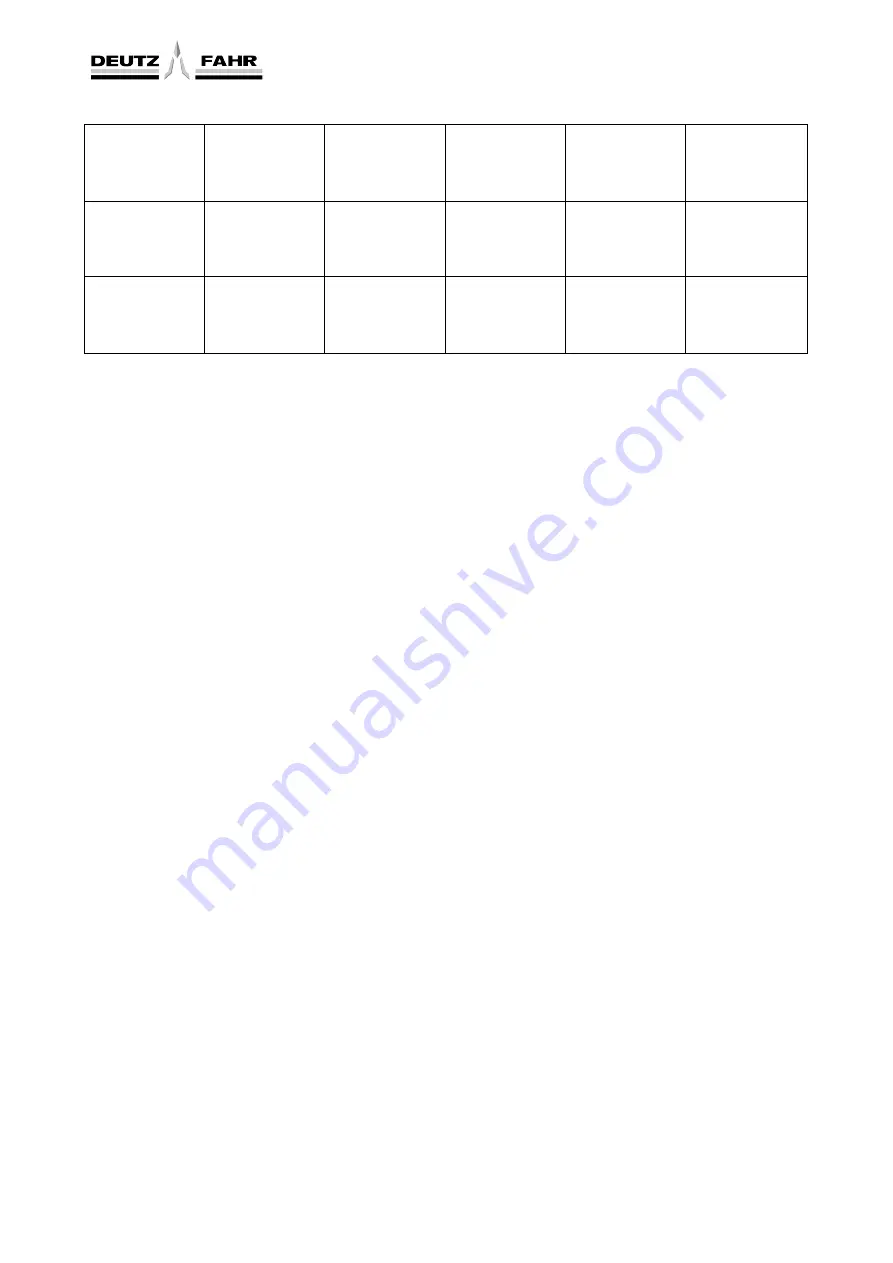
320
Fig. 8-67
1.
Sun gear
2.
Planet
wheel
3.
Planetary
carrier
4.
Needle
roller
5.
Planetary
gear shaft
6.
Ring gear
7.
Bolt
8.
Spacer bush 9.
Overturning
bearing
10.
Drive shaft
housing
11.
Drive shaft
12.
Overturning
bearing
13.
Spacer bush 14.
Adjustable
pad
15.
Locking
plate
The final drive employs a planetary gear mechanism. The planetary gear mechanism consists of an active sun gear,
a fixed ring gear, a driven planetary gear carrier, and planetary gears. The sun gear is integrated with half shaft. The
spine at the front end engages with the half shaft gear. The ring gear is fixed between the drive shaft housing and
the brake housing. The three planetary gears engaging with the sun gear and ring gear are installed to the planetary
gear carrier via the needle bearings and planetary gear shaft. The drive shaft for the planetary gear mechanism is
supported on the drive shaft housing by two radial ball bearings. The drive shaft is connected to the planetary gear
carrier via spline, and fixed with the locking screw. In order to improve engagement of the sun gear with the
planetary gears to achieve uniform load distribution, no fixed support is provided for the sun gear, in other words,
the sun gear is at the floating status. A floating clearance G = (0.2 ~ 0.3) mm exists between the planetary gear
carrier and spacer.
8.11.4.2.Final drive Adjustment
Floating clearance between planetary gear carrier and spacer has already been factory adjusted as G= (0.2~0.3) mm,
removing necessity of adjustment during use of the tractor. However, in the case of overhaul of tractor or
replacement of planetary gear mechanism, this parameter shall be adjustment. Adjustment: measure the distance
from drive shaft to bearing end face A. Measure the planetary gear carrier spline hole depth B and the spacer
thickness C. Calculate the adjusting shim thickness
δ
= A- (B + C + 0.2 ~ 0.3) mm. Place a shim of this thickness
in the position shown in the figure. Tighten the drive shaft locking screw, and lock the drive shaft using the locking
tab.
8.11.5.Adjustment of front wheel hub bearings
Содержание FL35-70HP Series
Страница 21: ...Product Mark 20 1 Security Considerations ...
Страница 57: ...Product Mark 56 Fig 1 35 Fig 1 36 ...
Страница 58: ...Product Mark 57 Fig 1 37 Fig 1 38 ...
Страница 62: ...Product Mark 61 Rear transverse board safety label To prevent personal injury do not ride or stand here ...
Страница 70: ...69 2 Product Mark ...
Страница 74: ...73 Page Left Intentionally Blank ...
Страница 75: ...Product Description 74 3 Product Description ...
Страница 77: ...Product Description 76 Fig 3 2 3 1 2 Appearance of tractor equipped with cab ...
Страница 81: ...Product Description 80 ...
Страница 84: ...Product Description 83 3 7 Notice Check whether the steering wheel is fixed firmly before driving ...
Страница 113: ...Product Description 112 ...
Страница 124: ...Electrical system 123 4 Operation Instructions ...
Страница 157: ...Electrical system 156 ...
Страница 162: ...Electrical system 161 Fig 4 32 Three point linkage Model 2 ...
Страница 168: ...Electrical system 167 Fig 4 41 Diagram for movement of the hitch mechanism configuration 3 Wheels ...
Страница 189: ...Electrical system 188 5 Wheels ...
Страница 208: ...Electrical system 207 6 Electrical System ...
Страница 230: ...Electrical system 229 requirements 6 6 Electrical Schematic Diagram ...
Страница 235: ...234 7 On board Spare Parts Tools and Quick wear Parts ...
Страница 241: ...240 ...
Страница 242: ...241 8 Maintenance Specification ...
Страница 288: ...287 Fig 8 35 ...
Страница 338: ...Operation Instructions 337 9 Troubleshooting ...
Страница 353: ...352 10 Tractor Storage and Unpack ...
Страница 358: ...Tractor Storage and Unpack 357 11 Delivery Acceptance and Transportation ...
Страница 361: ...360 ...
Страница 362: ...361 12 Disassembly and Disposal ...
Страница 365: ...Warranty Contents 364 13 Warranty Contents ...
Страница 411: ...Appendix 410 15 Appendix ...