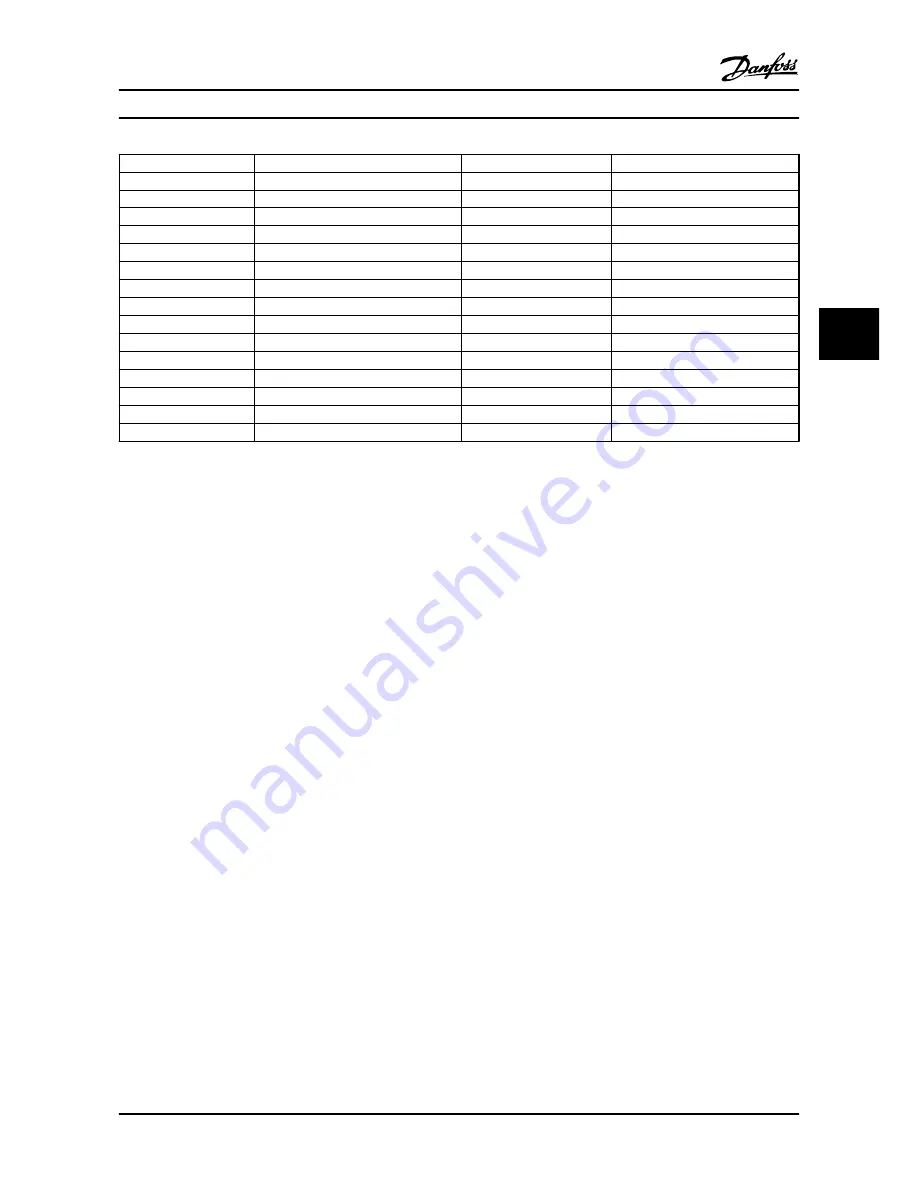
Terminal number
Terminal description
Parameter number
Factory default
1+2+3
Terminal 1+2+3-Relay1
5-40
No operation
4+5+6
Terminal 4+5+6-Relay2
5-40
No operation
12
Terminal 12 Supply
-
+24 V DC
13
Terminal 13 Supply
-
+24 V DC
18
Terminal 18 Digital Input
5-10
Start
19
Terminal 19 Digital Input
5-11
No operation
20
Terminal 20
-
Common
27
Terminal 27 Digital Input/Output
5-12/5-30
Coast inverse
29
Terminal 29 Digital Input/Output
5-13/5-31
Jog
32
Terminal 32 Digital Input
5-14
No operation
33
Terminal 33 Digital Input
5-15
No operation
37
Terminal 37 Digital Input
-
Safe Stop
42
Terminal 42 Analog Output
6-50
Speed 0-HighLim
53
Terminal 53 Analog Input
3-15/6-1*/20-0*
Reference
54
Terminal 54 Analog Input
3-15/6-2*/20-0*
Feedback
Table 5.9 Terminal Connections
Very long control cables and analog signals may, in rare
cases and depending on the installation, result in 50/60 Hz
ground loops due to noise from line power supply cables.
If this occurs, break the shield or insert a 100 nF capacitor
between shield and chassis.
NOTE!
The common of digital / analog inputs and outputs should
be connected to separate common terminals 20, 39, and
55. This will prevent ground current interference among
groups. For example, it prevents switching on digital
inputs from disturbing analog inputs.
NOTE!
Control cables must be shielded/armored.
5.2.3 Motor Cables
See section
General Specifications
for maximum
dimensioning of motor cable cross-section and length.
•
Use a shielded/armored motor cable to comply
with EMC emission specifications.
•
Keep the motor cable as short as possible to
reduce the noise level and leakage currents.
•
Connect the motor cable shield to both the de-
coupling plate of the Adjustable frequency drive
and to the metal cabinet of the motor.
•
Make the shield connections with the largest
possible surface area (cable clamp). This is done
by using the supplied installation devices in the
Adjustable frequency drive.
•
Avoid mounting with twisted shield ends
(pigtails), which will spoil high frequency
shielding effects.
•
If it is necessary to split the shield to install a
motor isolator or motor relay, the shield must be
continued with the lowest possible HF
impedance.
F frame Requirements
F1/F3 requirements: Motor phase cable quantities must be
multiples of 2, resulting in 2, 4, 6, or 8 (1 cable is not
allowed) to obtain equal amount of wires attached to both
inverter module terminals. The cables are required to be
equal length within 10% between the inverter module
terminals and the first common point of a phase. The
recommended common point is the motor terminals.
F2/F4 requirements: Motor phase cable quantities must be
multiples of 3, resulting in 3, 6, 9, or 12 (1 or 2 cables are
not allowed) to obtain equal amount of wires attached to
each inverter module terminal. The wires are required to
be equal length within 10% between the inverter module
terminals and the first common point of a phase. The
recommended common point is the motor terminals.
Output junction box requirements: The length, a minimum
of 8 ft [2.5 m], and quantity of cables must be equal from
each inverter module to the common terminal in the
junction box.
How to Install
VLT
®
HVAC Drive Design Guide
MG11BB22 - VLT
®
is a registered Danfoss trademark
5-11
5
5
Содержание VLT HVAC Drive FC 100 Series
Страница 10: ...How to Read this Design Gui VLT HVAC Drive Design Guide 1 6 MG11BB22 VLT is a registered Danfoss trademark 1 1...
Страница 56: ...Introduction to VLT HVAC D VLT HVAC Drive Design Guide 2 46 MG11BB22 VLT is a registered Danfoss trademark 2 2...
Страница 126: ...How to Install VLT HVAC Drive Design Guide 5 38 MG11BB22 VLT is a registered Danfoss trademark 5 5...
Страница 136: ...Application Examples VLT HVAC Drive Design Guide 6 10 MG11BB22 VLT is a registered Danfoss trademark 6 6...
Страница 160: ...RS 485 Installation and Set VLT HVAC Drive Design Guide 7 24 MG11BB22 VLT is a registered Danfoss trademark 7 7...