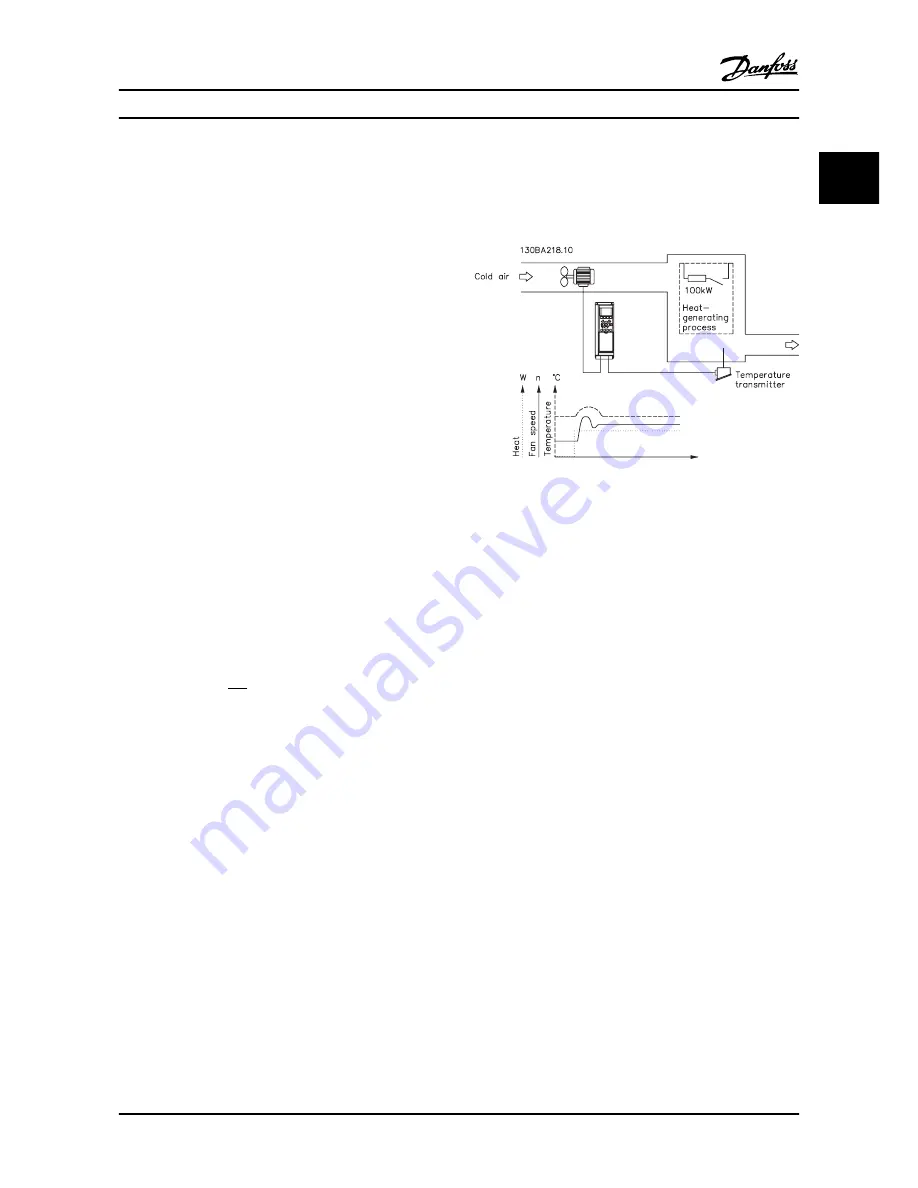
The Remote Reference is comprised of:
•
Preset references.
•
External references (analog inputs, pulse
frequency inputs, digital potentiometer inputs
and serial communication bus references).
•
The preset relative reference.
•
Feedback controlled setpoint.
Up to 8 preset references can be programmed in the drive.
The active preset reference can be selected using digital
inputs or the serial communications bus. The reference can
also be supplied externally, most commonly from an
analog input. This external source is selected by one of the
3 Reference Source parameters (
3-15 Reference 1 Source
,
3-16 Reference 2 Source
and
3-17 Reference 3 Source
).
Digipot is a digital potentiometer. This is also commonly
called a speed up/speed down control, or a floating point
control. To set it up, one digital input is programmed to
increase the reference while another digital input is
programmed to decrease the reference. A third digital
input can be used to reset the digipot reference. All
reference resources and the bus reference are added to
produce the total external reference. The external
reference, the preset reference or the sum of the two can
be selected to be the active reference. Finally, this
reference can by be scaled using
3-14 Preset Relative
Reference
.
The scaled reference is calculated as follows:
Reference = X + X ×
(
Y
100
)
Where X is the external reference, the preset reference or
the sum of these and Y is
3-14 Preset Relative Reference
in
[%].
If Y,
3-14 Preset Relative Reference
is set to 0%, the
reference will not be affected by the scaling.
2.8.9 Example of Closed-loop PID Control
The following is an example of a closed-loop control for a
ventilation system:
Figure 2.28
In a ventilation system, the temperature is to be
maintained at a constant value. The desired temperature is
set between 23° and 95°F [-5°–+35°C] using a 0–10 volt
potentiometer. Because this is a cooling application, if the
temperature is above the setpoint value, the speed of the
fan must be increased to provide more cooling air flow.
The temperature sensor has a range of 14°–104°F [-10°–
+40°C] and uses a two-wire transmitter to provide a 4–20
mA signal. The output frequency range of the Adjustable
frequency drive is 10 to 50Hz.
1.
Start/Stop via switch connected between
terminals 12 (+24V) and 18.
2.
Temperature reference via a potentiometer (23°–
95° F [-5°–+35
°
C], 0–10 V) connected to terminals
50 (+10 V), 53 (input) and 55 (common).
3.
Temperature feedback via transmitter (14°–104°F
[-10°–+40
°
C], 4–20 mA) connected to terminal 54.
Switch S202 behind the LCP set to ON (current
input).
Introduction to VLT® HVAC D...
VLT
®
HVAC Drive Design Guide
MG11BB22 - VLT
®
is a registered Danfoss trademark
2-29
2
2
Содержание VLT HVAC Drive FC 100 Series
Страница 10: ...How to Read this Design Gui VLT HVAC Drive Design Guide 1 6 MG11BB22 VLT is a registered Danfoss trademark 1 1...
Страница 56: ...Introduction to VLT HVAC D VLT HVAC Drive Design Guide 2 46 MG11BB22 VLT is a registered Danfoss trademark 2 2...
Страница 126: ...How to Install VLT HVAC Drive Design Guide 5 38 MG11BB22 VLT is a registered Danfoss trademark 5 5...
Страница 136: ...Application Examples VLT HVAC Drive Design Guide 6 10 MG11BB22 VLT is a registered Danfoss trademark 6 6...
Страница 160: ...RS 485 Installation and Set VLT HVAC Drive Design Guide 7 24 MG11BB22 VLT is a registered Danfoss trademark 7 7...