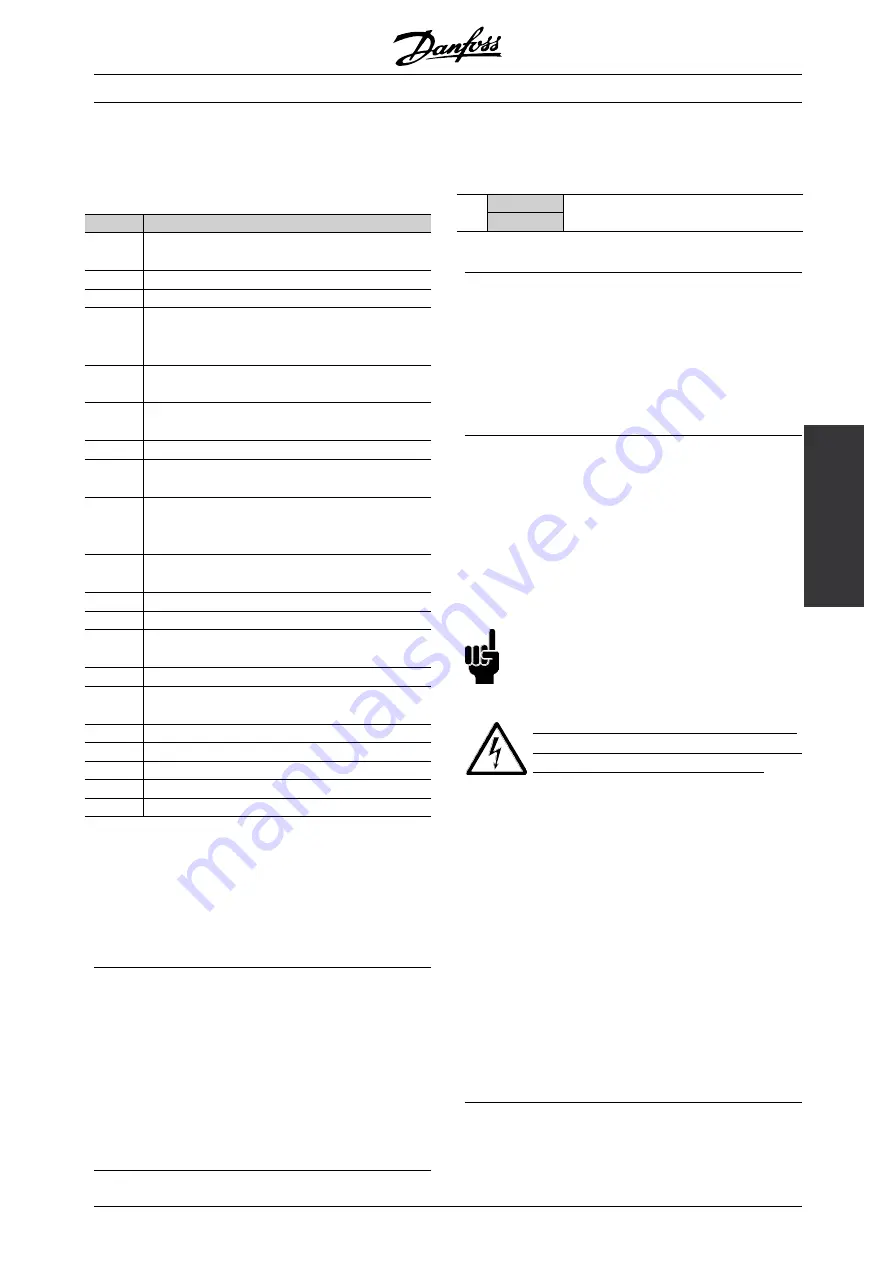
VLT
®
FCD Series
Installation
■
Electrical installation, control terminals
See section entitled
Earthing of screened/armoured
control cables
in the Design Guide for the correct
termination of control cables.
No.
Function
01-03
Relay outputs 01-03 can be used for
indicating status and alarms/warnings.
12
24 V DC voltage supply.
18-33
Digital inputs.
20, 55
Common frame for input
and output terminals. Can be separated with switch
S100
31a,
31b
Motor thermistor
35
Common (-) for external 24 V control back up
supply. Optional.
36
Ex 24 V control back up supply. Optional.
42
Analog output for displaying frequency,
reference, current or torque.
46
Digital output for displaying status,
warnings or alarms, as well as
frequency output.
50
+10 V DC supply
voltage for potentiometer
53
Analogue voltage input 0 - +/- 10 V DC.
60
Analogue current input 0/4 - 20 mA.
67
+ 5 V DC supply voltage
to Profibus.
68, 69
Fieldbus serial communication*
70
Ground for terminals 67, 68 and 69.
Normally this terminal is not to be used.
D
For future use
V
+5V, red
P
RS485(+), LCP2/PC, yellow
N
RS485(-), LCP2/PC, green
G
OV, blue
* See
VLT 2800/FCM 300/FCD 300 Profibus DP
V1 Operating Instructions
(MG.90.AX.YY),
VLT
2800/FCD 300 DeviceNet Operating Instructions
(MG.90.BX.YY) or
FCD 300 AS-interface Operating
Instructions
(MG.04.EX.YY).
■
PC communication
Connect to terminals P and N for PC-access to single
parameters. Motor and field bus communication
should be stopped before performing automatic
transfer of multiple parameters.
On non-fieldbus and Profibus variants, terminals
68 and 69 can be used provided Profibus
communication is stopped.
■
Relay connection
See parameter 323
Relay output
for programming
of relay output.
No.
01
- 02
1 - 2 make (normally open)
01
- 03
1 - 3 break (normally closed)
■
LCP 2 plug, optional
An LCP 2 control unit can be connected to a
plug which is optionally mounted in the housing.
Ordering number: 175N0131.
LCP control units with ordering number 175Z0401
are not to be connected.
■
Installation of 24 Volt external supply (optional)
24 V external DC supply can be used as low-voltage
supply to the control card. This enables full
operation of the LCP2 and serial bus (incl. parameter
setting) without connection to mains.
Please note that a warning of low voltage will
be given when 24 V DC has been connected;
however there will be no tripping.
NB!:
Use 24 V DC supply of type PELV to ensure
correct galvanic isolation (type PELV) on the
control terminals of the VLT frequency converter.
Beware of unintended start of the motor, if
the mains power is applied during operation
on the external 24 V back up supply.
■
Software version 1.5x
A Field bus equipped FCD shows the status
Unit
ready
even with bridged terminals 12-27 and cannot
be set into RUNNING mode by digital inputs alone
until one of the following parameters is set:
-
Par. 502 is set to
Digital input
or
Logic and
or
-
Par. 833 or 928 is set to
Disable
or
-
Par. 678 is set to
Standard version
The field bus status word at power up might be
different (typically 0603h instead of 0607h) until the
first valid control word is sent. After sending the first
valid control word (bit 10 = Data valid) the status
is exactly as in earlier software versions.
MG.04.B7.02 - VLT is a registered Danfoss trademark
21