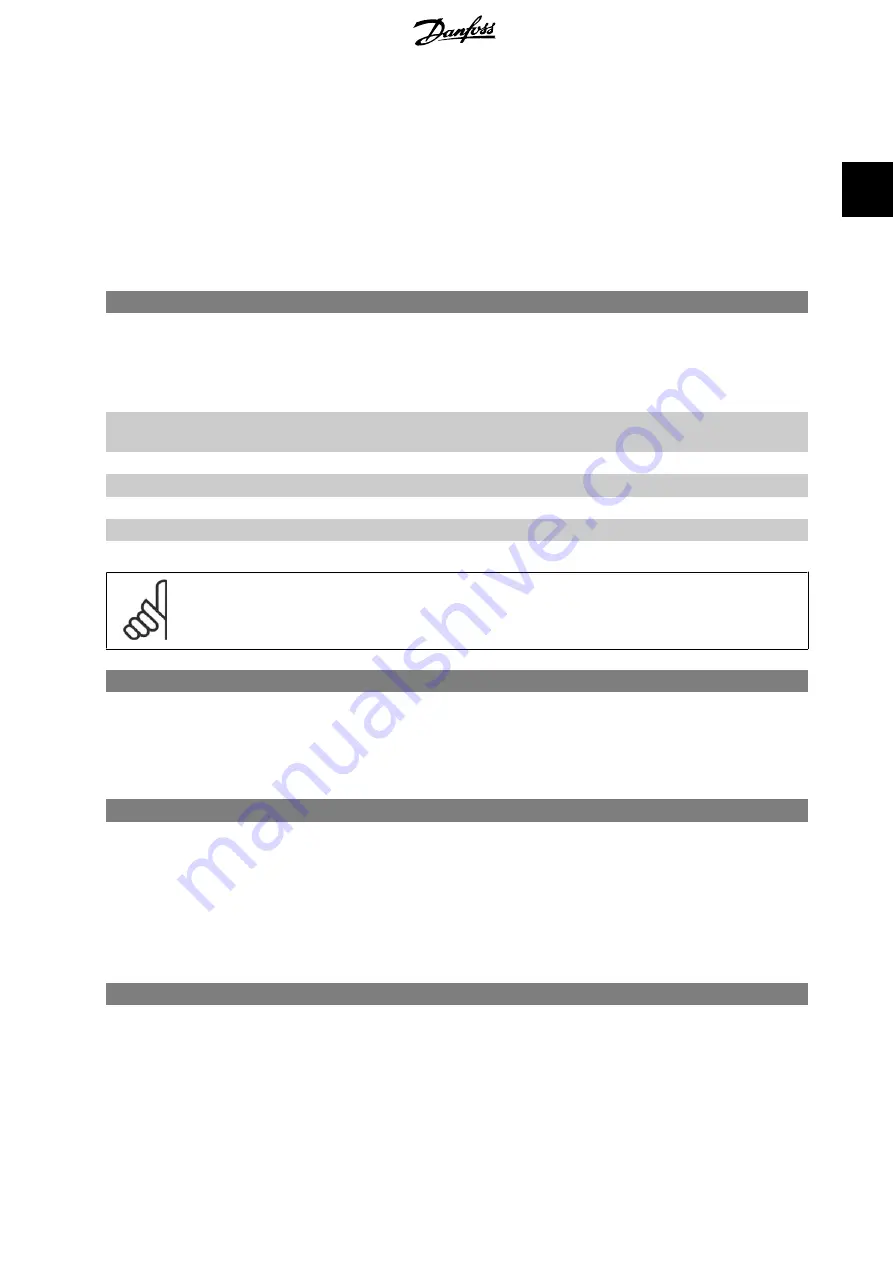
2.10. Parameters: Controllers
2.10.1. 7-** Controllers
Parameter group for configuring application controls.
2.10.2. 7-0* Speed PID Ctrl.
Parameters for configuring the speed PID control.
7-00 Speed PID Feedback Source
Option:
Function:
Select the encoder for closed loop feedback.
The feedback may come from a different encoder (typically mounted on the application itself) than the motor
mounted encoder feedback selected in par. 1-02.
This parameter cannot be adjusted while the motor is running.
[0]
Motor feedb. p.1-02
(FC 302 only)
[1]
24V encoder
[2]
MCB 102
[3]
MCB 103
[4]
MCO encoder 1
[5]
MCO encoder 2
NB!
If separate encoders are used (FC 302 only) the ramp settings parameters in the following groups: 3-4*, 3-5*, 3-6*, 3-7* and 3-8*
must be adjusted according to the gear ratio between the two encoders.
7-02 ProportionalGain
Range:
Function:
Size related [0.000 - 1.000]
Enter the speed controller proportional gain. The proportional gain amplifies the error (i.e. the deviation between
the feedback signal and the set-point). This parameter is used with par. 1-00
Speed open loop
[0] and
Speed
closed loop
[1] control. Quick control is obtained at high amplification. However if the amplification is too great,
the process may become unstable.
7-03 Speed PID Integral Time
Range:
Function:
8.0 ms
*
[2.0 - 20000.0 ms]
Enter the speed controller integral time, which determines the time the internal PID control takes to correct
errors. The greater the error, the more quickly the gain increases. The integral time causes a delay of the signal
and therefore a dampening effect, and can be used to eliminate steady state speed error. Obtain quick control
through a short integral time, though if the integral time is too short, the process becomes unstable. An exces-
sively long integral time disables the integral action, leading to major deviations from the required reference,
since the process regulator takes too long to regulate errors. This parameter is used with
Speed open loop
[0]
and
Speed closed loop
[1] control, set in par. 1-00
Configuration Mode
.
7-04 Speed PID Differentiation Time
Range:
Function:
30.0 ms [0.0 - 200.0 ms]
Enter the speed controller differentiation time. The differentiator does not react to constant error. It provides
gain proportional to the rate of change of the speed feedback. The quicker the error changes, the stronger the
gain from the differentiator. The gain is proportional with the speed at which errors change. Setting this param-
eter to zero disables the differentiator. This parameter is used with par. 1-00
Speed closed loop
[1] control.
FC 300 Programming Guide
2. How to Programme
MG.33.M3.02 - VLT
®
is a registered Danfoss trademark
101
2