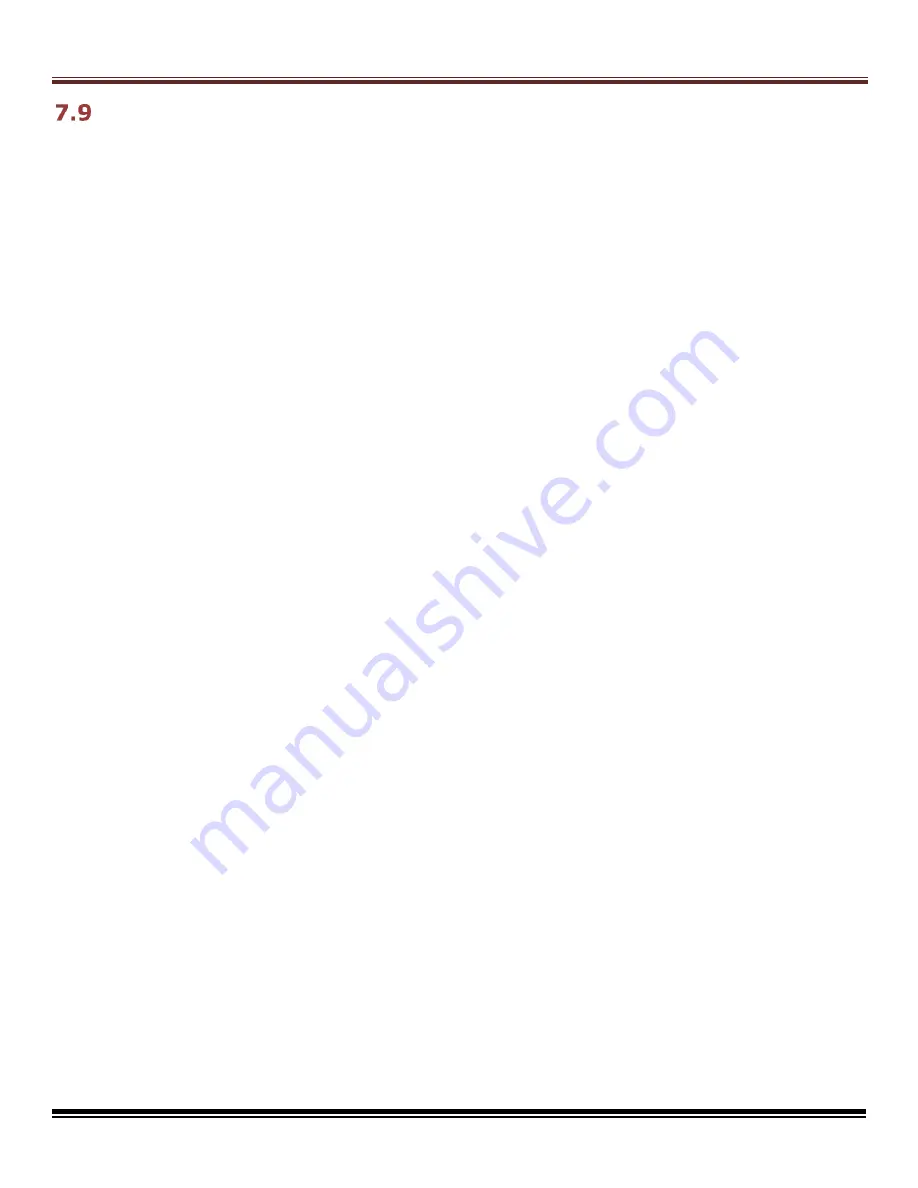
Accelnet Plus Micro Modules User Guide
16-01687 Rev 03
Copley Controls
Page 128 of 139
P
OSITION AND
V
ELOCITY
E
RRORS
E
RROR
-H
ANDLING
M
ETHODS
In position mode, the difference between the limited position output of the trajectory
generator and the actual motor position is the position or f
ollowing error. The drive’s position
loop uses complementary methods for handling position errors: following error fault, following
error warning, and a position-tracking window.
Likewise, in velocity or position mode, any difference between the limited velocity command
and actual velocity is a velocity error. The drive’s velocity loop uses a velocity tracking window
method to handle velocity errors. (There is no velocity error fault.)
F
OLLOWING
E
RROR
F
AULTS
When the position error reaches the programmed fault threshold, the drive immediately
faults. (The following error fault can be disabled.) For detailed information,
see
F
OLLOWING
E
RROR
W
ARNINGS
When the position error reaches the programmed warning threshold, the drive immediately
sets the following error warning bit in the status word. This bit can be read over a CAN or
EtherCAT. It can also be used to activate a digital output.
P
OSITION AND
V
ELOCITY
T
RACKING
W
INDOWS
When the position error exceeds the programmed tracking window value, a status word bit is
set. The bit is not reset until the position error remains within the tracking window for the
programmed tracking time. A similar method is used to handle velocity errors.
For detailed information, see
F
OLLOWING
E
RROR
F
AULT
D
ETAILS
P
OSITION
E
RROR
R
EACHES
F
AULT
L
EVEL
As described earlier, position error is the difference between the limited position output of the
trajectory generator and the actual position. When position error reaches the programmed
Following Error Fault level, the drive faults (unless the following error fault is disabled.) As
with a warning, a status bit is set. In addition, the fault is recorded in the error log. Additional
responses and considerations depend on whether the fault is non-latched or latched, as
described below.
D
RIVE
R
ESPONSE TO
N
ON
-L
ATCHED
F
OLLOWING
E
RROR
F
AULT
When a non-latched following error fault occurs, the drive drops into velocity mode and applies
the Fast Stop Ramp deceleration rate to bring the motor to a halt. The drive PWM output
stage remains enabled, and the drive holds the velocity at zero, using the velocity loop.
R
ESUMING
O
PERATIONS
A
FTER A
N
ON
-L
ATCHED
F
OLLOWING
E
RROR
F
AULT
The clearing of a non-
latched following error depends on the drive’s mode of operation.
Issuing a new trajectory command over the CAN bus or the ASCII interface, will clear the
fault and return the drive to normal operating condition.
If the drive is receiving position commands from the digital or differential inputs, then the
drive must be disabled and then re-
enabled using the drive’s enable input or though software
commands. After re-enabling, the drive will operate normally.