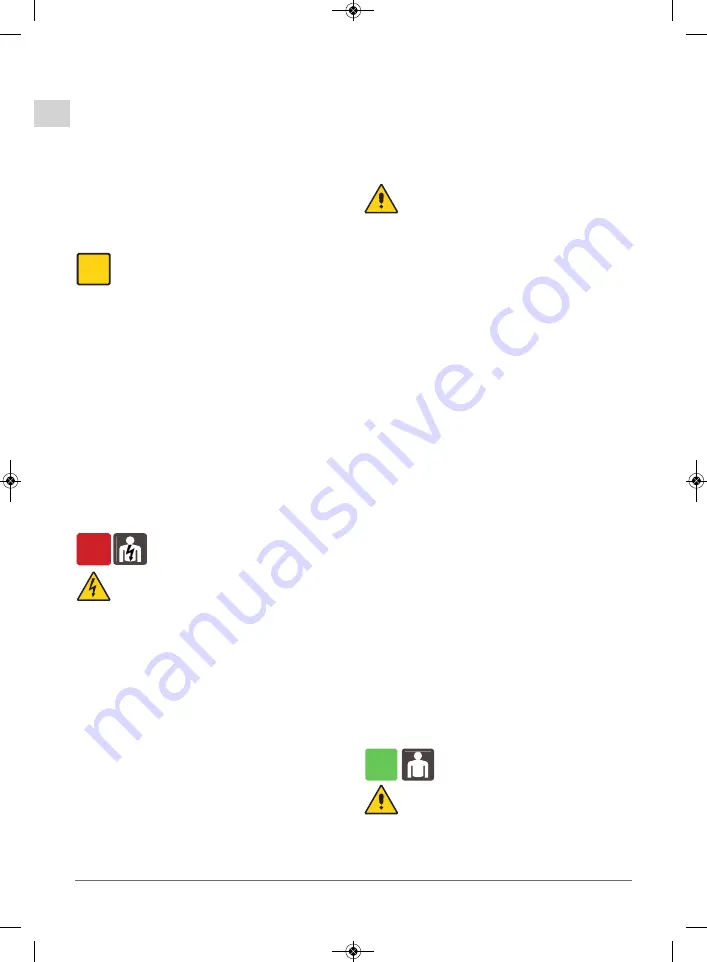
Pagina 8 / 48
CS-R Rev. 2 - Operating Instructions
GB
Deep well.
Make sure the motor remains at least 2-3 metres above the
well bottom.
The well pumping filters must always be below the position
occupied by the motor, in order to guarantee correct cooling.
Check if the dynamic level of the well varies, either because of
seasonal water level lowering or because the pump is too
powerful for the dynamic characteristics of the well.
Tank.
When installed correctly, the unit has a cooling jacket.
If the unit is installed horizontally, the motor must always be
submersed in water when not being used; if it is not, top-up
completely (paragraph 6.2).
6.4 Unpacking
Inspect the device in order to check any damages
which may have occurred during transportation.
Package material, once removed, must be discarded/recy-
cled according to local laws of the destination country.
6.5 Assembly of motor on pump
These instructions refer to the motor only. Please strictly
observe the assembly instructions of the pump manufactu-
rer!
Place motor and pump horizontally and level. Turn motor
shaft by hand before assembly. It must turn freely after over-
coming the adhesive friction. Apply acid-free, waterproof
grease to the coupling internal toothing. Remove nuts from
the studs of the motor. Aling the pump so that its in line with
the lead exit of the motor and guide pump and motor
together. Plase spring rings on the studs and tighten the nuts
crosswise.
Strictly observe the tigthening torques of the unit manufactu-
rer.
Check radial and axial clearance of the motor shaft. There
must be no rigid connection since otherwise motor and
pumps will be damaged during commissioning.
Protect coupling spot against contact.
6.6 Electrical connection
Electrical connection must be carried out only by a
qualified electrician in accordance with local
regulations.
Follow all safety standards.
The unit must be properly earthed (grounded), also with
a nonmetallic delivery pipe.
Make sure the frequency and mains voltage correspond with
the name plate data.
- general disconnecting switch with minimum contact opening
of 3 mm and suitable block when open;
- a suitable heat device to protect the motor set at a maxi-
mum consumption current of not more than 5% of the nomi-
nal current given on the motor plate and with an intervention
time of less than 30 seconds;
- a suitable magnetic device for protecting the cables against
short-circuits;
- a suitable protective device that sections the power in the
case of motor pump faults towards earth;
Install electrodes to protect the pump against dry running.
6.6.1. Connection of cables
Feed cables have to be chosen on the basis of power, distan-
ce, voltage drop and temperature.
For connection of cables in the well, use thermo-shrinking
insulation sheathes or other systems used for submerged
cables.
Before lowering the motor into the well, use appropriate instru-
ments to measure continuity between phases and perform an
isolation test between each single phase and the earth con-
ductor.
The isolation test should be repeated with motor and cable
jonction fully submerged.
6.7. Operation with frequency converter
During starting and/or use, the minimum frequency must not
be lower than 30 Hz, keeping the voltage/frequency ratio con-
stant.
A filter must be inserted between the inverter and the
motor that guarantees the following voltage gradients:
In motors with water and glycol and standard wrap-
ping (PVC/HT):
dV/dt≤500 V/μs e Vpp
(1)
≤1400V
In motors with water and glycol and special wrapping
(PE2+PA):
dV/dt≤650 V/μs e Vpp
(1)
≤1800V
(1)
Voltage between one peak and the next generated by the drive.
Conditions to be respected no matter how long the power
cables are.
6.8 Operation with soft-starter
The SOFT-STARTER device must have a voltage ramp, not
a current ramp.
Always make sure that the soft-starter is excluded when the
unit starting phase has ended.
6.9 Setting the PT100 probes
If there are PT100 probes inside the motor, do the following
to set the intervention temperature threshold:
- Start the motor pump and position yourself at the working
point where the highest absorbed power is; the internal tem-
perature will increase progressively and will be monitored by
the probe. When running correctly (up to 2 hours can pass
according to the motor) the temperature that is read will sta-
bilize.
- When the temperature is stable, set the first alarm at a
value equal to the temperature read +3°C; the alarm must
register that the temperature has been exceeded for regi-
stration of the first inspection.
- The second alarm, which controls motor stopping, has to be
set at a value equal to the temperature read +6° C; restar-
ting (with recording of the temperature that has been excee-
ded) can be automatic but must occur with a delay of at
least 15 minutes from stopping, or at an internal motor tem-
perature that is 20° C lower than the set alarm temperature;
The 2nd alarm, with motor shutdown, cuts in in cases of:
- Overload
- Poor cooling
- Frequent starts
With the motor wrapped in PVC the maximum set temperatu-
re of the second alarm can be 58°C
With the motor wrapped in PE2+PA the maximum set tempe-
rature of the second alarm can be 75°C.
7 SWITCH OFF OF THE PUMP
The appliance must be switch off every time there are
faults. (see troubleshooting).
The product is designed for a continuous duty, the switch off
is performed by disconnecting the power supply by means
the expected disconnecting devices. (see paragraph "6.6
Electrical connection").
OFF
i
ON
IST CSR 09_16 Rev2_MXS 11_03con gall 07/11/16 08:37 Pagina 8