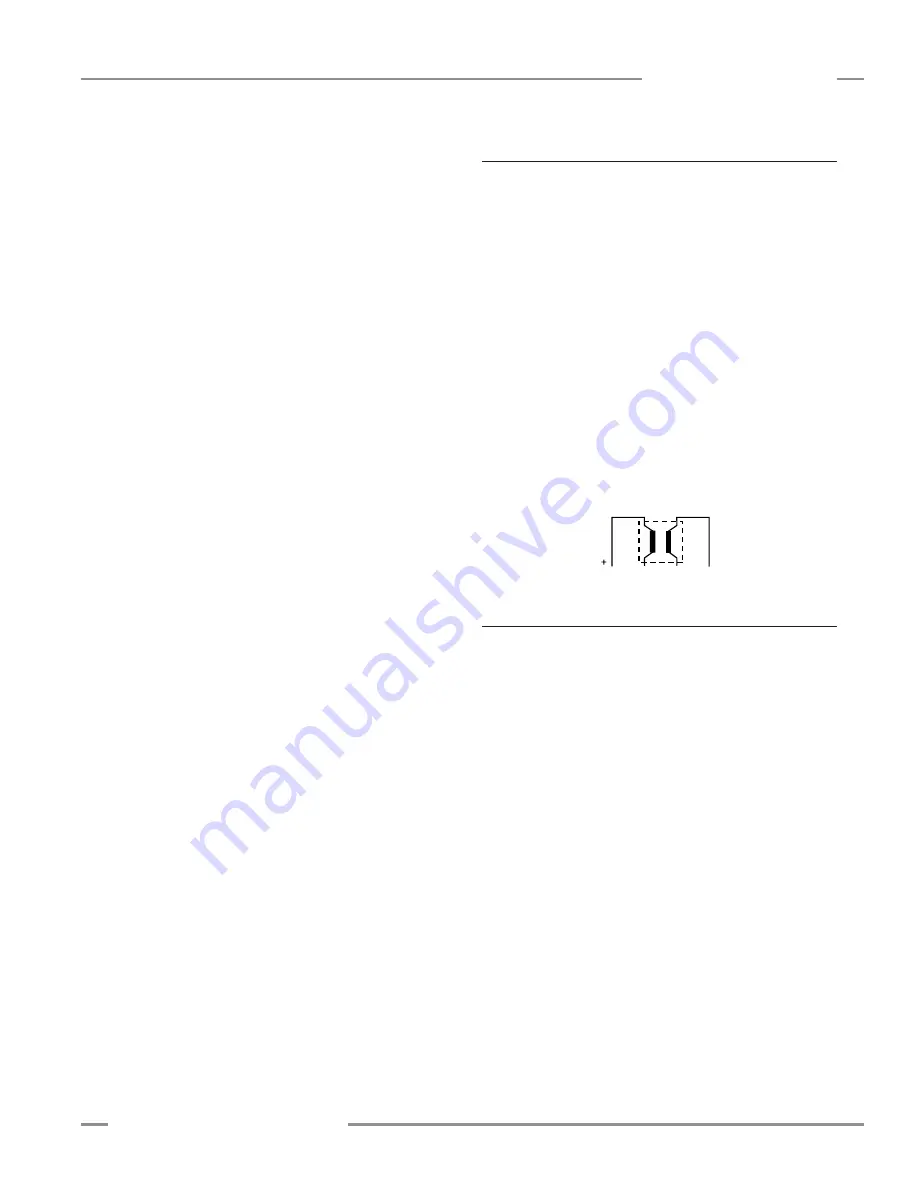
P/N 133487
85
Banner Engineering Corp.
•
Minneapolis, U .S .A .
www .bannerengineering .com • Tel: 763 .544 .3164
SC22-3 Safety Controller
Instruction Manual
Appendix A
Safety Mat System Design and Construction
The safety mat system sensor, Safety Controller, and any
additional devices must have a response time that is fast enough
to reduce the possibility of an individual stepping lightly and
quickly over the mat’s sensing surface (less than 100 to 200 ms,
depending on the relevant standard) .
For a safety mat system, the minimum object sensitivity of the
sensor must detect, at minimum, a 30 kg (66 lb .) weight on an
80 mm (3 .125") diameter circular disk test piece, anywhere on
the mat’s sensing surface, including joints and junctions . The
effective sensing surface or area must be identifiable and can
comprise one or more sensors . The safety mat supplier should
state this minimum weight and diameter as the minimum object
sensitivity of the sensor .
User adjustments to actuating force and response time are not
allowed (ISO 13856-1) . The sensor should be manufactured to
prevent any reasonably foreseeable failures (e .g ., oxidation of
the contact elements) which could cause a loss in sensitivity .
The environmental rating of the sensor must meet a minimum
of IP54 . When the sensor is specified for immersion in water,
the sensor’s minimum enclosure level must be IP67 . The
interconnect cabling may require special attention . A wicking
action may result in the ingress of liquid into the mat, possibly
causing loss of sensor sensitivity . The termination of the
interconnect cabling may need to be located in an enclosure that
has an appropriate environmental rating .
The sensor must not be adversely affected by the environmental
conditions for which the system is intended . The effects on the
sensor of liquids and other substances which can be expected
must be taken into account . For example, long-term exposure to
some liquids can cause degradation or swelling of the sensor’s
housing material, resulting in an unsafe condition .
The sensor’s top surface should be a lifetime non-slip design, or
otherwise minimize the possibility of slipping under the expected
operating conditions .
The four-wire connection between the interconnect cables and
the sensor must withstand dragging or carrying the sensor
by its cable without failing in an unsafe manner (e .g ., broken
connections due to sharp pulls, steady pulls, or continuous
flexing) . If not, an alternate means must be employed to avoid
such a failure, for example, a cable which disconnects without
damage and results in a safe situation .
A.6.2 SC22-3 Safety Mat Hookup Options
Pressure-sensitive mats and pressure-sensitive floors must meet
the requirements of the category for which they are specified and
marked . These categories are defined in ISO 13849-1
(EN 954-1) .
The safety mat, its Safety Controller and any output signal
switching devices must meet the requirements of safety
Category 1 as a minimum . To meet these requirements, the
system must at minimum meet the requirements of ISO 13856-1
(EN 1760-1) and the relevant requirements of ISO 13849-1
(EN 954-1) .
The Safety Controller is designed to monitor 4-wire safety mats;
the SC22-3 is not compatible with two-wire devices (mats,
sensing edges, etc ., with two wires and a “sensing” resistor) .
This circuit typically can meet ISO 13849-1 category 2 or
category 3 requirements depending on the safety rating and
installation of the mat(s) or other sensor(s) . This circuit can
detect a short circuit between channels or to another source of
power .
Safety Mat Input
4-Wire Safety Mat, 4 Terminals
12Oct2006 rev E - Moved Gray box behind the black lines
21-Nov-2006 rev F - Added + sign
10-Jan-07 Rev G - sign text to outlines, changed gray box to black dashed lines
A.6.3 Safety Mat Installation
The mounting surface quality and preparation for the
sensor must meet the requirements stated by the sensor’s
manufacturer . Irregularities in the floor (or other mounting
surfaces) may impair the function of the sensor and therefore
should be reduced to an acceptable minimum .
The mounting surface should be level and clean . The collection
of fluids under or around the sensor should be avoided . The
risk of failure due to build-up of dirt, turning-chips, or other
material under the sensor(s) or the associated hardware must
be prevented . Special consideration should be given to joints
between sensors to ensure that foreign material does not
migrate under or into the sensor .
Any damage (e .g ., cuts, tears, wear, or punctures) to the outer
insulating jacket of the interconnect cable (in the presence
of fluids) or to any part of the exterior of the sensor must be
immediately repaired or replaced . Ingress of material (including
dirt particles, insects, fluid, moisture, or turning-chips) which may
be present near the mat can cause the sensor to corrode or to
lose its sensitivity .