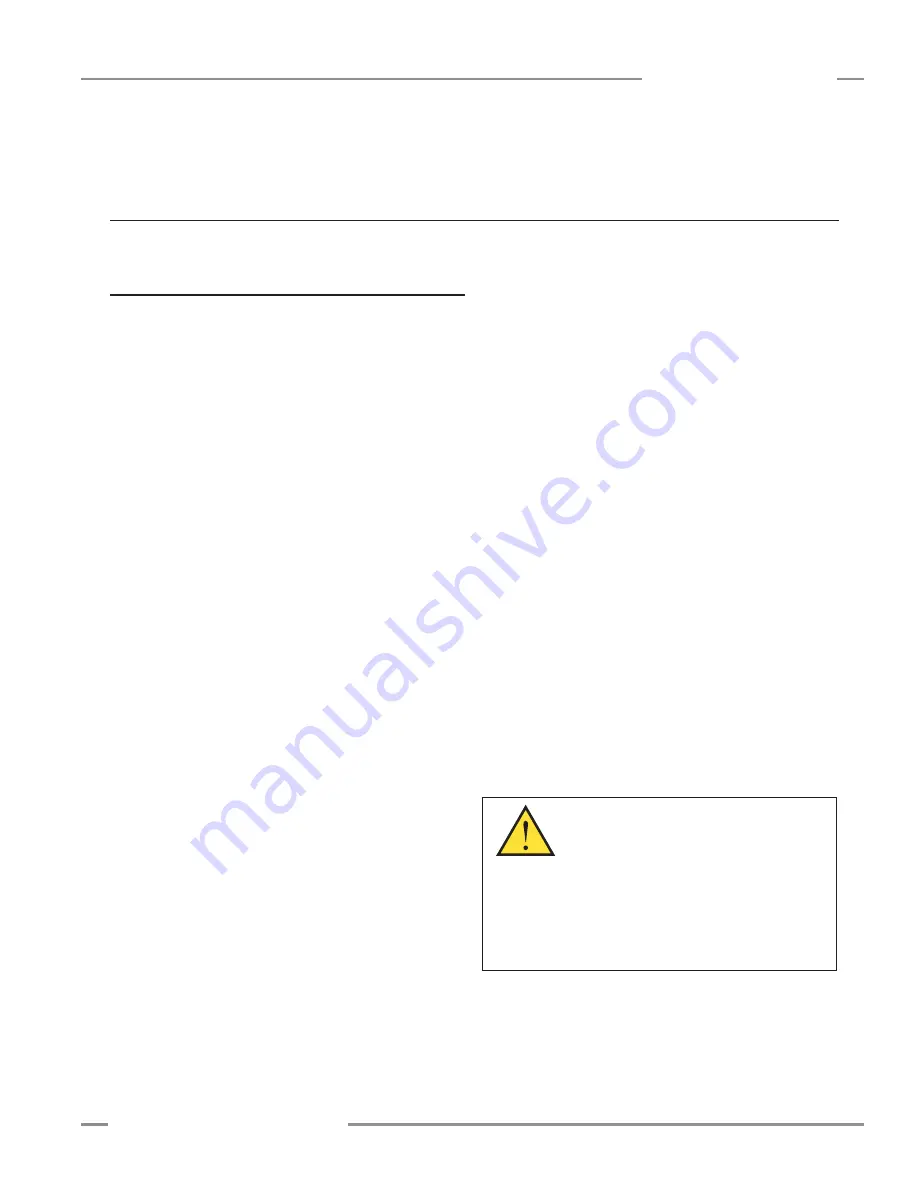
P/N 133487
73
Banner Engineering Corp.
•
Minneapolis, U .S .A .
www .bannerengineering .com • Tel: 763 .544 .3164
SC22-3 Safety Controller
Instruction Manual
Appendix A
A.1 Safety Circuit Integrity and ISO 13849-1 (EN954-1)
Safety Circuit Principles
Safety circuits involve the safety-related functions of a machine
that minimize the level of risk of harm . These safety-related
functions can prevent initiation, or they can stop or remove a
hazard . The failure of a safety-related function or its associated
safety circuit usually results in an increased risk of harm .
The integrity of a safety circuit depends on several factors,
including fault tolerance, risk reduction, reliable and well-tried
components, well-tried safety principles, and other design
considerations .
Depending on the level of risk associated with the machine or
its operation, an appropriate level of safety circuit performance
(i .e ., integrity) must be incorporated into its design . Standards
that detail safety performance levels include ANSI/RIA
R15 .06 Industrial Robots, ANSI B11 Machine Tools, OSHA
29CFR1910 .217 Mechanical Power Presses, and ISO 13849-1
(EN954-1) Safety-Related Parts of a Control System .
Safety Circuit Integrity Levels
Safety circuits in International and European standards have
been segmented into categories, depending on their ability
to maintain their integrity in the event of a failure . The most
recognized standard that details safety circuit integrity levels
is ISO 13849-1 (EN954-1), which establishes five levels:
Categories B, 1, 2, 3, and the most stringent, Category 4 .
In the United States, the typical level of safety circuit integrity
has been called “control reliability .” Control reliability typically
incorporates redundant control and self-checking circuitry and
has been loosely equated to ISO 13849-1 Categories 3 and 4
(see CSA Z432 and ANSI B11 .TR4) .
Appendix A. Input Device and Safety Category Reference
If the requirements described by ISO 13849-1 are to be
implemented, a risk assessment must first be performed to
determine the appropriate category, in order to ensure that
the expected risk reduction is achieved . This risk assessment
must also take into account national regulations, such as U .S .
control reliability or European “C” level standards, to ensure that
the minimum level of performance that has been mandated is
complied with .
The following sections (A .2 through A .11) deal only with
Category 2, Category 3, and Category 4 applications, as
described by ISO 13849-1 (1999) . Figure A-1 provides a
snapshot of the possible safety categories that can be achieved
for each device type, depending on the selected circuit option .
Refer to the text sections following, as well as the appropriate
standards, for further information .
Fault Exclusion
An important concept within the category requirements of
ISO 13849-1 is the “probability of the occurrence of the failure,”
which can be decreased using a technique termed “fault
exclusion .” The rationale assumes that the possibility of certain
well-defined failure(s) can be reduced to a point where the
resulting fault(s) can be, for the most part, disregarded—that is,
“excluded .”
Fault exclusion is a tool a designer can use during the
development of the safety-related part of the control system
and the risk assessment process . Fault exclusion allows the
designer to design out the possibility of various failures and
justify it through the risk assessment process to meet the intent
requirements of Category 2, 3 or 4 . See ISO 13849-1/-2 for
further information .
WARNING . . .
Safety Categories
The level of safety circuit integrity can be greatly
impacted by the design and installation of the safety
devices and the means of interfacing of those devices . A risk
assessment must be performed to determine the appropriate
safety circuit integrity level or safety category as described
by ISO 13849-1 (EN 954-1) to ensure that the expected risk
reduction is achieved and that all relevant regulations are
complied with.