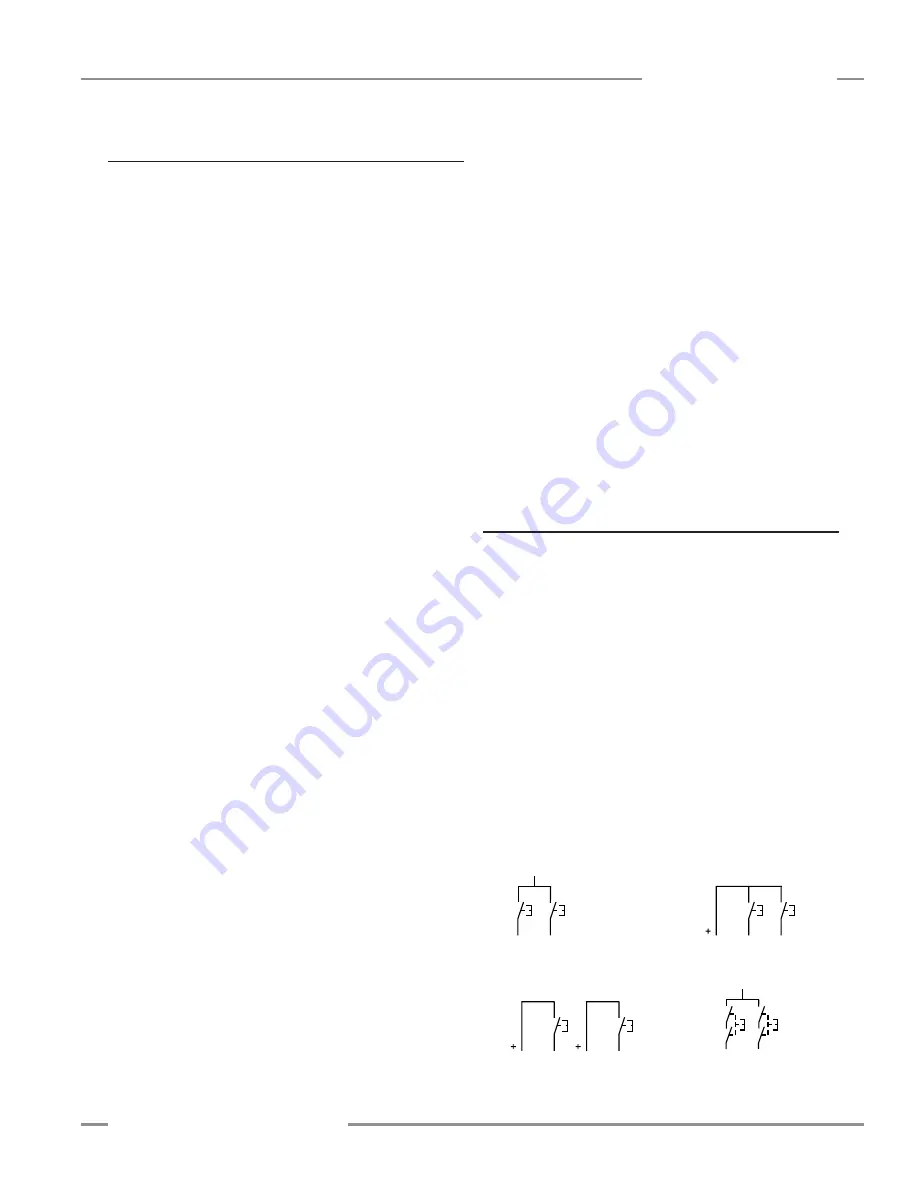
P/N 133487
83
Banner Engineering Corp.
•
Minneapolis, U .S .A .
www .bannerengineering .com • Tel: 763 .544 .3164
SC22-3 Safety Controller
Instruction Manual
Appendix A
NOTES:
1 . The OSHA-recommended hand speed constant K has been
determined by various studies, and although these studies
indicate speeds of 63"/sec to over 100"/sec, they are not
conclusive determinations . The employer should consider all
factors, including the physical ability of the operator, when
determining the value of K to be used .
2 . Ts is usually measured by a stop-time measuring device . If
the specified machine stop time is used, add at least 20% as
a safety factor to account for brake system deterioration . If
the stop-time of the two redundant machine control elements
is unequal, the slower of the two times must be used for
calculating the separation distance .
3 . Th is usually insignificant for purely mechanical switches .
However, Th should be considered for separation distance
calculation when using electronic or electromechanical (i .e .
powered) hand controls . For Banner Self-checking Touch
Buttons (STBs) response time = 0 .02 seconds .
A.5.2 SC22-3 Two-Hand Control Hookup Options
The device is shown not actuated or in the Off state . See
ISO 13851 for a complete explanation of “Type” designations
and ISO 13849-1 Category requirements .
Dual-Channel (2 terminals, 3 terminals, or 4 terminals):
The figures below are a Type IIIa Two-Hand Control circuit as
described by ISO 13851, and typically can meet ISO 13849-1
(EN 954-1) Category 1 requirements . A Type IIIb and Category 3
can be achieved if redundant contacts from each hand control
are used in each channel, i .e ., two each in series, as shown
in Figure D below, or with a 3-terminal hookup that uses pulse
monitoring and can detect a short circuit to another source
of power . Both 2- and 3-terminal hookups can detect a short
between channels when the contacts are open if the short is
present longer than 2 seconds . The 4-terminal circuit can detect
a short circuit between channels or to another source of power
(Figure C) .
A.
Two-Hand Operation
2-Ch, 2 Terminals
2-Ch, 3 Terminals
2-Ch, 4 Terminals
2-Ch, 2 Terminals
2 PNP
Two Hand Operation - 2x Dual Channel Complementary
2x Complementary,
4 Terminals
2x Complementary,
5 Terminals
2x Complementary,
4 Terminals, 4 PNP
Revision History
Rev C - Corrected “OFF” and “ON” on Two-hand Operation - 2x Dual Channel Complementary, 2x Complementary, 4 Terminals, 4 PNP
20-Sept-06 Rev. D - Moved 24V, ON and OFF text closer to drawings.
13-Oct-06 Rev. E Gray lines moved below the black lines
21-Nov-06 Rev. F - Added + sign to 2-Ch, 3 Terminals, 2-Ch, 4 Terminals, 2x Dual Channel Complementary, 5 Terminals
10-Jan-07 Rev. G - C sign text to outlines, changed gray lines to 6 pt. dashed lines
25-May-07 Rev H - Changed 2-Ch, 2 Terminals 2 PNP; 2x Complementary, 5 Terminals (centered arrow) and 2x Complementary, 4 Terminals, 4 PNP
24V
24V
OFF
OFF
ON
OFF
ON
OFF
B.
Two-Hand Operation
2-Ch, 2 Terminals
2-Ch, 3 Terminals
2-Ch, 4 Terminals
2-Ch, 2 Terminals
2 PNP
Two Hand Operation - 2x Dual Channel Complementary
2x Complementary,
4 Terminals
2x Complementary,
5 Terminals
2x Complementary,
4 Terminals, 4 PNP
Revision History
Rev C - Corrected “OFF” and “ON” on Two-hand Operation - 2x Dual Channel Complementary, 2x Complementary, 4 Terminals, 4 PNP
20-Sept-06 Rev. D - Moved 24V, ON and OFF text closer to drawings.
13-Oct-06 Rev. E Gray lines moved below the black lines
21-Nov-06 Rev. F - Added + sign to 2-Ch, 3 Terminals, 2-Ch, 4 Terminals, 2x Dual Channel Complementary, 5 Terminals
10-Jan-07 Rev. G - C sign text to outlines, changed gray lines to 6 pt. dashed lines
25-May-07 Rev H - Changed 2-Ch, 2 Terminals 2 PNP; 2x Complementary, 5 Terminals (centered arrow) and 2x Complementary, 4 Terminals, 4 PNP
24V
24V
OFF
OFF
ON
OFF
ON
OFF
C.
Two-Hand Operation
2-Ch, 2 Terminals
2-Ch, 3 Terminals
2-Ch, 4 Terminals
2-Ch, 2 Terminals
2 PNP
Two Hand Operation - 2x Dual Channel Complementary
2x Complementary,
4 Terminals
2x Complementary,
5 Terminals
2x Complementary,
4 Terminals, 4 PNP
Revision History
Rev C - Corrected “OFF” and “ON” on Two-hand Operation - 2x Dual Channel Complementary, 2x Complementary, 4 Terminals, 4 PNP
20-Sept-06 Rev. D - Moved 24V, ON and OFF text closer to drawings.
13-Oct-06 Rev. E Gray lines moved below the black lines
21-Nov-06 Rev. F - Added + sign to 2-Ch, 3 Terminals, 2-Ch, 4 Terminals, 2x Dual Channel Complementary, 5 Terminals
10-Jan-07 Rev. G - C sign text to outlines, changed gray lines to 6 pt. dashed lines
25-May-07 Rev H - Changed 2-Ch, 2 Terminals 2 PNP; 2x Complementary, 5 Terminals (centered arrow) and 2x Complementary, 4 Terminals, 4 PNP
24V
24V
OFF
OFF
ON
OFF
ON
OFF
D.
Two-Hand Operation
2-Ch, 2 Terminals
2-Ch, 2 Terminals
2-Ch, 3 Terminals
2-Ch, 4 Terminals
2-Ch, 2 Terminals
2 PNP
Two Hand Operation - 2x Dual Channel Complementary
2x Complementary,
4 Terminals
2x Complementary,
5 Terminals
2x Complementary,
4 Terminals, 4 PNP
Revision History
Rev C - Corrected “OFF” and “ON” on Two-hand Operation - 2x Dual Channel Complementary, 2x Complementary, 4 Terminals, 4 PNP
20-Sept-06 Rev. D - Moved 24V, ON and OFF text closer to drawings.
13-Oct-06 Rev. E Gray lines moved below the black lines
21-Nov-06 Rev. F - Added + sign to 2-Ch, 3 Terminals, 2-Ch, 4 Terminals, 2x Dual Channel Complementary, 5 Terminals
10-Jan-07 Rev. G - C sign text to outlines, changed gray lines to 6 pt. dashed lines
25-May-07 Rev H - Changed 2-Ch, 2 Terminals 2 PNP; 2x Complementary, 5 Terminals (centered arrow) and 2x Complementary, 4 Terminals, 4 PNP
20-Sept-07 Rev I - Added another 2-ch, 2 Terminal for the manual
24V
24V
OFF
OFF
ON
OFF
ON
OFF
24V
A.5.1 Two-Hand Control Separation Distance
Both hand controls must be located far enough away from the
nearest hazard point that the operator cannot reach the hazard
with a hand or other body part before the hazardous motion
ceases . This is the “separation distance,” and may be calculated
as follows:
For Part-Revolution Clutch Machinery Where the machine
and its controls allow the machine to stop motion during the
hazardous portion of the machine cycle, use the following
formula:
Ds = K x (Ts + Tr + Th)
For Full-Revolution Clutch Machinery Where the machine and
its controls are designed to complete a full machine cycle, once
activated, use the following formula:
Ds = K x (Tm + Tr + Th)
For both formulas,
Ds = the separation distance in inches,
K = 63" per second (the hand speed constant currently
accepted by OSHA; see NOTE 1)
Ts = the stop time (in seconds) of the machine, measured
from the application of the “stop” signal to the final
ceasing of all motion, including stop times of all relevant
control elements, and measured at maximum machine
velocity (see NOTE 2)
Tr = the response time of the Safety Controller as measured
from the time a stop is signalled by either hand control .
(Controller default response is 0 .010 seconds, plus any
additional closed-to-open debounce time . If the debounce
time is adjusted, the time in excess of 6 ms (=default
closed-to-open debounce time) must be added to the
stated response; refer to Specifications, Section 2 .2 .)
Th = the response time of the slowest hand control (from the
time when a hand disengages that control until the switch
opens; see NOTE 3)
Tm = the maximum time (in seconds) the machine takes
to cease all motion after it has been tripped . For full-
revolution clutch presses with only one engaging point,
Tm is equal to the time necessary for one and one-half
revolutions of the crankshaft . For full-revolution clutch
presses with more than one engaging point, Tm is
calculated as follows:
Tm = (1/2 + 1/N) x Tcy
where:
N = number of clutch engaging points per revolution
Tcy = time (in seconds) necessary to complete one
revolution of the crankshaft