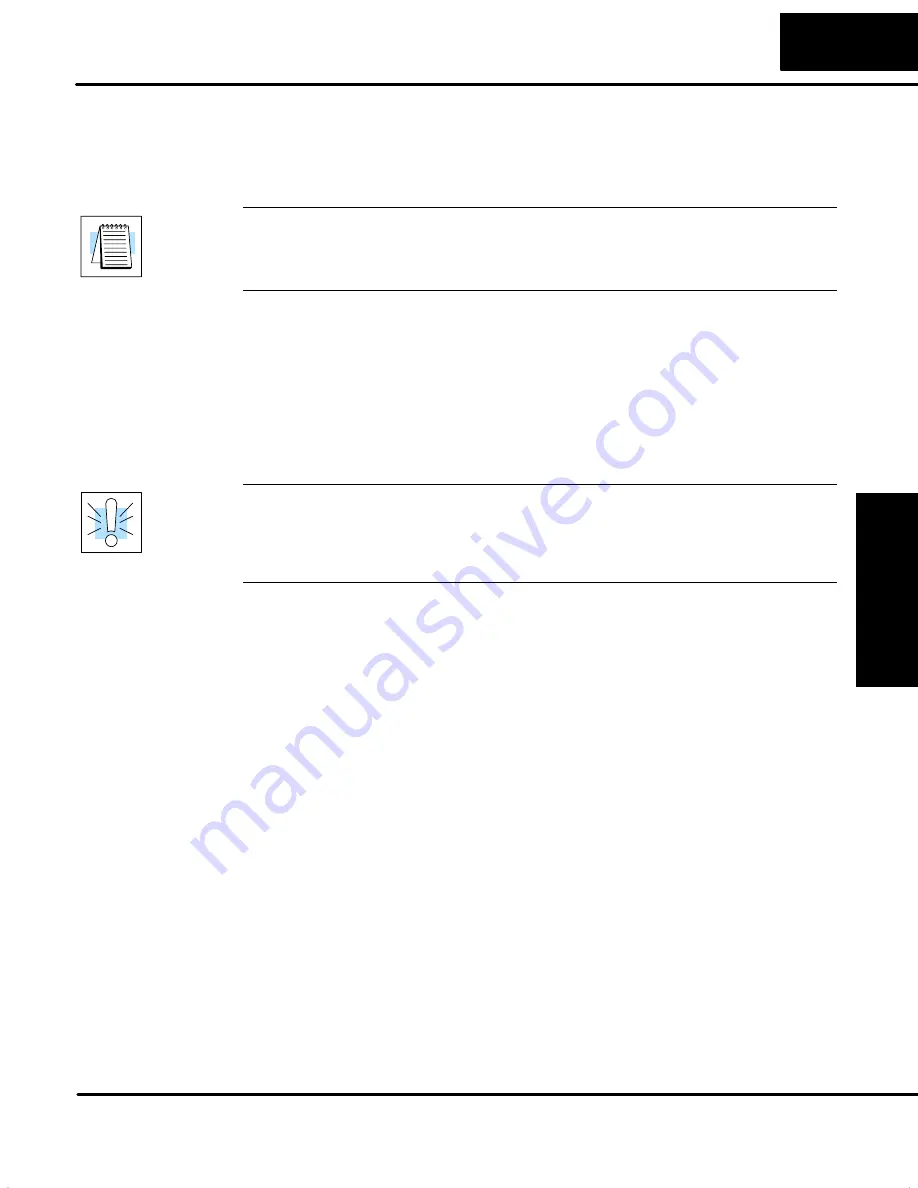
PID Loop Operation
Maintenance
8–39
PID Loop Operation
Now comes the exciting moment when we actually close the loop (go to Auto Mode)
for the first time. Use the following checklist
before
switching to Auto mode:
S
Monitor the loop parameters with a loop trending instrument. We
recommend using the PID view feature of
Direct
SOFT.
NOTE:
We recommend using the PID trend view setup menu to select the vertical
scale feature to
manual,
for both SP/PV area and Bias/Control Output areas. The
auto scaling feature will otherwise change the vertical scale on the process
parameters and add confusion to the loop tuning process.
S
Adjust the gains so the Proportional Gain = 10, Integrator Gain = 9999,
and Derivative Gain =0000. This disables the integrator and derivative
terms, and provides a little proportional gain.
S
Check the bias term value in the loop parameter table (V+04). If it is not
zero, then write it to zero using
Direct
SOFT32 or HPP, etc.
Now we can transition the loop to Auto Mode.
Check the mode monitoring bits to
verify its true mode. If the loop will not stay in Auto Mode, check the troubleshooting
tips at the end of this chapter.
CAUTION:
If the PV and Control Output values begin to oscillate, reduce the gain
values immediately. If the loop does not stabilize immediately, then transfer the loop
back to Manual Mode and manually write a safe value to the control output.
During
the loop tuning procedure, always be near the Emergency Stop switch which
controls power to the loop actuator in case a shutdown is necessary.
S
At this point, the SP should = PV because of the bumpless transfer
feature. Increase the SP a little, in order to develop an error value. With
only the proportional gain active and the bias term=0, we can easily
check the control output value:
Control Output = (SP – PV) x proportional gain
S
If the control output value changed, the loop should be getting more
energy from the actuator, heater, or other device. Soon the PV should
move in the direction of the SP. If the PV does not change, then
increase the proportional gain until it moves slightly.
S
Now, add a small amount of integral gain.
Remember that large
numbers are small integrator gains and small numbers are large
integrator gains!
After this step, the PV should = SP, or be very close.
Until this point we have only used proportional and integrator gains. Now we can
“bump the process” (change the SP by 10%), and adjust the gains so the PV has an
optimal response. Refer to the figure below. Adjust the gains according to what you
see on the PID trend view. The critically- damped response shown gives the fastest
PV response without oscillating.
Manual Tuning
Procedure
Содержание DL05
Страница 1: ...DL05 User Manual Automationdirect com ...
Страница 2: ...DL05 User Manual Automationdirect com ...
Страница 436: ...1B DL05 Error Codes In This Appendix Ċ Error Code Table ...
Страница 443: ...1C Instruction Execution Times In This Appendix Ċ Introduction Ċ Instruction Execution Times ...
Страница 459: ...1D Special Relays In This Appendix Ċ DL05 PLC Special Relays ...
Страница 464: ...1E DL05 Product Weights In This Appendix Ċ Product Weight Table ...
Страница 466: ...1F European Union Directives CE In This Appendix Ċ European Union EU Directives Ċ Basic EMC Installation Guidelines ...