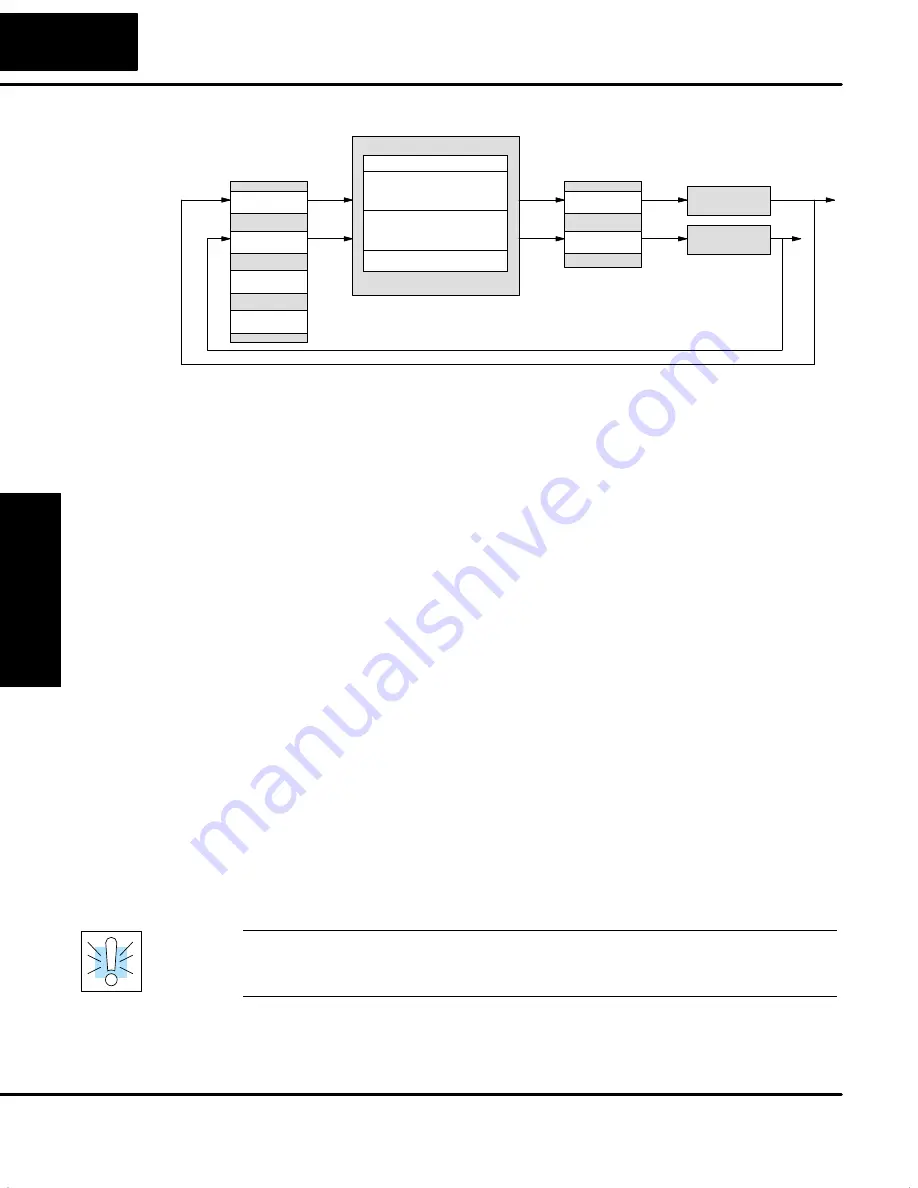
PID Loop Operation
Maintenance
and T
roubleshooting
8–18
PID Loop Operation
Loop 1 Data
SP
V-memory
Digital
Output
DL05 CPU
Input
Module
Channel 1
Process 1
Process 2
PV
OUT
Channel 2
Loop 2 Data
SP
PV
OUT
Channel 3
Channel 4
Channel 1
Channel 2
After selection and procurement of all loop components and I/O module(s), you can
perform the wiring and installation. Refer to the wiring guidelines in Chapter 2 of this
Manual, and to the
D0–OPTIONS–M
manual. The most common wiring errors when
installing PID loop controls are:
S
Reversing the polarity of sensor or actuator wiring connections.
S
Incorrect signal ground connections between loop components.
After wiring and installation, choose the loop setup parameters. The easiest method
for programming the loop tables is using
Direct
SOFT32 (3.0c or later). This software
provides PID Setup dialog boxes which simplify the task.
Note:
It is important to
understand the meaning of all loop parameters mentioned in this chapter before
choosing values to enter.
With the sensor and actuator wiring done, and loop parameters entered, we must
manually and carefully check out the new control system (use Manual Mode).
S
Verify that the PV value from the sensor is correct.
S
If it is safe to do so, gradually increase the control output up above 0%,
and see if the PV responds (
and moves in the correct direction!
).
If the Open Loop Test (see Loop Tuning on page 8–38) shows the PV reading is
correct and the control output has the proper effect on the process, you can follow
the closed loop tuning procedure (see Automatic Mode on page 8–39). In this step,
you tune the loop so the PV automatically follows the SP.
If the closed loop test shows the PV will follow small changes in the SP, consider
running an actual process cycle. You will need to have completed the programming
which will generate the desired SP in real time. In this step, you may want to run a
small test batch of product through the machine, watching the SP change according
to the recipe.
WARNING:
Be sure the Emergency Stop and power-down provision is readily
accessible, in case the process goes out of control. Damage to equipment and/or
serious injury to personnel can result from loss of control of some processes.
When the loop tests and tuning sessions are complete, be sure to save all loop setup
parameters to disk.
Step 5:
Wiring and
Installation
Step 6:
Loop Parameters
Step 7:
Check Open Loop
Performance
Step 8:
Loop Tuning
Step 9:
Run Process Cycle
Step 10:
Save Parameters
Содержание DL05
Страница 1: ...DL05 User Manual Automationdirect com ...
Страница 2: ...DL05 User Manual Automationdirect com ...
Страница 436: ...1B DL05 Error Codes In This Appendix Ċ Error Code Table ...
Страница 443: ...1C Instruction Execution Times In This Appendix Ċ Introduction Ċ Instruction Execution Times ...
Страница 459: ...1D Special Relays In This Appendix Ċ DL05 PLC Special Relays ...
Страница 464: ...1E DL05 Product Weights In This Appendix Ċ Product Weight Table ...
Страница 466: ...1F European Union Directives CE In This Appendix Ċ European Union EU Directives Ċ Basic EMC Installation Guidelines ...