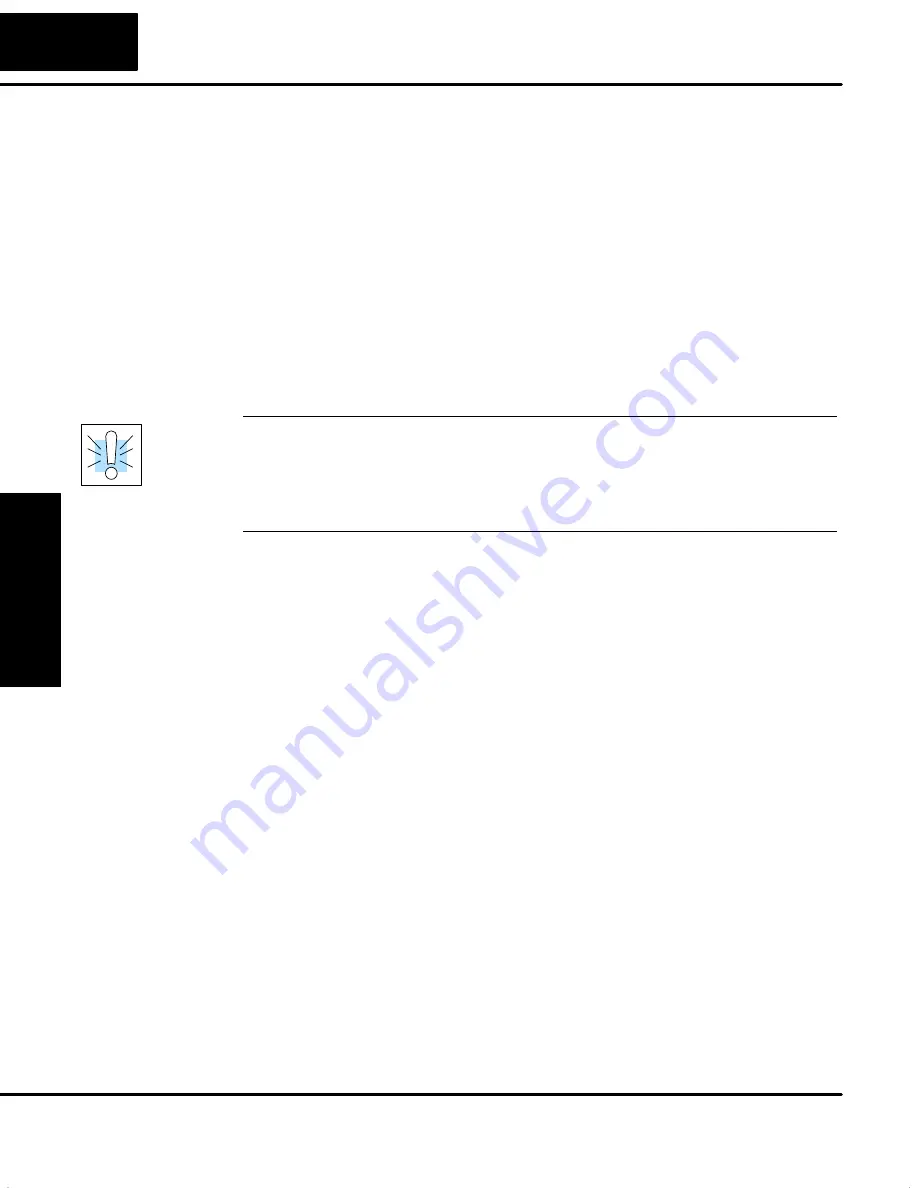
PID Loop Operation
Maintenance
and T
roubleshooting
8–38
PID Loop Operation
Loop Tuning Procedure
This is perhaps the most important step in closed-loop process control. The goal of a
loop tuning procedure is to adjust the loop gains so the loop has optimal
performance in dynamic conditions. The quality of a loop’s performance may
generally be judged by how well the PV follows the SP after a SP step change.
Auto Tuning versus Manual Tuning
– you may change the PID gain values directly
(manual tuning), or you can have the PID processing engine in the CPU
automatically calculate the gains (auto tuning). Most experienced process
engineers will have a favorite method, and the DL05 will accommodate either
preference. The use of the auto tuning can eliminate much of the trial-and-error of
the manual tuning approach, especially if you do not have a lot of loop tuning
experience. However, note that performing the auto tuning procedure will get the
gains
close
to optimal values, but additional manual tuning changes can take the
gain values to their optimal values.
WARNING:
Only authorized personnel fully familiar with all aspects of the process
should make changes that affect the loop tuning constants. Using the loop auto tune
procedures will affect the process, including inducing large changes in the control
output value. Make sure you thoroughly consider the impact of any changes to
minimize the risk of injury to personnel or damage to equipment. The auto tune in the
DL05 is not intended to perform as a replacement for your process knowledge.
Whether you use manual or auto tuning, it is very important to verify basic
characteristics of a newly-installed process before attempting to tune it. With the
loop in Manual Mode, verify the following items for each new loop.
S
Setpoint
– verify the source which is to generate the setpoint can do so.
You can put the PLC in Run Mode, but leave the loop in Manual Mode.
Then monitor the loop table location V+02 to see the SP value(s). The
ramp/soak generator (if you are using it) should be tested now.
S
Process Variable
– verify the PV value is an accurate measurement,
and the PV data arriving in the loop table location V+03 is correct. If the
PV signal is very noisy, consider filtering the input either through
hardware (RC low-pass filter), or using a digital S/W filter.
S
Control Output
– if it is safe to do so, manually change the output a
small amount (perhaps 10%) and observe its affect on the process
variable. Verify the process is direct-acting or reverse acting, and check
the setting for the control output (inverted or non-inverted). Make sure
the control output upper and lower limits are not equal to each other.
S
Sample Rate
– while operating open-loop, this is a good time to find the
ideal sample rate (procedure give earlier in this chapter). However, if
you are going to use auto tuning, note the auto tuning procedure will
automatically calculate the sample rate in addition to the PID gains.
The discussion beginning on the following page covers the manual tuning
procedure. If want to perform only auto tuning, please skip the next section and
proceed directly to the section on auto tuning.
Open-Loop Test
Содержание DL05
Страница 1: ...DL05 User Manual Automationdirect com ...
Страница 2: ...DL05 User Manual Automationdirect com ...
Страница 436: ...1B DL05 Error Codes In This Appendix Ċ Error Code Table ...
Страница 443: ...1C Instruction Execution Times In This Appendix Ċ Introduction Ċ Instruction Execution Times ...
Страница 459: ...1D Special Relays In This Appendix Ċ DL05 PLC Special Relays ...
Страница 464: ...1E DL05 Product Weights In This Appendix Ċ Product Weight Table ...
Страница 466: ...1F European Union Directives CE In This Appendix Ċ European Union EU Directives Ċ Basic EMC Installation Guidelines ...