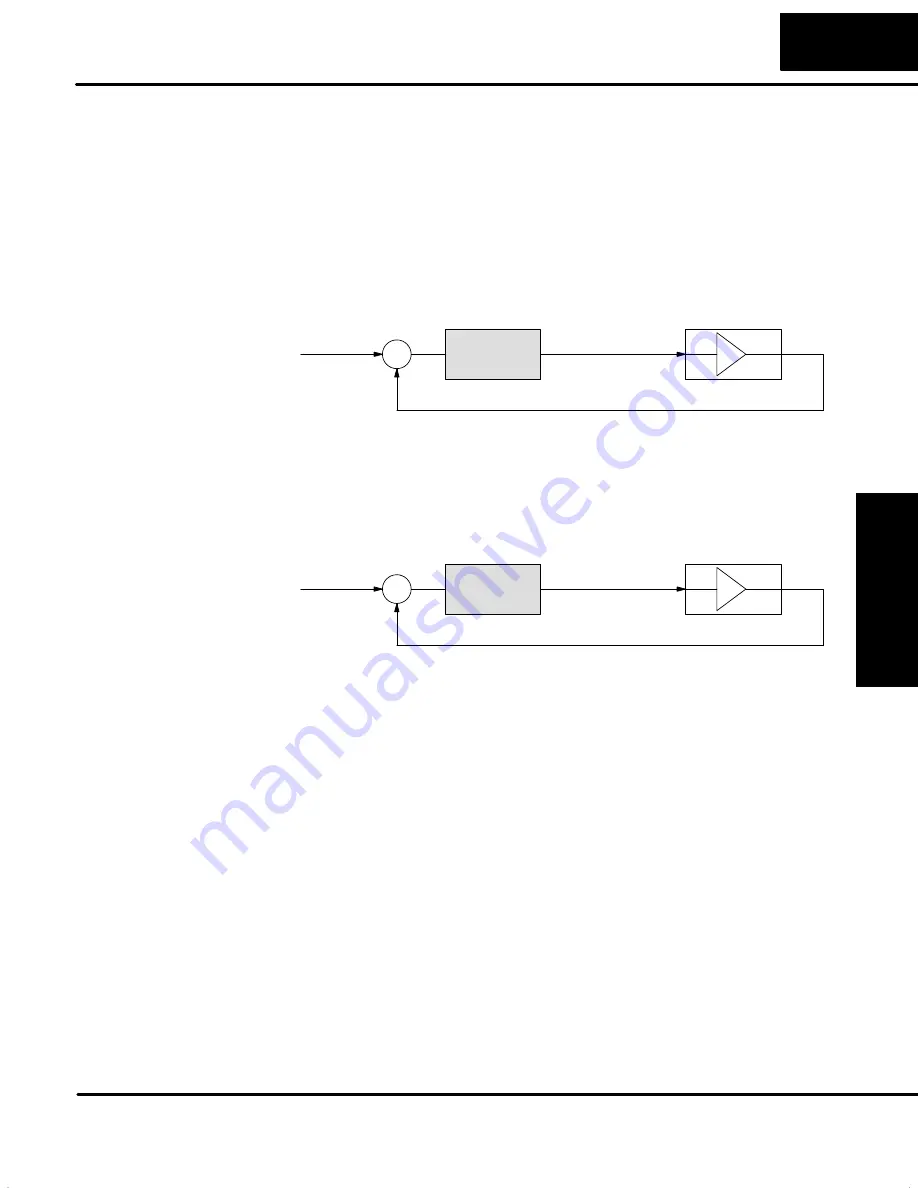
PID Loop Operation
Maintenance
8–33
PID Loop Operation
The gain of a process determines, in part, how it must be controlled. The process
shown in the diagram below has a positive gain, which we call “direct-acting”. This
means that when the control output increases, the process variable also eventually
increases. Of course, a true process is usually a complex transfer function that
includes time delays. Here, we are only interested in the direction of change of the
process variable in response to a control output change.
Most process loops will be direct-acting, such as a temperature loop. An increase in
the heat applied increases the PV (temperature). Accordingly, direct-acting loops
are sometimes called
heating loops
.
Process Variable
Loop
Calculation
S
+
–
Control Output
Setpoint
Process
+
Direct-Acting Loop
A “reverse-acting” loop is one in which the process has a negative gain, as shown
below. An increase in the control output results in a decrease in the PV. This is
commonly found in refrigeration controls, where an increase in the cooling input
causes a decrease in the PV (temperature). Accordingly, reverse-acting loops are
sometimes called
cooling loops
.
Process Variable
Loop
Calculation
S
+
–
Control Output
Setpoint
Process
–
Reverse-Acting Loop
It is crucial to know whether a particular loop is direct or reverse-acting!
Unless you are controlling temperature, there is no obvious answer. In a flow control
loop, a valve positioning circuit can be configured and wired reverse-acting as easily
as direct-acting. One easy way to find out is to run the loop in Manual Mode, where
you must manually generate control output values. Observe whether the PV goes up
or down in response to a step increase in the control output.
To run a loop in Auto or Cascade Mode, the control output must be correctly
programmed (refer to the previous section on Control Output Configuration). Use
“normal output” for direct-acting loops, and “inverted output” for reverse-acting
loops. To compensate for a reverse-acting loop, the PID controller must know to
invert the control output. If you have a choice, configure and wire the loop to be
direct-acting. This will make it easier to view and interpret loop data during the loop
tuning process.
Direct-Acting and
Reverse-Acting
Loops
Содержание DL05
Страница 1: ...DL05 User Manual Automationdirect com ...
Страница 2: ...DL05 User Manual Automationdirect com ...
Страница 436: ...1B DL05 Error Codes In This Appendix Ċ Error Code Table ...
Страница 443: ...1C Instruction Execution Times In This Appendix Ċ Introduction Ċ Instruction Execution Times ...
Страница 459: ...1D Special Relays In This Appendix Ċ DL05 PLC Special Relays ...
Страница 464: ...1E DL05 Product Weights In This Appendix Ċ Product Weight Table ...
Страница 466: ...1F European Union Directives CE In This Appendix Ċ European Union EU Directives Ċ Basic EMC Installation Guidelines ...