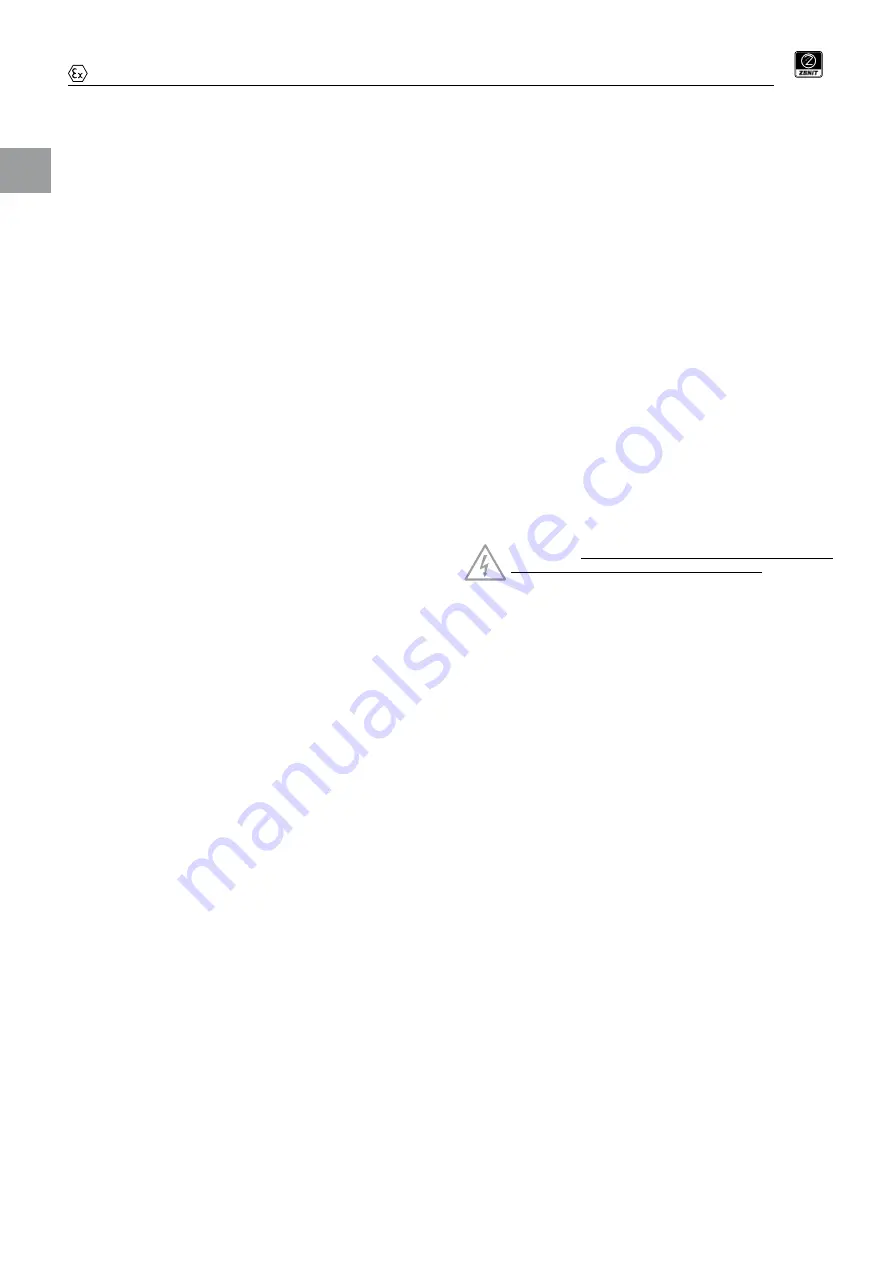
EN
10
better together
User and maintenance manual – Translation of original instructions
rigid or metallic tubing. It is also possible to connect the pump to a
polyethylene pipe using an appropriate fitting.
It is advisable to install a gate valve and a flow ball check valve to allow
free passage. This should be done using a connection pipe with length
L > 5 Di (Di= internal diameter of connection pipe)
(fig. 3 page 126).
4.2 Installation with a coupling device
This type of installation allows easy removal of the pump from the tank
and quick repositioning without requiring interferance on the system.
4.2.1 Installation with external coupling device (fig. 4 page 126)
Models with a vertical delivery can be installed with an external cou
-
pling device composed of a fixed part and a mobile part.
The fixed part is connected to the tubing of the system using a DN50
flange or a 2” GAS thread.
The mobile part is attached to the pump’s delivery pipe using an appro
-
priately sized piece of pipe.
This device allows the easy separation of the pump from the system
and, without any intervention in the bottom of the tank, it can be
mounted even without being emptied.
4.2.2 Installation with a bottom coupling device (fig. 5A - 5B page 126)
This type of installation, which is designed for pumps with horizontal
outlets, allows the pump to be removed from the tank and repositioned
in a quick way without affecting the system.
For models with a vertical outlet with 1½”-2” GAS thread, it is necessa
-
ry to use a special adaptor kit.
Proceed in the following manner:
•
Attach the sliding flange to the delivery pipe on the pump using the
screws provided with the coupling device;
•
Steadily attach the coupling device to the bottom of the tank;
•
It is recommended to install a gate valve and a flow ball check valve
to allow free passage. This should be done using a connection pipe
with length L > 5 Di (Di= internal diametre of connection pipe)
(fig.
6 page 127).
•
Affix the coupling device securely to bottom of the tank;
•
Join the guide tubes to the coupling device and secure them at the
top with the spacer bracket (supplied by the manufacturer) which will
ensure their correct parallel alignment and guarantee the necessary
rigidity of the system;
•
The pump can then be lowered using a rope or chain attached to the
handle on the upper part of the motor cover. The guide tubes should
be used to aid the coupling of the flange with the outlet tube of the
pump until it is affixed to the coupling device.
4.3 Dry or semi-immersed installation (fig. 7 page 127)
Dry or semi-immersed installation is permitted, for pumps without a
cooling jacket, only with intermittent periodic duty (S3 mode) according
to the percentage indicated on the metal plaque.
Pumps with a suction flange can be coupled to the system using a
curved base plate.
4.3.1 Dry installation with a cooling jacket (fig. 8 page 127)
(only models DGN-DRN-MAN-GRN-APN)
A cooling jacket allows continuous duty (S1) of the submergible elec
-
tric pump even with partial immersion or installed in a drying chamber.
This type of application can use the fluid in the tank as a cooling liquid
if it is clean enough and free from solid bodies, or else water from an
external circuit.
In both instances, the pump comes supplied with a predisposed suc
-
tion flange for attachment to a curved base plate.
4.3.1.1 Closed jacket cooling system (CC) (fig. 8A page 127)
Owing to the particular shape of the rear part of the impeller, the liquid
in which the pump is immersed is pumped into the gap between the
body and the jacket, assuring the cooling of the motor. Once the gap
is filled, the liquid is sucked into the pump body through a pipe and is
then expelled.
WARNING: This system can only be used with clean liquids free
from solid or filamentous particles.
4.3.1.2 Open jacket system cooling (CCE) (fig. 8B page 127)
The cooling liquid which is pumped into the gap between the body and
the jacket comes from an external pressure unit.
With the pump, two attachments per “Rilsan” pipe are provided. Con
-
nect the water inlet pipe to where the “ENTRATA - IN”
(fig. 9 page
127)
sign is attached. Connect the drain pipe to where the “USCITA
- OUT”
(fig. 9 page 127)
sign is attached.
The temperature of the cooling liquid must not exceed 40°C going into
the jacket.
The capacity of the system must be 2-3 l/min and the maximum
pressure must not exceed 0.2 bar.
The cooling circuit must be activated at least 10 seconds before the
pump is turned on and not deactivated before the complete shutdown
of the pump.
5. SUCTION PIPE
The suction pipe of the pump can have a grill which prevents foreign
bodies larger than the size of the free passage of the pump from en-
tering.
It is not recommended to remove the suction grill except in cases whe
-
re it is expressly permitted.
Periodically check that the suction pipe or the grill remain free, with the
aim of preventing the clogging or blockage of the impeller.
GR models have a rotating knife with three blades that cut fine solids
and filaments and prevents the blockage of the impeller.
Periodically check that the knife and the plate of the shredding system
are free from residues.
During cleaning operations and maintenance, always unplug the pump
from power supply. Work with recommended personal protective
equipment and pay the utmost attention.
6. ELECTRIC CONNECTIONS (fig. 14 - 15 page 129-130)
All operations connecting the motor pump to the electricity supply
must be performed by technicians qualified to operate in areas with
a potentially explosive atmosphere and in full compliance with current
regulations.
WARNING: To protect the power supply cable, avoid
twisting, pulling and/or accidental crushing.
The ends of the power supply cable must be connected to an
electric panel certified for use in potentially explosive atmospheres if it
is installed in a hazardous area or to a normal electric panel suitable
for the atmosphere in which it is installed if the connection is found
to be in a safe area, always in accordance with the installation rules.
In single-phase explosion-proof pumps with a reverse capacitor
and any external capacitor circuit breakers, the capacitors are
included in the supply but they are not connected to the pump
cable as they need to be connected internally to the electric panel
certified for use in potentially explosive atmospheres, if being in-
stalled in a hazardous area.
Before wiring check that:
•
the tension and frequency of the power line are equal to that indica
-
ted on the metal plaque on the pump;
•
the absorbency indicated on the metal plaque is less than the maxi
-
mum current supplied to the system;
•
the power line is earthed and has a magnetothermic differential in
respect to the regulations in force
•
the electric cables are not in any way damaged.
Always connect the pump to the equipotential earth using the screw
on the motor body.
The electrical connection phase on models without a plug must be
carried out by first connecting the yellow-green earth cable and then
the other connections.
To protect the pump motor use an adequate overload cutout suited to
the electrical characteristics shown on the metal identification plaque.
Using an ammeter, check that the absorbency of the installed pump is
within the limits indicated on the metal pump.
The operation and electrical safety of the ZENIT electric pump are
guaranteed by the configuration provided from the factory.
WARNING:
Any modifications (e.g. adding a piece of cable to the ori
-
ginal) can be considered a deviation of the pump characteristics and
can cause explosions.
6.1 Thermal protection
All of the -EX versions are equipped with a protection system against
overheating of the engine through means of a bimetal thermal protec-
tor which detects the temperature of the pump wrapping of the stator.
The ends are marked with a sticker upon which is written “THERMAL
PROTECTION”.
The electric panel must be predisposed to guarantee the shutdown
of the motor when the thermal protection intervenes and to avoid the
automatic start-up of the pump which must only be started manually
Summary of Contents for DGN 150/6/65-80-100
Page 43: ...EL 43 better together 10 O ring OFF O R O R...
Page 64: ...BG 64 better together 10 OFF 9 4 20000 7000 9 5 20000 7000 9 6 O R O R...
Page 121: ...RU 121 better together 9 4 20000 7000 9 5 20000 7000 9 6 10 OFF...
Page 128: ...128 better together 13 DGF DRF MAF SMF GRF APF 13 DGN DRN MAN GRN APN A B C D E F A B C D E F...
Page 142: ...142 better together...
Page 143: ......
Page 144: ...zenit com better together Cod 27270101613200000 Rev 8 01 11 19...