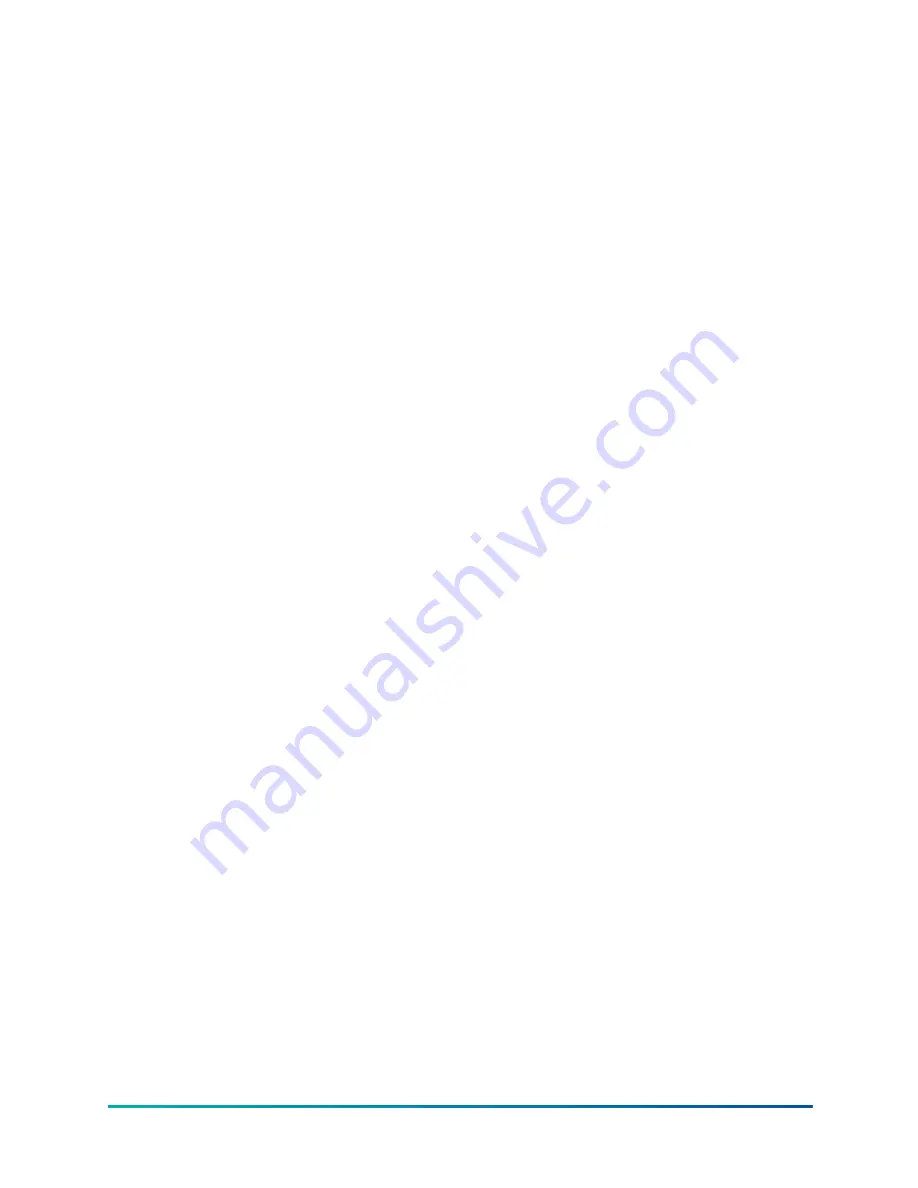
while starting the Lag compressor. The Override Time Remaining displays the time remaining
in the Valve Preset mode or the time remaining in the Lag Start mode. In the first case, it is the
time remaining in the Valve Preset Timer plus the time remaining of the first 3 minutes of lead
compressor run time. In the second case, it is the time remaining in the lag compressor pre-lube
cycle plus the time remaining in the first 3.5 minutes of lag compressor run time.
The
Lead Compressor Pulldown Time
setpoint can be used to limit the chiller to single
compressor operation for a specified duration (0-255 minutes) when starting the chiller. While
this pulldown time is in effect,
System In Lead Compressor Pulldown
is displayed on the
System Details line along with the time remaining in the period. During this time, only the lead
compressor is permitted to run. The lag compressor will not be brought online. After this period
has elapsed, the lag compressor can be brought on line per normal operation. While this period is
in effect, the lead compressor motor current will be limited to the value programmed for the
Lead
Compressor Pulldown Demand Limit
setpoint (30% to 100% FLA). This current limit applies to
the full load Amps of the lead compressor motor only, not the Chiller Full Load Amps (total of both
compressors). For example, if the Chiller Full Load Amps is 2000 A, then each compressor’s FLA
is 1000 A. If set to 80%, then the lead compressor motor current would be limited to 800 A (80% x
1000) for the duration of this period.
The Chiller Pulldown Demand Limit setpoint, which was used during the Chiller Pulldown Period
in previous software versions, has been removed in this and later software versions. Although this
setpoint has been removed, the logic in the Chiller Pulldown Period that is used to determine if it
is necessary to bring on the lag compressor (to meet load) still exists. This period is still in effect
from start until the Leaving Chilled Liquid Temperature is within 2ºF of the Leaving Chilled Liquid
Temperature setpoint. However, the Chiller Pulldown In Effect LED (that indicated when the Chiller
Pulldown Period is in effect) has been eliminated from the MOTOR Screen to avoid confusion with
the Lead Compressor Pulldown Demand Limit feature.
After the Lead Compressor Pulldown Time setpoint has elapsed, the chiller current limit is limited
to the value programmed for the Chiller Current Limit setpoint. As in previous software versions,
this setpoint is applied to the total chiller current (30% to 100% of the chiller Full Load Amps). For
example, if the chiller FLA is 1600 A, the FLA of each motor is 800 A. If this setpoint is set to 70%, the
chiller current would be limited to 1120 A. If both compressors are running, each would be limited
to 560 A. If only one motor is running, the motor would be allowed to operate all the way up to its
full load Amps of 800 A, because the total chiller current is being limited to 1120 A.
Compressor lockout
The Compressor Lockout setpoint, available on the Capacity Compressor Cycling screen, can be
used to lockout either compressor. The designated compressor is then unable to run. This feature
is useful when it is necessary to service a compressor.
A single compressor can be locked out while both compressors are running, without shutting
down the entire chiller. A soft shutdown is performed on the running compressor selected for
lockout and its status is changed to Lag, if it is not the lag compressor already. Upon completion
of Coastdown, the compressor remains locked out until the lockout is released. If there is only
one compressor running and it is the one targeted for lockout, the user must either shutdown the
entire chiller and then lock out the relevant compressor, or bring the other compressor online and
then lock out the relevant one. In previous software versions, a compressor can only be locked out
only while it is shutdown.
The following Safety or Cycling Conditions on a locked-out compressor will not cause the other
compressor to shut down. In previous software versions, these cycling and safety conditions that
occur on a locked out compressor cause the other compressor to shutdown or prevent it from
starting:
•
Motor Controller [#1/#2] – Contacts Open
•
Oil Pump [#1/#2] – Drive Contacts Open
13
Model YD Mod D with OptiView Control Center
Summary of Contents for YD Mod D
Page 2: ...2 Model YD Mod D with OptiView Control Center...
Page 8: ...Nomenclature Model YD Mod D with OptiView Control Center 8...
Page 17: ...Figure 2 Chiller operation flow chart 17 Model YD Mod D with OptiView Control Center...
Page 18: ...Figure 2 Chiller operation flow chart Model YD Mod D with OptiView Control Center 18...
Page 19: ...Figure 2 Chiller operation flow chart 19 Model YD Mod D with OptiView Control Center...
Page 20: ...Figure 2 Chiller operation flow chart Model YD Mod D with OptiView Control Center 20...
Page 21: ...Figure 2 Chiller operation flow chart 21 Model YD Mod D with OptiView Control Center...
Page 22: ...Figure 2 Chiller operation flow chart Model YD Mod D with OptiView Control Center 22...
Page 150: ...Figure 57 Sample printout status Model YD Mod D with OptiView Control Center 150...
Page 151: ...Figure 57 Sample printout status 151 Model YD Mod D with OptiView Control Center...
Page 152: ...Figure 58 Sample printout setpoints Model YD Mod D with OptiView Control Center 152...
Page 153: ...Figure 58 Sample printout setpoints 153 Model YD Mod D with OptiView Control Center...
Page 154: ...Figure 59 Sample printout schedule Model YD Mod D with OptiView Control Center 154...
Page 155: ...Figure 60 Sample printout sales order 155 Model YD Mod D with OptiView Control Center...
Page 156: ...Figure 61 Sample printout history Model YD Mod D with OptiView Control Center 156...
Page 157: ...Figure 61 Sample printout history 157 Model YD Mod D with OptiView Control Center...
Page 159: ...Figure 64 Sample printout custom screen report 159 Model YD Mod D with OptiView Control Center...