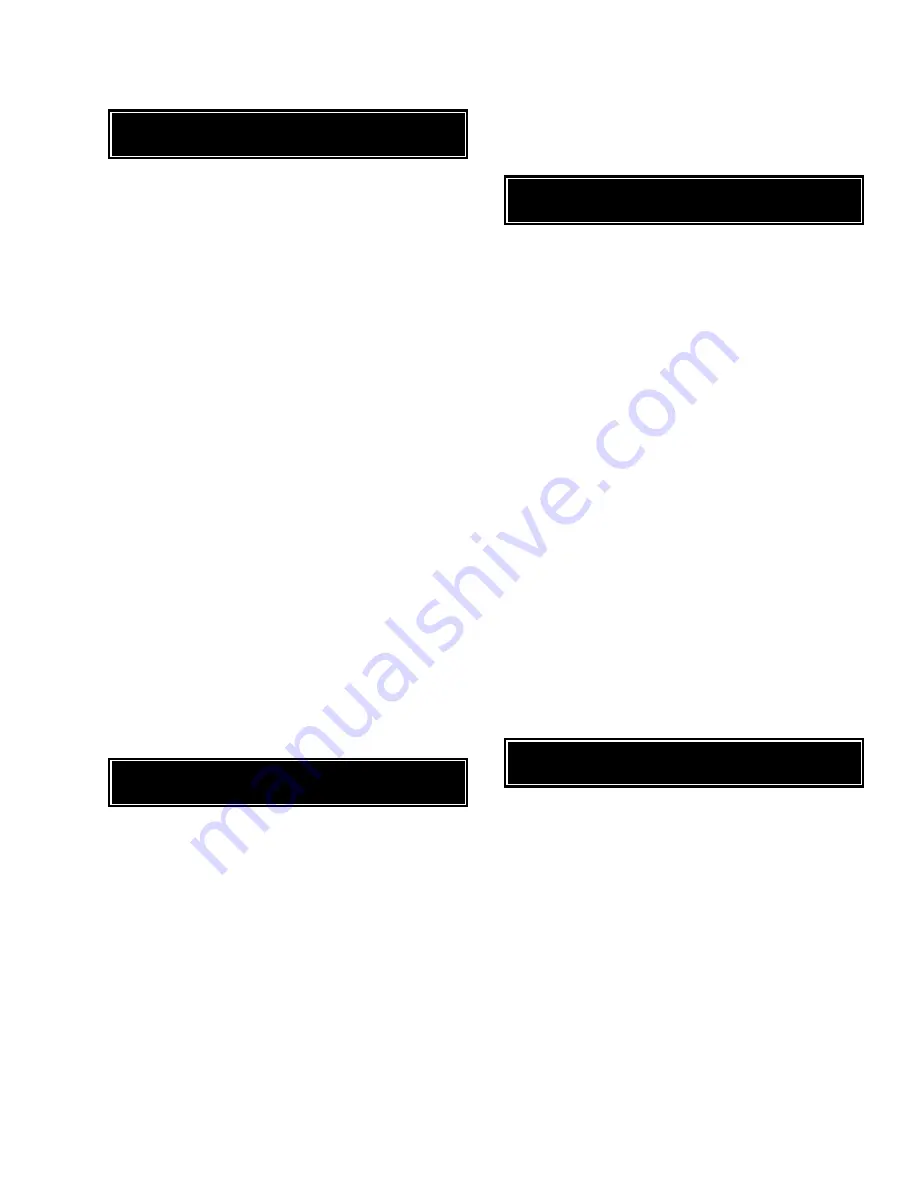
FORM 150.65-NM4
45
YORK INTERNATIONAL
for programming this control will be discussed in the
SELECTION OF RETURN OR LEAVING CHILLED LIQ-
UID CONTROL Section (Page 50).
ANTI RECYCLE TIME
The ANTI RECYCLE TIME selection allows the user to
select the compressor anti-recycle time to best suit his
needs. Motor heating is a result of inrush current when
the motor is started. This heat must be dissipated be-
fore another start takes place or motor damage may re-
sult. The anti-recycle timer assures the motor has suffi-
cient time to cool before it is again restarted.
An adjustable timer allows for the motor cooling required,
but gives the user the ability to extend the timer to cut
down on cycling. In some applications fast compressor
start response is necessary, in others it is not. These
needs should be kept in mind and the timer should be
adjusted for the longest period of time tolerable. Although
300 seconds is adequate motor cooling time, longer pe-
riods will allow even more heat dissipation, reduce cy-
cling, and possibly increase motor life.
To program the ANTI RECYCLE TIME, key in the de-
sired value and press the ENTER key. The new value will
be entered into memory and the display will advance to
the next user programmable limit.
The micro will accept a range of programmable values
between 300 - 600 seconds for this operating control.
LEAVING WATER TEMP CUT-OUT
The LEAVING WATER TEMP CUT-OUT protects the
chiller from an evaporator freeze-up should the chilled
liquid temp drop below the freeze point. This situation
could occur under low flow conditions or if the micro panel
SETPOINT values are improperly programmed. Anytime
the leaving chilled liquid temperature (water or glycol)
drops to the cut-out point, the chiller will shut down.
Restart will occur when temperature rises above the cut-
out if the anti-recycle timers are satisfied.
For chilled water applications (comfort cooling, SW1
OPEN), the cut-out is automatically set at 36.0°F (2.2°C).
This covers applications where leaving water tempera-
tures are not designed to go below 40.0°F (4.4°C). If
chilled liquid (glycol) temperatures are required below
40°F, the cut out should be programmed for 4°F (2.2°C)
below the desired leaving chilled liquid temperature.
AVERAGE CURRENT UNLOAD
The purpose of AVERAGE CURRENT UNLOAD is to pro-
vide adequate motor cooling and to prevent the motor from
faulting on high motor current. The motor current unload
feature only unloads a compressor by a single step. This
provides more cooling to the motor and at the same time
still attempt to pull the water temperature down.
Unloading will only occur when a compressor is running
with at least one step of loading above a fully unloaded
state. This feature will under no circumstances shut a
compressor off.
Whenever Motor Current Unloading is activated, the com-
pressor will stay in the unloaded state for 5 minutes.
After the 5 minute time period, the micro will look at
motor current once again. If motor is 25% below the pro-
grammed Motor Current Unload point, the compressor
will be allowed to reload, if water temperature allows.
To program the Motor Current Unload, key in the desired
value and press the ENTER Key. The new value will be
entered into memory and the display will advance to the
next user programmable limit.
The micro will accept a range of programmable values
between 80 - 105% for the unload point. A setting of
100% is recommended for the unload point.
NOTE: When programming values from 80 - 99%, it is
first required to key in a “0”. Example: 090%.
RATE CONTROL TEMP
The RATE CONTROL TEMP establishes a temperature
range over which the micro may override normal system
loading timers and react to actual rate of change of re-
turn and leaving water temperature. This temperature
range is slightly above the setpoint with its band width
being programmable. This control works in conjunction
with the RATE SENSITIVITY which is also programmable.
These controls allow the chiller to adapt to a full range of
applications. Depending on how the controls are set up
the chiller can be adapted to provide maximum response,
demand limiting/energy saving, or reduced loader and
compressor cycling. Typically this value should be
programmed for 00.1°F (0.05°C). When programming
values like 00.1°F (0.05°C), it is first required to key
in “00”. Example: 00.1°F (0.05°C). Additional details
R A T E
C O N T R O L
T E M P
= 0 8 . 0
F
A N T I
R E C Y C L E
T I M E
=
6 0 0
S E C S
L E A V I N G
W A T E R
T E M P
C U T O U T
=
3 6 . 0
F
A V E R A G E
C U R R E N T
U N L O A D
=
1 0 0
% F L A
Summary of Contents for Millennium YCAJ150
Page 21: ...FORM 150 65 NM4 21 YORK INTERNATIONAL LD02461 FIG 6 ELEMENTARY DIAGRAM Cont d...
Page 22: ...22 YORK INTERNATIONAL ELEMENTARY DIAGRAM...
Page 24: ...24 YORK INTERNATIONAL CONNECTION DIAGRAM FIG 7 CONNECTION DIAGRAM LD02463...
Page 25: ...FORM 150 65 NM4 25 YORK INTERNATIONAL FIG 7 CONNECTION DIAGRAM Cont d LD02462...
Page 30: ...30 YORK INTERNATIONAL FIG 8 SYSTEM WIRING Cont d LD02499...
Page 100: ...100 YORK INTERNATIONAL LD02654 FIG 37B LOUVER BRACKETS INSTALLATION...
Page 103: ...FORM 150 65 NM4 103 YORK INTERNATIONAL LD02656 FIG 39A LOUVER INSTALLATION SIDES...
Page 104: ...104 YORK INTERNATIONAL LD02654 FIG 39B LOUVER BRACKETS INSTALLATION...
Page 108: ...108 YORK INTERNATIONAL FIG 40B CONDENSER COIL LOUVER INSTALLATION FRONT AND BACK LD02659...
Page 110: ...110 YORK INTERNATIONAL FIG 41 REMOTE RESET BOARD LD02666 P1...