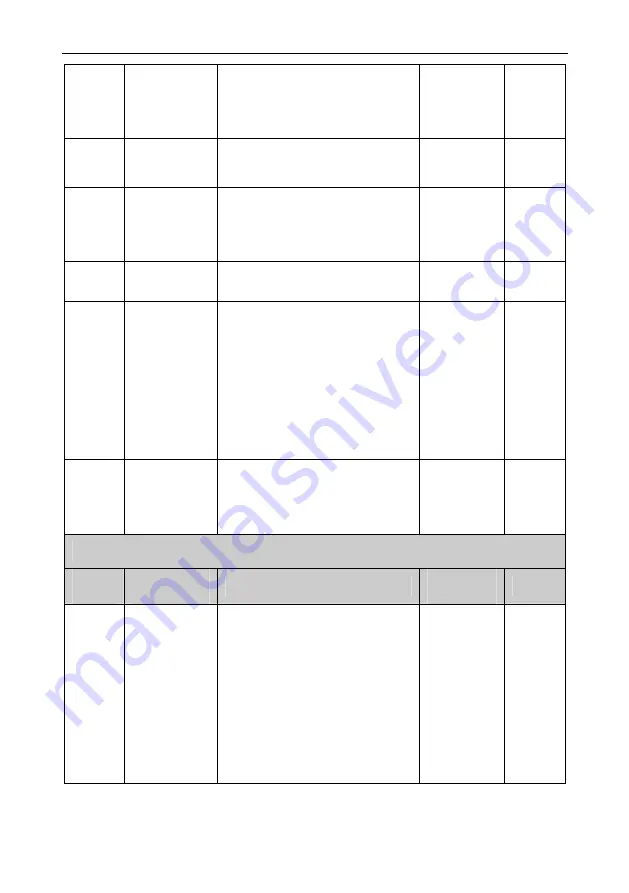
VD120 Series Inverter User Manual Function Parameter Table
-
49
-
FC-47
Acceleration/D
eceleration
Time Selection
of Simple PLC
Reference 14
0~3
0
○
FC-48
Run Time of
Simple PLC
Reference 15
0.0s (h)~6553.5s (h)
0.0s (h)
○
FC-49
Acceleration/D
eceleration
Time Selection
of Simple PLC
Reference 15
0~3
0
○
FC-50
Simple PLC
Run Time Unit
0: s
1: h
0
○
FC-51
Multi-reference
0 Setting
Method
0: Coding FC-00 given
1: AI1
2: Reserved
3: Reserved
4: PULSE
5: PID
6: Preset frequency(F0-09)given,
UP/DOWN can modify
7: Keypad potentiometer
0
○
FC-52
MS Speed
Acceleration/D
eceleration
Time Selection
Mode
0: Function code confirm
1: Terminal confirm
0
○
Fd MODBUS Communication
Function
Code
Parameter
Name
Setting Range
Factory
Default Value
Property
Fd-00
Baud Rate
0: 300BPS
1: 600BPS
2: 1200BPS
3: 2400BPS
4: 4800BPS
5: 9600BPS
6: 19200BPS
7: 38400BPS
8: 57600BPS
9: 115200BPS
5
○
Summary of Contents for VD120 Series
Page 2: ......