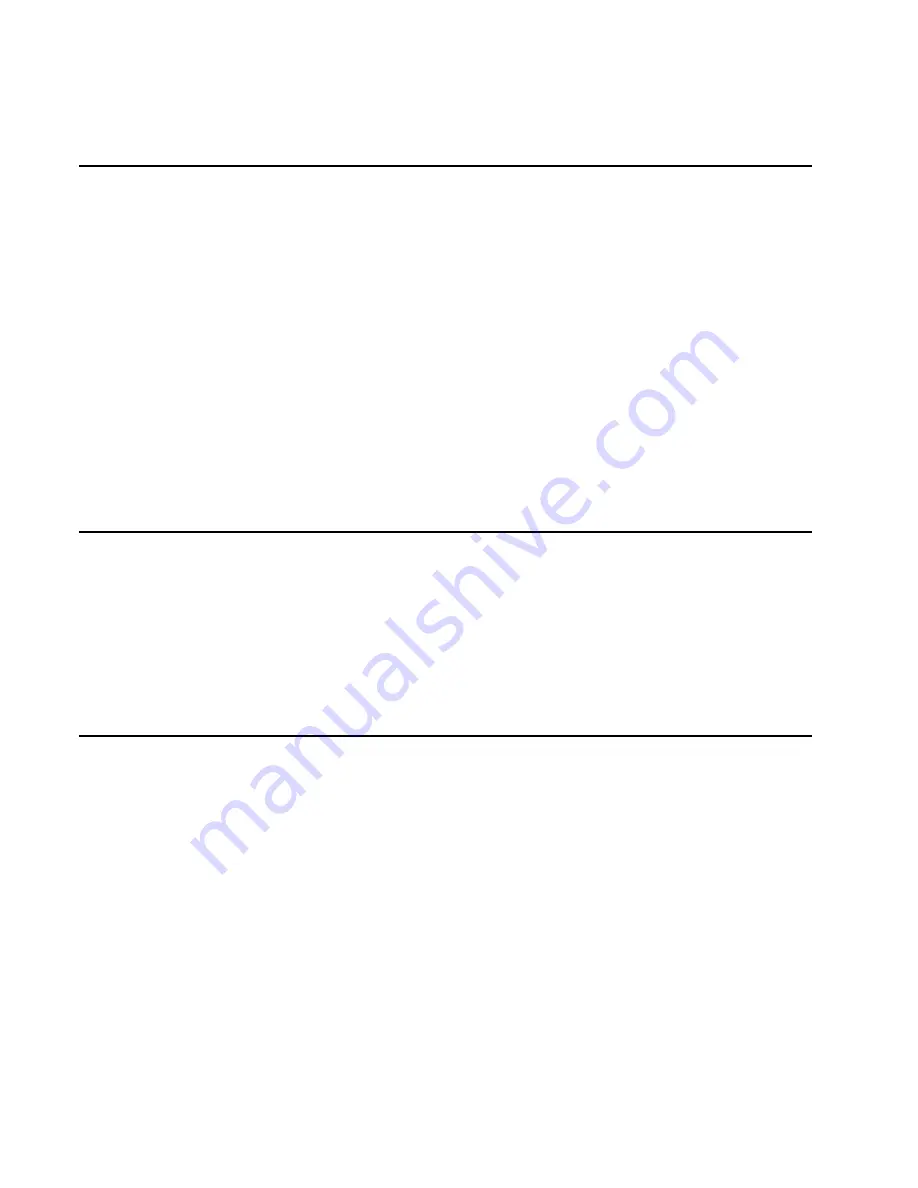
General Software Information
Flow Control
Two modes of flow control are supported, software (XON/XOFF) and hardware
(CTS, clear to send). The host can enable or disable flow control with command
614N.
The host can use software control characters (XON/XOFF) or the hardware
handshake line (CTS) to interrupt reader transmissions. If the reader is configured
for software flow control, the reader will cease transmitting if it receives the
command XOFF (command 13H). It resumes transmission only when it receives the
command XON (command 11H). Likewise, if the reader is configured for hardware
flow control, it will cease transmission if it detects that the CTS line is no longer
asserted. It will resume transmission when this line is asserted again. If flow control
is not needed, the reader should be configured for no flow control (command 6140).
Note:
TransCore recommends that XON/XOFF flow control be disabled while
using the error correcting protocol.
ID Separation
The host can select a unique ID separation of one ID (command 4100) or two IDs
(command 4101). The uniqueness timeout is fixed at 2 minutes. The reader default
operation is for a unique ID separation of one ID and a uniqueness timeout of
2 minutes. The host computer can disable the uniqueness check using the transmit all
IDs command (40) or buffer all IDs command (43). In this case, every tag ID
received will be transmitted without regard to uniqueness. The host can reinstate
uniqueness checking with the select ID separation commands (4100/4101).
Input Circuits
Both the RS–232 and RS–422 configurations used by SmartPass have two input
circuits, input0 and input1. The default configuration uses input0 as the presence
detection device line. RF power is automatically turned on only when the presence
detection device (loop detector or other device) detects a presence. Input1 is not used
directly by the reader; it is used by the host. The reader can be configured with
command 82N to generate input status change reports, which are transmitted like tag
IDs. The host can then respond based on the true/false (closed/open) status of the
inputs. The input circuits of the reader are designed to connect to a dry contact
closure. The input1 circuit is not available on Wiegand-configured SmartPass
systems.
Note:
The input circuits may be referred to as sense or sensor inputs in other
documentation.
6-5
Summary of Contents for SmartPass AI1611
Page 4: ......
Page 17: ...A Glossary...
Page 18: ......
Page 22: ...SmartPass Integrated Reader 2450 MHz High Voltage System Guide A 6...
Page 23: ...B System Specifications...
Page 24: ......
Page 26: ...SmartPass Integrated Reader 2450 MHz High Voltage System Guide B 4...
Page 27: ...C Wiring Tables...
Page 28: ......
Page 32: ...SmartPass Integrated Reader 2450 MHz High Voltage System Guide C 6...
Page 33: ...1 Introduction...
Page 34: ......
Page 40: ...SmartPass Integrated Reader 2450 MHz High Voltage System Guide 1 8...
Page 41: ...2 Preparing the Site...
Page 42: ......
Page 52: ...SmartPass Integrated Reader 2450 MHz High Voltage System Guide 2 12...
Page 53: ...3 Quick SmartPass Test...
Page 54: ......
Page 63: ...4 Installing Tags on Vehicles...
Page 64: ......
Page 71: ...5 Installing SmartPass...
Page 72: ......
Page 90: ...6 General Software Information...
Page 91: ......
Page 99: ...SmartPass Integrated Reader 2450 MHz High Voltage System Guide 6 10...
Page 100: ...7 Modes of Operation...
Page 101: ......
Page 106: ...8 Communication Protocols...
Page 107: ......
Page 124: ...9 Commands...
Page 125: ...SmartPass Integrated Reader 2450 MHz High Voltage System Guide 9 2...
Page 174: ...10 Troubleshooting...
Page 175: ......
Page 179: ...SmartPass Integrated Reader 2450 MHz High Voltage System Guide 10 6...