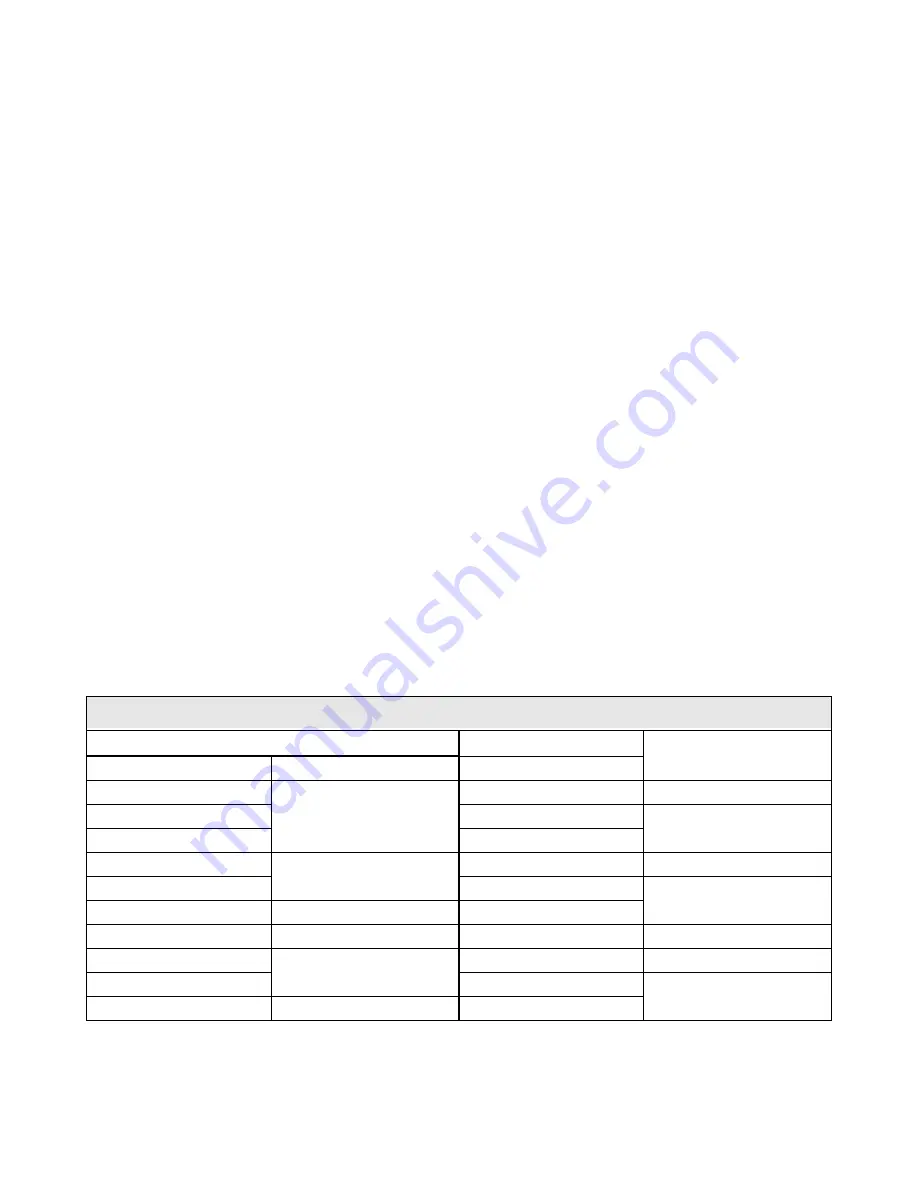
G7 ASD Operation Manual
11
Units received as an Open Chassis shall not be placed into operation until being placed into an
approved enclosure that will protect personnel against electrical shock.
Opening and closing of enclosures or barriers should be possible only with the use of a key or a
tool.
3.
Cabling — The power, filter, and motor cables shall be of the appropriate current rating. The
cables shall be connected in accordance with the guidelines of the manufacturer and the applicable
local and national agencies. A 4-core screened cable (such as RS 379-384) is to be used for the
power and earth connections to minimize RF emissions. Control cabling must be screened using
P/N RS 367-347 or a similar component.
4.
Grounding — The mains (input) ground shall be connected at the ground terminal provided on the
filter. The filter and motor shall be grounded at the ground terminals provided in the ASD.
5.
Screening — The mains (input) screen is to be connected to the metallic back-plane at the filter;
remove any finish coating as required. The screen over the filter output cables, the motor cable
screen, and the control wire screens must be connected to the ASD case using glands or conduit
connectors. The motor cable screen shall be connected to the motor case. When using a braking
resistor, the cabling between the resistor and ASD shall also be screened. This screen shall connect
to both the ASD enclosure and the resistor enclosure.
6.
Where residual-current-operated protective device (RCD) is used for protection in case of direct or
indirect contact, only RCD of type B is allowed on the supply side of this Electronic Equipment
(EE). Otherwise, another protective measure shall be applied, such as separation of the EE from the
environment by double or feinforced insulation, or isolation of the EE and the supply system by a
transformer.
See the G7 Filter Selection below for the recommended input filters for a given typeform.
Table 1.
G7 Filter Selection Table
230V
VT130G7U4110B
FN258-30
VT130G7U2010B
FN258-7
VT130G7U4160B
VT130G7U2015B
FN258-16
VT130G7U4220B
FN258-42
VT130G7U2025B
VT130G7U4270B
FN258-55
VT130G7U2035B
VT130G7U4330B
VT130G7U2055B
FN258-30
VT130G7U4400B
FN258-75
VT130G7U2080B
VT130G7U4500B
FN258-100
VT130G7U2110B
FN258-42
VT130G7U4600B
VT130G7U2160B
FN258-75
VT130G7U4750B
FN258-130
VT130G7U2220B
FN258-100
VT130G7U410KB
FN258-180
VT130G7U2270B
VT130G7U412KB
FS5236-300
VT130G7U2330B
FN258-130
VT130G7U415KB