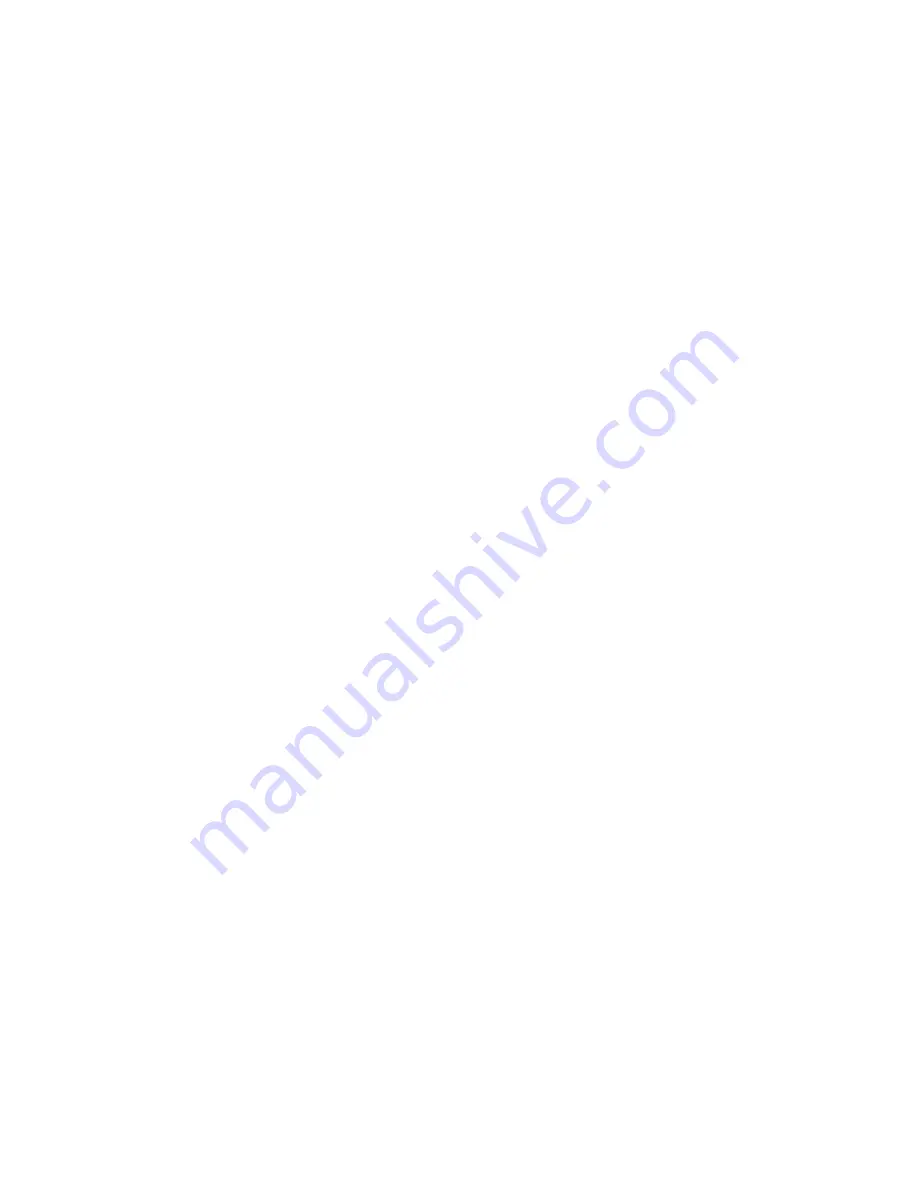
6
G7 ASD Operation Manual
referenced if three or more power conductors are run in the same conduit (refer to 2002 NEC
Article 310 adjustment factors on page 70-142).
•
Ensure that the 3-phase input power is Not connected to the output of the ASD. This will damage
the ASD and may cause injury to personnel.
•
Do not install the ASD if it is damaged or if it is missing any component(s).
•
Do Not connect resistors across terminals PA – PC or PO – PC. This may cause a fire.
•
Ensure the correct phase sequence and the desired direction of motor rotation in the Bypass mode
(if applicable).
•
Turn the power on only after attaching and/or securing the front cover.
Protection
•
Ensure that primary protection exists for the input wiring to the equipment. This protection must be
able to interrupt the available fault current from the power line. The equipment may or may not be
equipped with an input disconnect (option).
•
All cable entry openings must be sealed to reduce the risk of entry by vermin and to allow for
maximum cooling efficiency.
•
Follow all warnings and precautions and do not exceed equipment ratings.
•
If using multiple motors provide separate overload protection for each motor and use V/f control.
•
External dynamic braking resistors must be thermally protected.
•
It is the responsibility of the person installing the ASD or the electrical maintenance personnel to
setup the Emergency Off braking system of the ASD. The function of the Emergency Off braking
function is to remove output power from the drive in the event of an emergency. A supplemental
braking system may also be engaged in the event of an emergency.
For further information on
braking systems, see
DC Injection Braking Start Frequency on pg. 105
and
Dynamic Braking
Enable on pg. 112
.
Note:
A supplemental emergency stopping system should be used with the ASD. Emergency
stopping should not be a task of the ASD alone.
•
Follow all warnings and precautions and do not exceed equipment ratings.