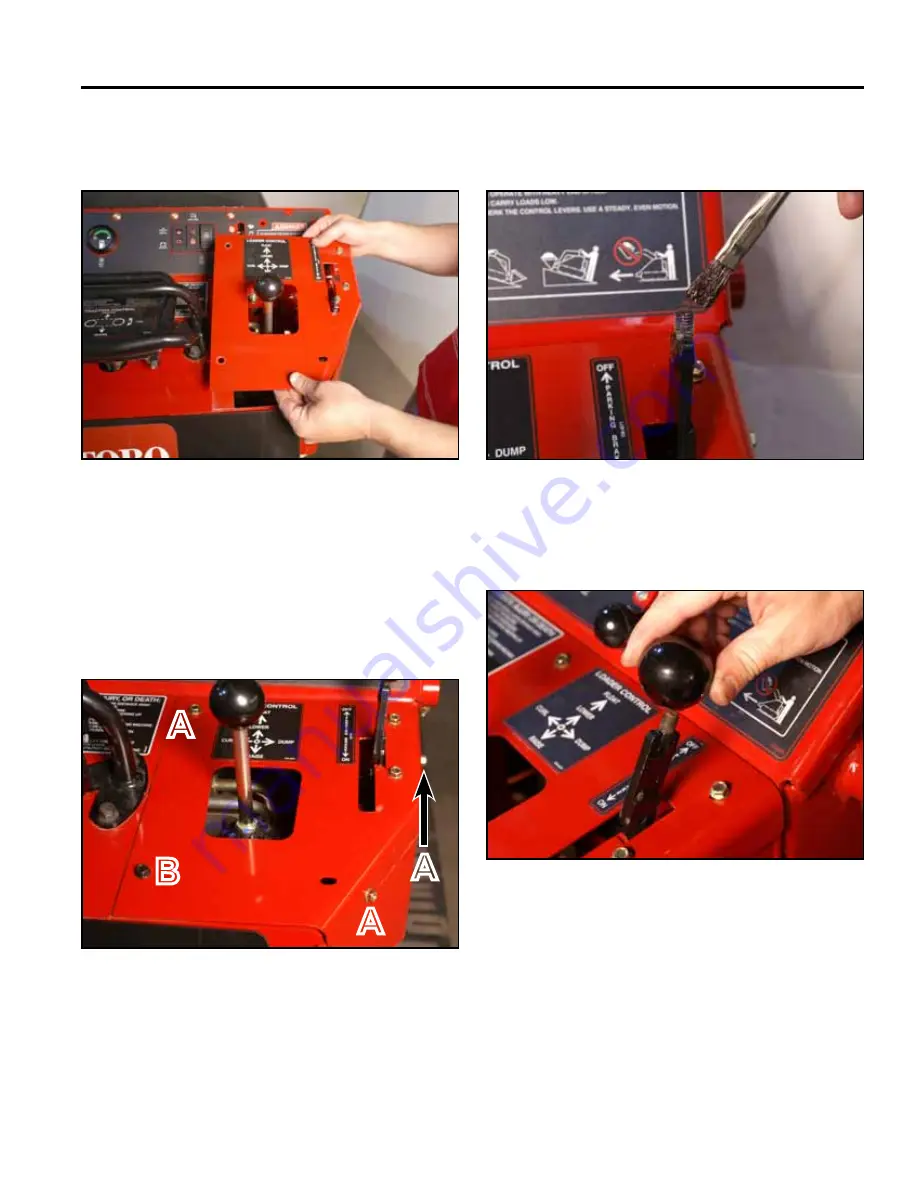
BRAKES
8-53
TX525 Service Manual
Rev. 000
8. Position the right panel onto the control panel
assembly (Fig. 1832).
10. Apply thread locking compound (Loctite 416 or
equivalent) to brake handle threads (Fig. 1834).
A. Self-tapping screw (3)
B. Bolt and nut
Fig 1832
PICT-4343a
Fig 1834
PICT-5526
11. Install the knob onto the brake handle (Fig. 1835).
9. Using a 3/8” socket, install 3 self-tapping screws
securing the top right panel to the control panel
assembly. Using a 3/8” socket and a 7/16” socket,
install the bolt and nut securing the lower left corner
of the top right panel to the control panel assembly
(Fig. 1833).
Fig 1835
PICT-4342
Fig 1833
PICT-4341
A
B
A
A
Summary of Contents for Dingo TX 525
Page 1: ...TX525 Service Manual Sitework Systems Form No 492 9195...
Page 3: ...ii Rev 000 TX525 Service Manual 8 01 10 Revision 000 REVISIONS...
Page 11: ...x Rev 000 TX525 Service Manual TABLE OF CONTENTS THIS PAGE INTENTIONALLY LEFT BLANK...
Page 243: ...ENGINE 4 190 Rev 000 TX525 Service Manual THIS PAGE INTENTIONALLY LEFT BLANK...
Page 263: ...ELECTRICAL 5 20 Rev 000 TX525 Service Manual THIS PAGE INTENTIONALLY LEFT BLANK...
Page 377: ...HYDRAULIC SYSTEM 6 114 Rev 000 TX525 Service Manual THIS PAGE INTENTIONALLY LEFT BLANK...
Page 479: ...DRIVE SYSTEM 7 102 Rev 000 TX525 Service Manual THIS PAGE INTENTIONALLY LEFT BLANK...
Page 553: ...HYDRAULIC TESTING 9 20 Rev 000 TX525 Service Manual THIS PAGE INTENTIONALLY LEFT BLANK...