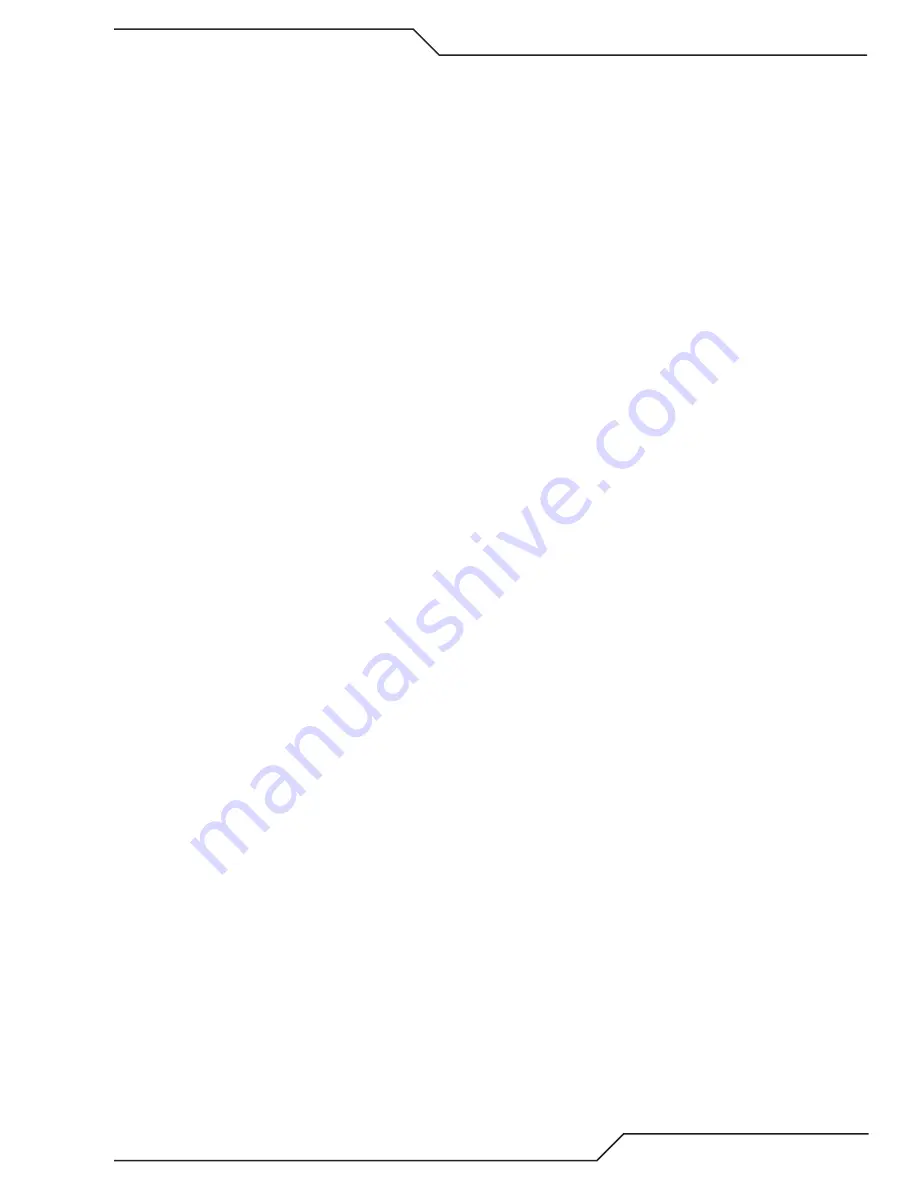
ULTRA-CUT 200 XT
Manual 0-5304
APPENDIX
A-89
ii. Remove power. Remove J11 from the Relay Board. On the J11 harness connector measure for resis-
tance of 400-800 ohms between pins 8 & 9. Do not use the meters diode scale. If resistance is less
than 400 ohms reverse your leads, you may be measuring the diode D202. If you measure a short,
much lower than 400 ohms, that may be the cause of not seeing any movement of the meter.
iii. A short or an open will require opening the 1Torch Module to determine the cause. Refer to the
Removing and opening the 1Torch module near the beginning of this section for directions to open
the module. In the case of a short determine if the D202 is bad or if the relay coil is shorted or open.
K201 is the relay toward the front of the module; K200 is the one to the rear.
704 Pressure Fault
Normal 1Torch operating pressure is 70-85 PSI. However minimum pressure to satisfy the pressure switch is
35 PSI. When the 1Torch trigger is pressed and the tests to determine that the consumables are in place (702)
and detection circuit is working (703) then the gas solenoid SOL4 is turned on. If the inlet gas pressure is above
35 PSI the pressure SW PS1 should close. Inlet Pressure below 35 PSI or the gas regulator not set above 35 PSI
will result in the 704 fault.
1. Confirm that an air supply capable of 70-85 PSI is connected into the inlet fitting of the 1Torch Module. If
an optional filter is used on the air line check that it is not plugged.
2. Trigger the torch momentarily to start the preflow. Adjust the regulator on the 1Torch Module clockwise to
increase the pressure to at least 70 PSI (up to 85 PSI for longer leads.)
3. If no pressure shows on the gauge the solenoid may be defective or the Relay Board is not turning it on.
a. First see if D2, Torch Gas ON LED on the Relay Board lights when pressing the torch SW. If not there is
a problem on the Relay Board or the CCM. If D2 is on skip to step 3c.
b. On the 40 ribbon cable between the CCM and the Relay Board (J23-J4) measure pin 4 relative to TP1. It
should be low, less than 2VDC, when pressing the 1Torch trigger. If it does not go low the CCM (or the
ribbon cable) is faulty. If pin 4 is low or goes low when the torch trigger is pressed but D2 on the Relay
Board is not on, then the Relay Board is bad.
c. If D2 on the Relay Board is on, with the torch SW pressed, you need to see if the Relay Board is supply-
ing power to the solenoid coil. First set up for measurement of 24 VAC between pins 13 & 14 on J11 of
the Relay Board. Press the 1Torch trigger. If no voltage the Relay Board may be bad.
d. If there was 24VAC in the previous measurement disconnect J11 and measure the resistance between pins
13 & 14 of the J11 harness connector. It should be about 21 ohms. This is the solenoid coil resistance. If
it’s open or the resistance is significantly less indicating the coil may be shorted you will have to replace
the solenoid assembly. The snubber RC, SA201, is NOT part of the solenoid assembly so do not discard
it, you will need it on the new solenoid. Refer to the Removing and opening the 1Torch module near the
beginning of this section for directions to open the module.
705 Start Cartridge Fault.
As explained in the section Operation of the 1Torch and its interlock circuits, during the preflow time the gas
pressure should cause the Start Cartridge to separate from the tip. After a slight delay allowing time for separa-
tion, the inverter is enabled to provide open circuit voltage which is measured and must be over 200 volts. If
the cartridge does not move, does not separate from the tip or something else is causing a tip to electrode short
it will set the 705 code. Also since it uses power from the inverter for this test, if the inverter does not put out
OCV the measured voltage will be low and the 705 fault is set.
1. If the DC indicator on the unit front panel flashes momentarily each time you press the 1Torch trigger it’s a
good sign the inverter is OK. Also try using the XT automation torch, if that works the inverter is good.
2. The most likely problem is the start cartridge is stuck. Disassemble the consumables and see if the cartridge
moves freely. Try a new cartridge and new tip.
This completes the Advanced Troubleshooting information.
This Page Intentionally Blank
Summary of Contents for ULTRA-CUT 200 XT
Page 6: ...This Page Intentionally Blank...
Page 15: ...ULTRA CUT 200 XT Manual 0 5304 SAFETY INSTRUCTIONS 1 5 This Page Intentionally Blank...
Page 28: ...ULTRA CUT 200 XT SPECIFICATIONS Manual 0 5304 This Page Intentionally Blank...
Page 76: ...ULTRA CUT 200 XT INSTALLATION Manual 0 5304 This Page Intentionally Blank...
Page 160: ...ULTRA CUT 200 XT APPENDIX Manual 0 5304 APPENDIX 17 Cap Bias Bottom PCB Layout Art A 11685_AB...
Page 162: ...ULTRA CUT 200 XT APPENDIX Manual 0 5304 APPENDIX 19 Suppressor PCB Layout Art A 11684_AB...
Page 165: ...ULTRA CUT 200 XT Manual 0 5304 APPENDIX A 39 This Page Intentionally Blank...
Page 227: ......