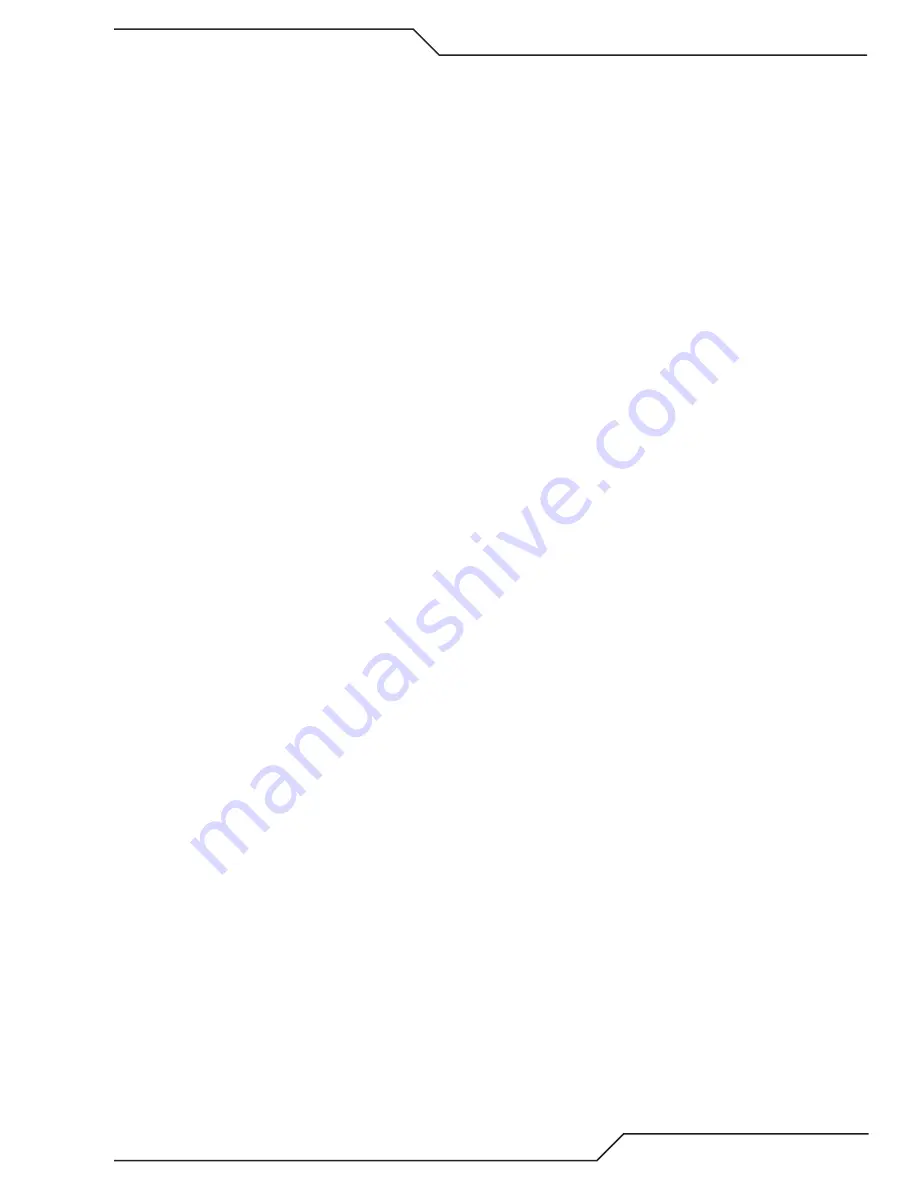
ULTRA-CUT 200 XT
Manual 0-5304
APPENDIX
A-59
Causes for 108 code:
• Gas Flow/pressure too low for consumable parts being used.
o If gas source pressure is not well regulated it is possible pressure may be OK at times and drop too
low at other times such as during a cut.
o A leak of the preflow/plasma gas after the pressure/flow control (GCM 2010, DPC, GCM 1000 XT)
can reduce the pressure/flow to the torch because some if it is bypassing the torch, while seeming to
have enough pressure/flow at the gas control.
• Cut current set too high for consumable parts being used.
• With DFC 3000 a faulty component would be expected to set a fault code in either the DPC or DMC.
However, if a wrong process is selected which doesn’t match the consumable type or if using a custom
process where pressure has been set too low or current too high that could cause 108 without setting any
faults in the DFC 3000.
• A broken pilot wire in the torch lead making intermittent contact can allow piloting or sometimes the
torch can transfer using only HF (high frequency). This intermittent connection will upset the tip voltage
measurement and can result in the 108 code. Symptom is - it may cut for a short time then fault. Check
for an open/broken torch lead pilot wire.
• Physically shorted torch body between anode (tip) and cathode (electrode).
The fault resulting in a 108 code is measured while cutting. It is more likely a shorted torch body, depending
on the resistance of the short, it will set code 208 (Unwanted Current) as that is measured prior to starting cut
However, it must be considered as a last resort.
109
Part Process not Configured.
This represents a status, not a fault. This is used with the DFC 3000 only. It means the operator hasn’t loaded
the cutting process from either the TSC 3000 or from the program embedded in the cutting table CNC control-
ler. The solution is to load a process. The code will continue to be displayed until the CNC Start is applied at
which time the code will clear.
110
Device locked.
This means the DPC or DMC is still in the process of downloading a new cutting process. This should only
occur with the DFC 3000 if you apply CNC Start before the download process is finished. The optional 1Torch
can be started while the automation process is being loaded.
Group 2 – Plasma Power Supply codes
General:
LEDS
Several LEDs are used as indicators on the different inverter module boards. RED LEDs indicate faults. Green
LEDs should be on for the most part. Green LEDs are: On the main board, D4-READY; On the Cap Bias Board,
D6, -12V, D11 +12VP (primary referenced), D13, +12V; On the Control board D24, PWM will only be on when
the inverter is enabled and its brightness varies with the duty cycle of the PWM.
Signals:
General description of some Inverter Signals passed to the CCM that can generate fault codes in Group 2.
“Ready” also called AC IN FLT (D4, READY LED, green, on Main Inverter board)
On the inverter main board we measure the input voltage. The 3 phases are rectified and lightly filtered to
achieve an average voltage. Due to the light filtering a missing phase will also lower the average voltage so it
will be detected. Voltage in the correct range turns on the READY LED D4 (on the far left of the main boards,
in the upper part of the “B” section or lower part of the “A” section). Voltage outside the correct range or miss-
ing phase will turn D4 off.
An AC Input Fault by itself (no other faults occurring at the same time) will set codes in the 241-246 group
depending on which inverter sees the problem.
Summary of Contents for ULTRA-CUT 200 XT
Page 6: ...This Page Intentionally Blank...
Page 15: ...ULTRA CUT 200 XT Manual 0 5304 SAFETY INSTRUCTIONS 1 5 This Page Intentionally Blank...
Page 28: ...ULTRA CUT 200 XT SPECIFICATIONS Manual 0 5304 This Page Intentionally Blank...
Page 76: ...ULTRA CUT 200 XT INSTALLATION Manual 0 5304 This Page Intentionally Blank...
Page 160: ...ULTRA CUT 200 XT APPENDIX Manual 0 5304 APPENDIX 17 Cap Bias Bottom PCB Layout Art A 11685_AB...
Page 162: ...ULTRA CUT 200 XT APPENDIX Manual 0 5304 APPENDIX 19 Suppressor PCB Layout Art A 11684_AB...
Page 165: ...ULTRA CUT 200 XT Manual 0 5304 APPENDIX A 39 This Page Intentionally Blank...
Page 227: ......