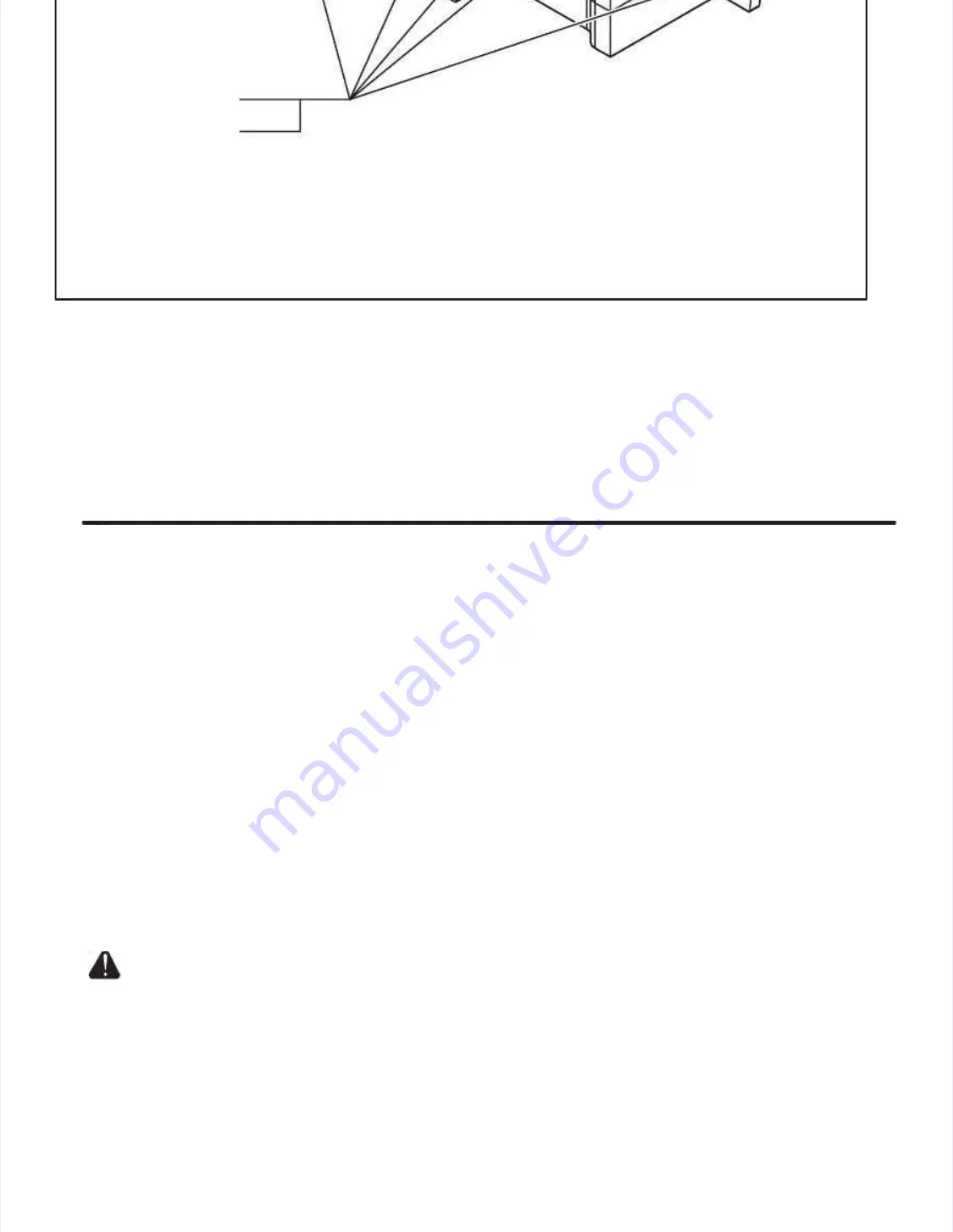
TX / TXH / TXB 180S - 400L (Rev. 4/23/07)
TX / TXH / TXB 180S - 400L (Rev. 4/23/07)
A-16
A-16
VT (3)
VT (3)
MT (FS)
MT (FS)
Illustration 1
Illustration 1
1.
1.
Chassis D
Chassis D
etail 5
etail 5
Fork Inspection,
Fork Inspection,
Repair
Repair
, and
, and
T
T
esting
esting
Forks in use shall be visually inspected daily and
Forks in use shall be visually inspected daily and
must be magnetic particle tested (magnafluxed)
must be magnetic particle tested (magnafluxed)
for cracks at intervals of not more than 2400 hours
for cracks at intervals of not more than 2400 hours
or whenever any defect or permanent deformation
or whenever any defect or permanent deformation
is detected.
is detected.
Severe applications
Severe applications
will require
will require
more
more
frequent inspection.
frequent inspection.
When forks are used in pairs, the rated capacity of
When forks are used in pairs, the rated capacity of
each fork shall be at least half of the manufactur-
each fork shall be at least half of the manufactur-
er’s rated capacity of the truck, and at the rated
er’s rated capacity of the truck, and at the rated
load center distance shown on the lift truck name-
load center distance shown on the lift truck name-
plate.
plate.
Fork inspection shall be carried out carefully by
Fork inspection shall be carried out carefully by
trained personnel with the aim of detecting any
trained personnel with the aim of detecting any
damage, failure, deformation, etc., which might
damage, failure, deformation, etc., which might
impair safe use.
impair safe use.
Any fork which
Any fork which
shows such
shows such
a
a
defect shall be withdrawn from service, and shall
defect shall be withdrawn from service, and shall
not be returned to service unless it has been sat-
not be returned to service unless it has been sat-
isfactorily repaired.
isfactorily repaired.
Do not weld on forged forks.
Do not weld on forged forks.
Failure to follow this warning could lead
Failure to follow this warning could lead
to
to
seriously weakened forks that could fail pre-
seriously weakened forks that could fail pre-
maturely und
maturely und
er normal
er normal
loads.
loads.
When neces-
When neces-
sary, the welding of fork bushings should only
sary, the welding of fork bushings should only
be done by qualified welders knowledgeable of
be done by qualified welders knowledgeable of
the appropriate welding practice.
the appropriate welding practice.
The fork shall be thoroughly examined visually for
The fork shall be thoroughly examined visually for
cracks and if considered necessary, subjected to a
cracks and if considered necessary, subjected to a
nondestructive crack detection process, special
nondestructive crack detection process, special
attention being paid to the heel and welds attach-
attention being paid to the heel and welds attach-
ing all mounting components to the fork blank.
ing all mounting components to the fork blank.
This inspection for cracks must also include any
This inspection for cracks must also include any
special mounting mechanisms of the fork blank to
special mounting mechanisms of the fork blank to
Any fork that
Any fork that
has a deviation
has a deviation
of greater than
of greater than
3
3
fork angle from the original specification shall not
fork angle from the original specification shall not
be returned to service.
be returned to service.
The difference in height of one set of forks when
The difference in height of one set of forks when
mounted on the
mounted on the
fork carrier s
fork carrier s
hall be checked.
hall be checked.
If
If
the difference in tip heights exceeds 3% of the
the difference in tip heights exceeds 3% of the
length of the blade, the set of forks shall not be
length of the blade, the set of forks shall not be
returned to service until repaired.
returned to service until repaired.
It shall be confirmed that the positioning lock is in
It shall be confirmed that the positioning lock is in
good repair and correct
good repair and correct
working order
working order
.
.
If ant
If ant
fault
fault
is found, the fork shall be withdrawn from service
is found, the fork shall be withdrawn from service
until satisfactory repairs have been effected.
until satisfactory repairs have been effected.
The fork blade and shank shall be thoroughly
The fork blade and shank shall be thoroughly
checked for wear, special attention being paid to
checked for wear, special attention being paid to
the vicinity
the vicinity
of the heel.
of the heel.
If the thic
If the thic
kness is reduc
kness is reduc
ed
ed
to 90% of the original thickness, the fork shall not
to 90% of the original thickness, the fork shall not
be returned to service.
be returned to service.
The support face of the top hook and the retaining
The support face of the top hook and the retaining
faces of both hooks shall be checked for wear,
faces of both hooks shall be checked for wear,
crushing, and
crushing, and
other local
other local
deformations.
deformations.
If these
If these
are apparent to such an extent that the clearance
are apparent to such an extent that the clearance
between the fork and the fork carrier becomes
between the fork and the fork carrier becomes
excessive, the fork shall not be returned to service
excessive, the fork shall not be returned to service
until repaired.
until repaired.
If the fork marking is not clearly legible, it shall be
If the fork marking is not clearly legible, it shall be
renewed.
renewed.
Marking shall
Marking shall
be renewed
be renewed
per instruc-
per instruc-
tions from original supplier.
tions from original supplier.
Each fork shall be clearly stamped with its individ-
Each fork shall be clearly stamped with its individ-
ual load rating in an area readily visible and not
ual load rating in an area readily visible and not
subject to
subject to
wear.
wear.
Only the manufacturer of the fork or an expert of
Only the manufacturer of the fork or an expert of
equal competence shall decide if a fork may be
equal competence shall decide if a fork may be
i d f
ti
d
d th
i
h ll
i d f
ti
d
d th
i
h ll
https://www.forkliftpdfmanuals.com/
Summary of Contents for TX180S
Page 5: ...https www forkliftpdfmanuals com...
Page 13: ...1 2 1 2 Rev 11 94 Rev 11 94 https www forkliftpdfmanuals com...
Page 15: ...https www forkliftpdfmanuals com...
Page 17: ...https www forkliftpdfmanuals com...
Page 54: ...Hoist Circuit Hoist Circuit https www forkliftpdfmanuals com...
Page 83: ...https www forkliftpdfmanuals com...
Page 84: ...https www forkliftpdfmanuals com...
Page 85: ...https www forkliftpdfmanuals com...
Page 86: ...https www forkliftpdfmanuals com...
Page 144: ...o o l l e e r r https www forkliftpdfmanuals com...
Page 193: ...https www forkliftpdfmanuals com...
Page 216: ...Section 15C Section 15C https www forkliftpdfmanuals com...
Page 222: ...Hoist Circuit Hoist Circuit https www forkliftpdfmanuals com...
Page 234: ...https www forkliftpdfmanuals com...
Page 243: ...https www forkliftpdfmanuals com...
Page 245: ...https www forkliftpdfmanuals com...
Page 272: ...https www forkliftpdfmanuals com...
Page 274: ...https www forkliftpdfmanuals com...
Page 290: ...TX TXH TXB 180S 400L 07 TX TXH TXB 180S 400L 07 https www forkliftpdfmanuals com...