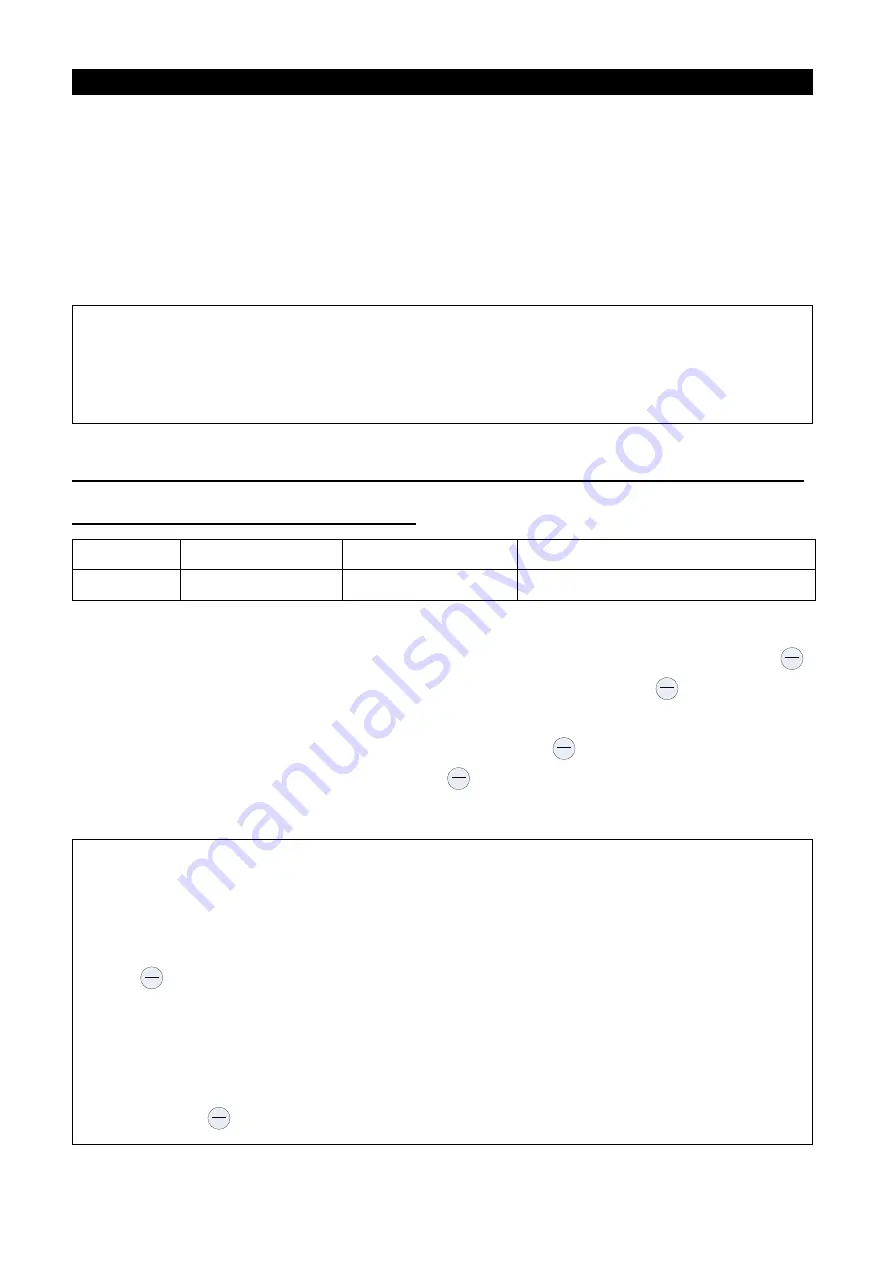
91
4. Parameter description
Parameter
<Setting>
• The higher the carrier frequency is, the lower the motor acoustic noise is. Unfortunately, greater
leakage current and larger noises generated by the inverter are resulted in.
• The higher the carrier frequency is, the more energy is dissipated, and the higher the temperature of
the inverter is.
• In case a mechanical resonance occurs in a system with the inverter, P.72 is helpful for improved
the performance just by adjusting its value.
Note: 1. The optimum carrier frequency shall be over 8 times greater than the target frequency.
2. When selected sensorless vector control (P.300=3), the carrier frequency can set to 2kHz, 6kHz, 10kHz,
14kHz. If the setting value is less 6kHz, the carrier frequency is 2kHz; If the setting value is less than
10kHz, the carrier frequency is 6kHz; If the setting value is less than 14kHz, the carrier frequency is
10kHz; If the setting value is more than 14kHz, the carrier frequency is 14kHz.
4.32
Stop or Reset function selection (P.75
)
P.75 “Stop or Reset function selection”
Parameter
Factory setting
Setting range
Remarks
75
1
0, 1
---
<Setting>
• When P.75=0, it is only suitable for PU mode and H2 mode (combined mode 2). Pressing
STOP
RESET
during running is used to stop the motor. Only at trouble state, we can press
STOP
RESET
for 1.0s to reset
the inverter, and then the inverter will show the power on state.
• When P.75=1, it is only suitable for the mode chosed. Pressing
STOP
RESET
during running is used to stop
the motor. Only at trouble state, we can press
STOP
RESET
for 1.0s to reset the inverter, and then the
inverter will show the power on state.
Note: 1. In normal or abnormal conditions, the reset can be executed by P.997.
2. There are two built-in program emulational thermally-accumulating relay, namely, ‘electronic thermal
relay’ and ‘IGBT module thermal relay’. Once reset occurs, the values of the two relay for ‘electronic
thermal relay’ and ‘IGBT module thermal relay’ will be set to zero.
3. In any modes except External mode or H2 mode, when P.75=1, the motor can be stopped by pressing
STOP
RESET
, then the inverter displays E0, and all the functions of the inverter are disabled. It can restart as
follows:
(1). Terminate external STF/STR command (In programmed operation mode, there’s no need to
terminate the start signal. The inverter will continue to run at the section where it stopped after
reset.)
(2). Press
STOP
RESET
for 1.0s.