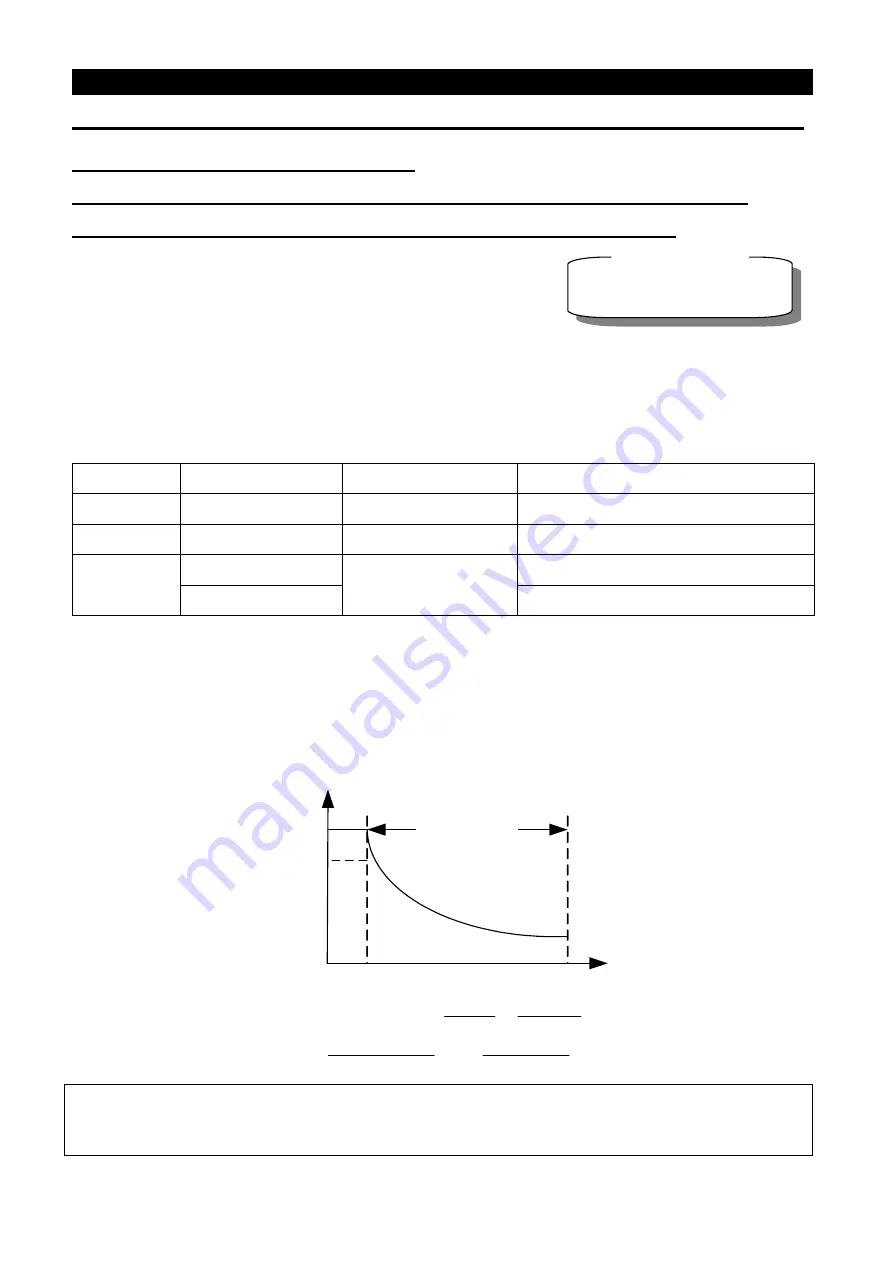
55
4. Parameter description
Parameter
4.12
Stall prevention (P.22, P.23, P.66)
P.22 “Stall prevention operation level”
P.23 “Offset coefficient for Stall prevention operation level at double speed”
P.66 “Stall prevention operation level reduction starting frequency”
Related parameters
P.189
“
Default function
”
● With a heavy load, in the case when a motor starts or the target frequency is adjusted (increasing),
the motor speed often can not tightly follow the output frequency. If the motor speed is lower than
the output frequency, the output current will increase to improve the output torque. However, if the
difference between the output frequency and the motor speed is too great, the motor torque will
decrease, which is called ‘stall’.
Parameter
Factory setting
Setting range
Remarks
22
200%
0~400%
---
23
9999
0~200%, 9999
---
66
50Hz
0~400Hz (Note 2)
When P.189=1
60Hz
When P.189=0
<Setting>
• During the period when a motor starts or the output frequency increases, the output current of the
inverter will increase. Once the output current exceeds the upper limit pre-set as the following
figure, the adjustment of the output frequency is paused automatically and will continue to proceed
until the motor captures the output frequency (at this moment the output current of the inverter will
decrease correspondingly).
P.22
Output frequency
Level decreasing
region
100%
Output current
percentage
P.66
(Full load current)
Level percentage=A+B×
P.22-A
P.22-B
×
P.23-100
B=
100
400
A=
P.66×P.22A
Output frequency
P.66×P.22A
Note: 1.If P.300=3, the real-time speed sensorless vector control function is selected, P.22 will be the torque limit
level as action.
2. If P.187=1, P.66 is in the range of 0~1000Hz.