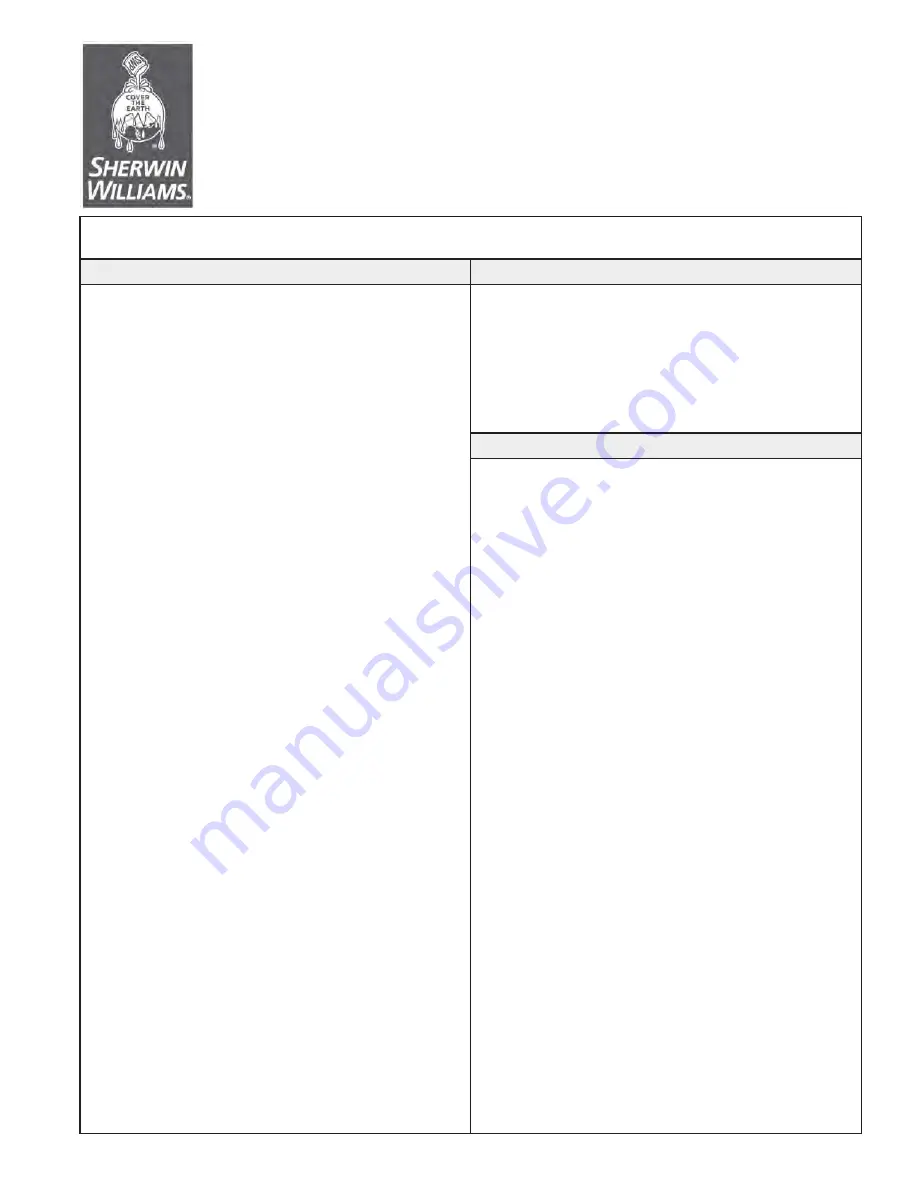
ACROLON™ 218 HS
ACRYLIC POLYURETHANE
P
ART
A
B65-600
G
LOSS
S
ERIES
P
ART
A
B65-650
S
EMI
-G
LOSS
S
ERIES
P
ART
B
B65V600
H
ARDENER
Revised 2/07
Industrial
&
Marine
Coatings
The following is a guide. Changes in pressures and tip sizes
may be needed for proper spray characteristics. Always purge
spray equipment before use with listed reducer. Any reduction
must be compatible with the existing environmental and ap-
plication conditions.
Reducer/Clean Up:
Spray ............................ Reducer R7K15
Brush/Roll .................... Reducer #132, R7K132
If reducer is used, reduce at time of catalyzation.
Airless Spray
Pressure ...................... 2500 - 2800 psi
Hose ............................ 3/8" ID
Tip ................................ .013" - .017"
Filter ............................. 60 mesh
Reduction ..................... As needed up to 10% by volume*
Conventional Spray
Gun ............................... Binks 95
Cap ............................... 63P
Atomization Pressure .. 50 - 70 psi
Fluid Pressure ............. 20 - 25 psi
Reduction ..................... As needed up to 10% by volume*
Brush
Brush ............................ Natural Bristle
Reduction ..................... As needed up to 10% by volume*
Roller
Cover ............................ 3/8" woven with phenolic core
Reduction ..................... As needed up to 10% by volume*
If specific application equipment is not listed above, equiva-
lent equipment may be substituted.
* Note: Reducing more than 10% by volume with R7K15 will
exceed 340g/L VOC
APPLICATION BULLETIN
S
URFACE
P
REPARATION
A
PPLICATION
C
ONDITIONS
A
PPLICATION
E
QUIPMENT
Temperature:
40°F minimum, 120°F maximum
(air, surface, and material)
At least 5°F above dew point
Relative humidity:
85% maximum
Surface must be clean, dry, and in sound condition. Remove
all oil, dust, grease, dirt, loose rust, and other foreign material
to ensure adequate adhesion.
Iron & Steel
Remove all oil and grease from surface by Solvent Cleaning
per SSPC-SP1. Minimum surface preparation is Commercial
Blast Cleaning per SSPC-SP6/NACE 3. For better perform-
ance, use Near White Metal Blast Cleaning per SSPC-SP10/
NACE 2. Blast clean all surfaces using a sharp, angular abra-
sive for optimum surface profile (1-2 mils). Prime any bare
steel the same day as it is cleaned or before flash rusting
occurs.
Aluminum
Remove all oil, grease, dirt, oxide and other foreign material
by Solvent Cleaning per SSPC-SP1. Primer required
Galvanized Steel
Allow to weather a minimum of six months prior to coating.
Solvent Clean per SSPC-SP1. When weathering is not pos-
sible, or the surface has been treated with chromates or sili-
cates, first Solvent Clean per SSPC-SP1 and apply a test patch.
Allow paint to dry at least one week before testing adhesion. If
adhesion is poor, brush blasting per SSPC-SP7 is necessary
to remove these treatments. Rusty galvanizing requires a mini-
mum of Hand Tool Cleaning per SSPC-SP2, prime the area
the same day as cleaned or before flash rusting occurs.
Poured Concrete
New
For surface preparation, refer to SSPC-SP13/NACE 6, or ICRI
03732, CSP 1-3. Surfaces must be clean, dry, sound and offer
sufficient profile to achieve adequate adhesion. Minimum
substrate cure is 28 days at 75°F. Remove all form release
agents, curing compounds, salts, efflorescence, laitance, and
other foreign matter by sandblasting, shotblasting, mechani-
cal scarification, or suitable chemical means. Refer to ASTM
D4260. Rinse thoroughly to achieve a final pH between 8.0
and 10.0. Allow to dry thoroughly prior to coating.
Old
Surface preparation is done in much the same manner as
new concrete, however, if the concrete is contaminated with
oils, grease, chemicals, etc., they must be removed by clean-
ing with a strong detergent. Refer to ASTM D4258. Form
release agents, hardeners, etc. must be removed by sand-
blasting, shotblasting, mechanical scarification, or suitable
chemical means. If surface deterioration presents an unac-
ceptably rough surface, Kem Cati-Coat Epoxy HS Filler/Sealer
is recommended to patch and resurface damaged concrete.
Fill all cracks, voids and bugholes with Steel Seam VSE
Always follow the standard methods listed below:
ASTM D4258 Standard Practice for Cleaning Concrete.
ASTM D4259 Standard Practice for Abrading Concrete.
ASTM D4260 Standard Practice for Etching Concrete.
ASTM F1869 Standard Test Method for Measuring Moisture
Vapor Emission Rate of Concrete.
SSPC-SP 13/Nace 6 Surface Preparation of Concrete.
ICRI 03732 Concrete Surface Preparation
5.22A
Polyurethane
5.22A
continued on back
Summary of Contents for BN 5-12 Series
Page 13: ...TAB 1 DEVICE DATA SHEETS ...
Page 18: ...TAB 2 APPROVED SUBMITTAL ...
Page 23: ...All data subject to change without notice 1 800 ASK 4WEG www weg net 14 ...
Page 26: ...Your advantages our pumps ...
Page 45: ...ADV 2 13E And what can we get flowing for you Your nearest contact Or visit www seepex com ...
Page 117: ...TAB 3 INSTALLATION OPERATIONS AND MAINTENANCE ...
Page 133: ...Page 37 ...
Page 233: ...www weg net Manual of Electric Motors 64 ENGLISH Figure 2 1 IEC motor nameplate Page 135 ...
Page 234: ...www weg net Manual of Electric Motors 65 ENGLISH Figure 2 2 NEMA motor nameplate Page 136 ...
Page 306: ...TAB 4 AS BUILTS AND SUPPLEMENTAL INFORMATION ...
Page 307: ...R Page 29 ...
Page 308: ...R Page 30 ...