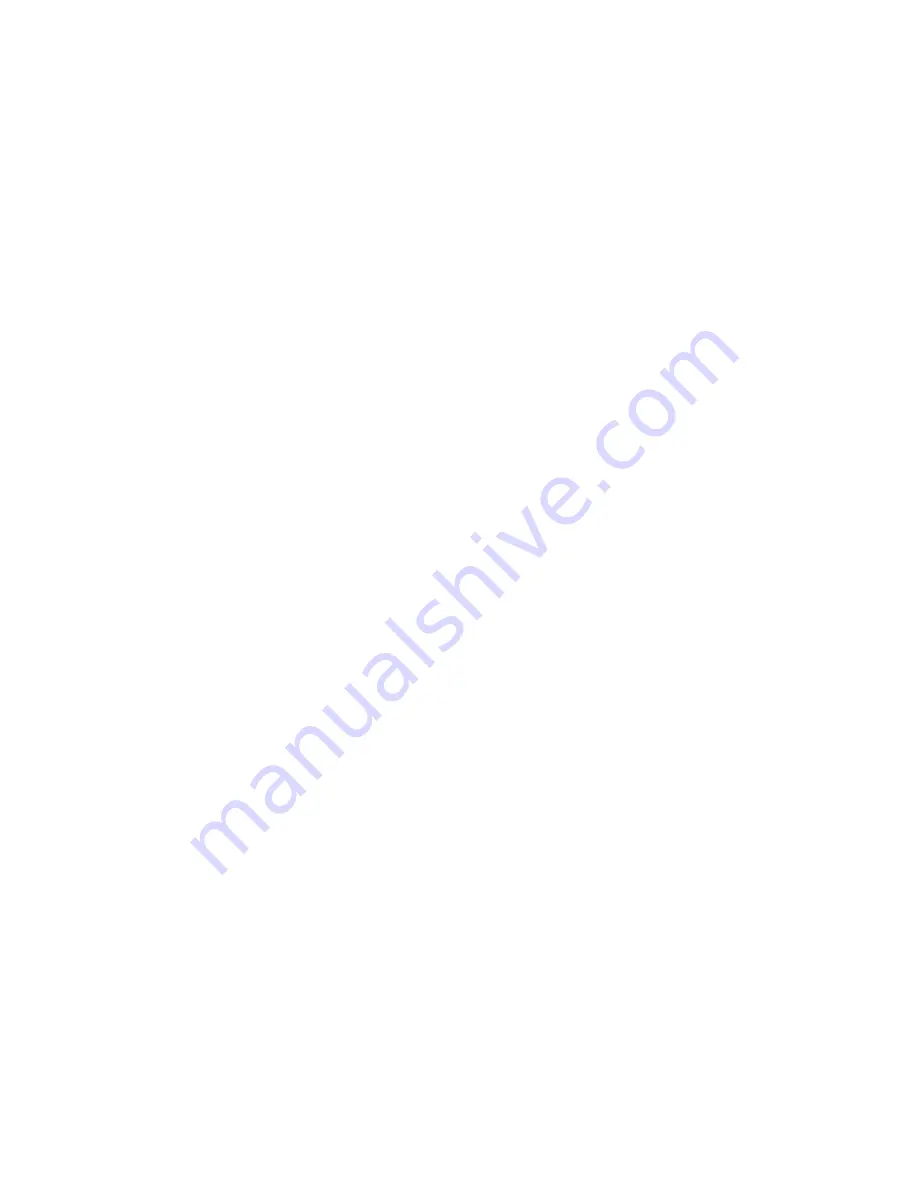
Proco Exansion Joint O&M Manual 6-15-2011
- 2 -
3.0 INSTALLATION
PROCEDURES
3.1 M
ATING
F
LANGE
I
NSPECTION
:
Check that mating flanges are clean and free of all foreign matter before installing
rubber expansion joint. A flat face mating flange is preferred. If raised face flanges
are to be used, the flange lip is to be no more than 1/16" tall.
3.2 E
XPANSION
J
OINT
B
OLTING
:
Install the expansion joint against the mating pipe flanges and install bolts so that
the bolt head and washer are against the retaining rings. If washers are not used,
flange leakage can result (
particularly at the split in the retaining rings
). Flange-to-
flange dimension of the expansion joint must match the breech opening
3.2.1 Retaining rings have one side beveled. The beveled side at the I.D. of the
retaining ring should be installed against the rubber flange. This will prevent
the edge of the ring from cutting the rubber flange.
3.3 A
DJACENT
E
QUIPMENT
P
RECAUTION
:
Never install expansion joints that utilize split retaining rings next to wafer-type
check or butterfly valves. Serious damage can result to a rubber joint of this type
unless installed against full-faced flanges.
3.4 I
NSTALLATION
O
F
C
ONTROL
R
ODS
:
Assemble control rod plates to the outside of pipe flanges. Flange bolts used to
connect rubber expansion joint to adjacent pipe flanges will also connect control rod
plates to pipe flanges. Make sure the through-bolt is long enough to accommodate
both connections. Control rod plates should be equally spaced around the flange.
Size and pressure rating of the system will dictate the number of control rods per
expansion joint. (
Please see drawings of rubber expansion joints listed in the "De-
sign Section" of this manual.)
3.4.1 Insert control rods through plate holes. Steel spherical washers are to be
positioned at outer plate surface and backed up by movable double nuts.
Steel flat washers are to be positioned on inside plate surface and backed up
by movable double nuts. (
Please see drawing for specific expansion joint to
determine number of pieces {nuts, washers} per joint. Drawing information
can be found in the
"Design Section"
of this manual
.)
3.4.2 When setting control rod gaps, both inner and outer double nuts are to be
positioned to meet maximum compression (
inner nuts
) and maximum exten-
sion (
outer nuts
) requirements. Gaps are to be determined by the said engi-
neer and are to be no more than the listed movements on the corresponding
drawings found in the "Design Section" of this manual. (
Note: Please con-
tact Proco Products, Inc. by phone: 209-943-6088, facsimile: 209-943-2042,
or e-mail: [email protected], if there are any questions as to the
rated compression or extension movements.)
These two rated movements
are critical for determining correct setting for the double nuts.
Page 197
Summary of Contents for BN 5-12 Series
Page 13: ...TAB 1 DEVICE DATA SHEETS ...
Page 18: ...TAB 2 APPROVED SUBMITTAL ...
Page 23: ...All data subject to change without notice 1 800 ASK 4WEG www weg net 14 ...
Page 26: ...Your advantages our pumps ...
Page 45: ...ADV 2 13E And what can we get flowing for you Your nearest contact Or visit www seepex com ...
Page 117: ...TAB 3 INSTALLATION OPERATIONS AND MAINTENANCE ...
Page 133: ...Page 37 ...
Page 233: ...www weg net Manual of Electric Motors 64 ENGLISH Figure 2 1 IEC motor nameplate Page 135 ...
Page 234: ...www weg net Manual of Electric Motors 65 ENGLISH Figure 2 2 NEMA motor nameplate Page 136 ...
Page 306: ...TAB 4 AS BUILTS AND SUPPLEMENTAL INFORMATION ...
Page 307: ...R Page 29 ...
Page 308: ...R Page 30 ...