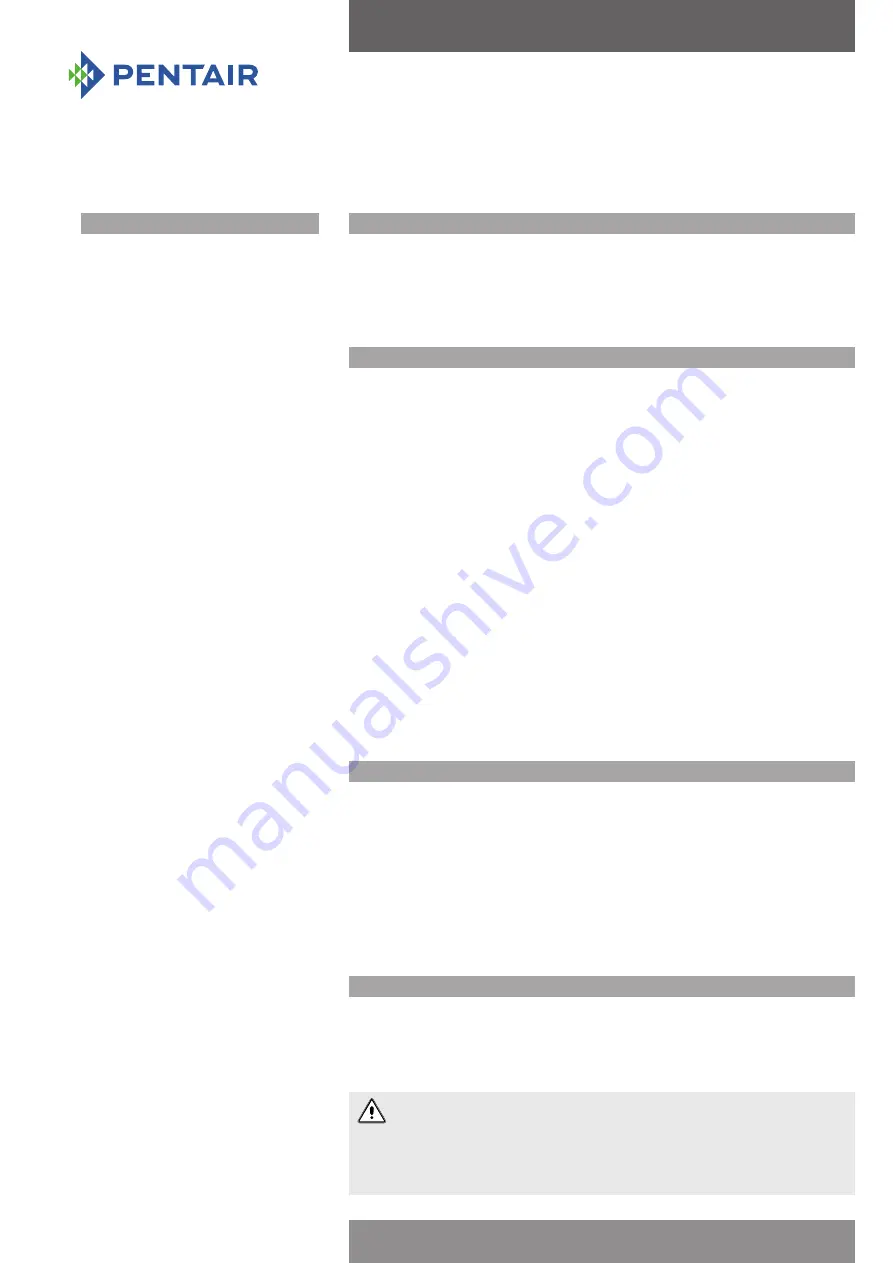
KUNKLE
Pressure Relief Valves
Installation and Operating Instructions
We reserve the rights to change the contents without notice
KUKMC-6302-EN-1305
Pre-Installation
Verification of Model and Service Media/
Capacity/Temperature/Pressure Limits
(Reference attached Model Description/
Guide.) Verify the Model Number on the
tag against the Model Number of the order.
For European service, verify the “CE Mark”
tag is connected to the valve. Verify the
Service Media, Capacity, and Temperature
and Pressure Limits of the valve against the
application. Please note the marked capacity
is based on Standard Temperature and
Pressure conditions and is valid only for the
service media noted on the catalog order
guide. Adjustments to the capacity must
be performed for different temperatures or
service media, and are the responsibility of the
end user to determine.
WARNING!
Removal of the seal wires or any attempt to adjust, repair or modify this product by non-VR
Certified personnel voids the product guarantee and may cause serious damage to equipment,
personal injury, and death. Kunkle Valve is not liable for any damage resulting from misuse or
misapplication of its products.
Installation
Always wear proper safety equipment, including safety glasses and ear protection.
1. Mount the valve in a vertical position so that the valve body is self-draining. If a body drain port
is provided, make sure it is open when required by the ASME code. Do not plug any bonnet vent
openings. The inlet piping should be as short as possible, with no elbows, and equal to or greater
than the size of the pressure relief valve inlet connection. This will help to limit the inlet pressure
drop to 3% or less when the valve is relieving.
2. When discharge piping is connected to valve outlet, make sure it is self-draining if a body drain
port is not used. The valve should not be connected to any discharge pipe that contains pressure
before the valve opens or to any pipe where the pressure build-up is greater than 10% of the set
pressure when the valve is open and relieving.
Discharge piping, other than a short tailpipe, must be supported. For steam service, a drip pan
elbow or flexible connection between the valve and the pipe should be used to prevent excessive
pipe stress, due to thermal expansion, from being imposed on the valve body.
3. For threaded valves, to prevent sealing compound from entering and damaging the valve,
apply a small amount of pipe thread sealing compound to external threads only. Do not put any
sealing compound on the first thread or on any internal threads. To do so may cause the sealing
compound to enter the valve and cause seat leakage.
Do not use the valve body or bonnet for installing the valve in threaded connections. Use the
wrench flats provided to tighten the valve to the connecting pipe. Torque valve enough to ensure
a pressure-tight seal and do not overtighten. To do so may cause valve leakage.
4. For flanged valves, use new gaskets and tighten the mounting studs evenly.
5. Do not paint, lubricate or allow contaminates to enter or cover the interior or any working parts
of the valve.
6. Remove gag screw (if valve is so equipped) before system start up.
Operation
1. Maintain a system operating pressure at least 5 psig or 10% below the set pressure of the valve,
whichever is greater. Operating too close to the valve set pressure will cause seat leakage and
will shorten the time between valve maintenance.
2. Do not use the safety valve as a control valve to regulate system operating pressure. Excessive
operation will cause the seat to leak and will require more frequent valve maintenance.
3. ASME Section I and VIII valves equipped with lift levers are designed to be operated only
when the system pressure is 75% of set pressure or greater. ASME Section IV valves may be
operated at any set pressure. When hand operating the valve, hold it open long enough to purge
any foreign matter from the seat area. If a cable or wire is attached to the lift lever for remote
actuation, make sure the direction of pull is the same as it would be if the lever were pulled
directly by hand.
Maintenance
Maintenance should be performed on a regular basis. An initial inspection interval of 12 months is
recommended. Depending on the service conditions and the condition of the valve, the inspection
interval may be decreased or increased. Use only Kunkle parts for repair. Depending on the local
jurisdictional requirements where the valve is installed, repairs may have to be made by a repair
facility holding a VR stamp.
Handling
This pressure relief valve is designed to protect equipment from overpressure. The valve should be
handled with care, not subjected to heavy shock loads, and protected to prevent contamination
from getting inside. It should be installed correctly per A.S.M.E. Boiler & Pressure Vessel Code
requirements, where applicable. Failure to do so could result in property damage or serious injury
to personnel. When hoisting the valve into position for installation, care should be exercised so that
lifting straps do not contact the valve lift lever.
Rev E 05/24/2007
Kunkle Valve Division
953 Old US 70, Black Mountain, NC 28711
www.kunklevalve.com
www.pentair.com/valves
Page 182
Summary of Contents for BN 5-12 Series
Page 13: ...TAB 1 DEVICE DATA SHEETS ...
Page 18: ...TAB 2 APPROVED SUBMITTAL ...
Page 23: ...All data subject to change without notice 1 800 ASK 4WEG www weg net 14 ...
Page 26: ...Your advantages our pumps ...
Page 45: ...ADV 2 13E And what can we get flowing for you Your nearest contact Or visit www seepex com ...
Page 117: ...TAB 3 INSTALLATION OPERATIONS AND MAINTENANCE ...
Page 133: ...Page 37 ...
Page 233: ...www weg net Manual of Electric Motors 64 ENGLISH Figure 2 1 IEC motor nameplate Page 135 ...
Page 234: ...www weg net Manual of Electric Motors 65 ENGLISH Figure 2 2 NEMA motor nameplate Page 136 ...
Page 306: ...TAB 4 AS BUILTS AND SUPPLEMENTAL INFORMATION ...
Page 307: ...R Page 29 ...
Page 308: ...R Page 30 ...