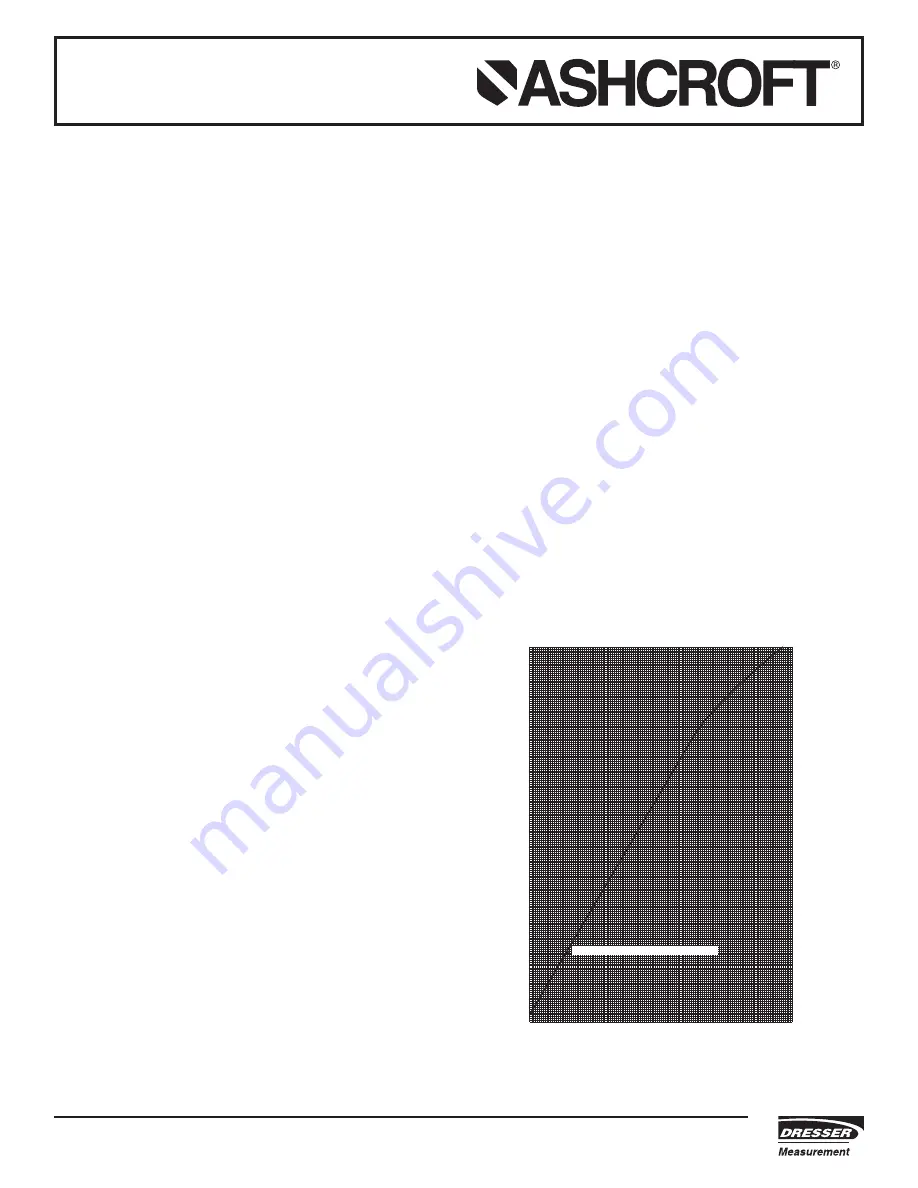
SELECTION
Pressure Ranges
– Select a gauge with a full scale pressure
range of approximately twice the normal operating pressure.
The maximum operating pressure should not exceed approxi-
mately 75% of the full scale range. Failure to select a gauge
range within this criteria may ultimately result in fatigue failure
of the Bourdon tube component.
INSTALLATION
Always use a wrench on the flats of the gauge socket to screw
the gauge in place. When a fitting is being screwed to the
gauge, hold a wrench on the socket flats instead of twisting
against the gauge socket screws which are intended to hold
the gauge mechanism in the case.
When gauges are mounted on the wall or panel, make sure
they are connected free from piping strains. Also see that the
mounting surface is flat, or insert washers under the flange of
the gauge case to obtain three-point suspension. Preferably,
the last length of piping leading up to the gauge should be flex-
ible tubing. This will ensure that the gauge is free from strain.
Install gauges where they will be free from the effects of
mechanical vibrations as this will wear out any gauge quickly.
Try to mount the gauge on a wall nearby and connect the
gauge to the machine which vibrates badly by means of
flexible line assembly.
Protect gauges from frequent pressure pulsations by using
liquid-filled or Duragauge Plus
®
with a throttle screw in the
socket of the gauge, needle valves, pulsation dampeners or
pressure snubbers.
When any gauge is used for steam pressures, a siphon filled
with water must be installed between the gauge and the line.
When the system is subject to occasional vacuum, provide a
leg of piping which cannot be emptied by the vacuum effect. A
drain cock or plug should be installed at the bottom of this leg
to enable occasional cleaning out of the sediment. The head
effect of this piping leg should be compensated for by resetting
the pointer of the gauge.
OPERATING CONDITIONS
The operating conditions to which a gauge will be subjected
must be considered. If the gauge will be subjected to severe
vibration or pressure pulsations, liquid filling the gauge may be
necessary to obtain normal product life.Other than discolora-
tion of the dial and hardening of the gasketing that will occur
as ambient temperatures exceed 150°F, metal case Dura-
gauges (that are not liquid filled) can withstand continuous
ambient temperatures as high as 250°F. Liquid filled gauges
can withstand 200°F but glycerin fill and acrylic window will tend
to yellow. Accuracy will be affected by approximately 1.5% per
100°F. Gauges with welded joints will withstand 750°F (450°F
with silver brazed joints) for short times without rupture,
although other parts of the gauge will be destroyed and cali-
bration will be lost. For temperature limits on other gauges see
the appropriate bulletin.
PROPER USE
Apply pressure slowly. do not open gauge cock or valve too
quickly – this imparts a severe strain on the Bourdon tube
which may rupture it, or result in shortened life. When the
service itself is subject to sudden pressure applications, use
a needle valve or the Ashcroft Gauge Saver.
Avoid overpressure. See that the apparatus is provided with a
relief valve and that the range of the gauge is higher than the
set pressure of the relief valve.
Sudden pressure release has the same detrimental effect and
should be compensated for in the same manner as for the
pressure applications mentioned above. On hydraulic presses,
Catalog Number 1056 or 1009DH Gauges with slotted link
should be specified. See Special Service Bulletin SG-1.
MAINTENANCE
Replace broken glasses and thus keep dirt out of the working
bearings and teeth of the movement mechanism.
Never oil gauge movements or linkages except with high grade
instrument oil. Regular oil attracts dirt and becomes gummy,
thus causing the gauge to act sluggish and inaccurate.
I
nstallation and Maintenance Instructions for
ASHCROFT
®
Pressure Gauges, Gauge Parts
and Ring Designs, Engineering Data
© Dresser, Inc., Dresser Instrument, 250 E. Main St., Stratford, CT 06614-5145, 203-378-8281, 203-385-0499 Fax, www.ashcroft.com
All sales subject to standard terms and conditions of sale. I&M008-10031-10/00 (250-1997B) GBE
+1
0
–1
–2
–3
–4
–5
–6
0
CORRECTION IN % 0F PRESSURE SCALE
02
0
4
06
08
0
1
0
0
120
140
160
180
200
220
240
260
280
300
320
340
360
380
400
TEMPERA
TURE IN °F
<– 75° ROOM TEMP. WHEN CALIBRATED
HEAT AFFECTS GAUGE ACCURACY
Approximate error or change in calibration of a Bourdon
tube type pressure gauge caused by changes in temperature.
Example: Gauge working at 500 psi pressure at 280°F. temperature
would have a –3% correction and would read 3% or 15 psi fast.
Page 190
Summary of Contents for BN 5-12 Series
Page 13: ...TAB 1 DEVICE DATA SHEETS ...
Page 18: ...TAB 2 APPROVED SUBMITTAL ...
Page 23: ...All data subject to change without notice 1 800 ASK 4WEG www weg net 14 ...
Page 26: ...Your advantages our pumps ...
Page 45: ...ADV 2 13E And what can we get flowing for you Your nearest contact Or visit www seepex com ...
Page 117: ...TAB 3 INSTALLATION OPERATIONS AND MAINTENANCE ...
Page 133: ...Page 37 ...
Page 233: ...www weg net Manual of Electric Motors 64 ENGLISH Figure 2 1 IEC motor nameplate Page 135 ...
Page 234: ...www weg net Manual of Electric Motors 65 ENGLISH Figure 2 2 NEMA motor nameplate Page 136 ...
Page 306: ...TAB 4 AS BUILTS AND SUPPLEMENTAL INFORMATION ...
Page 307: ...R Page 29 ...
Page 308: ...R Page 30 ...