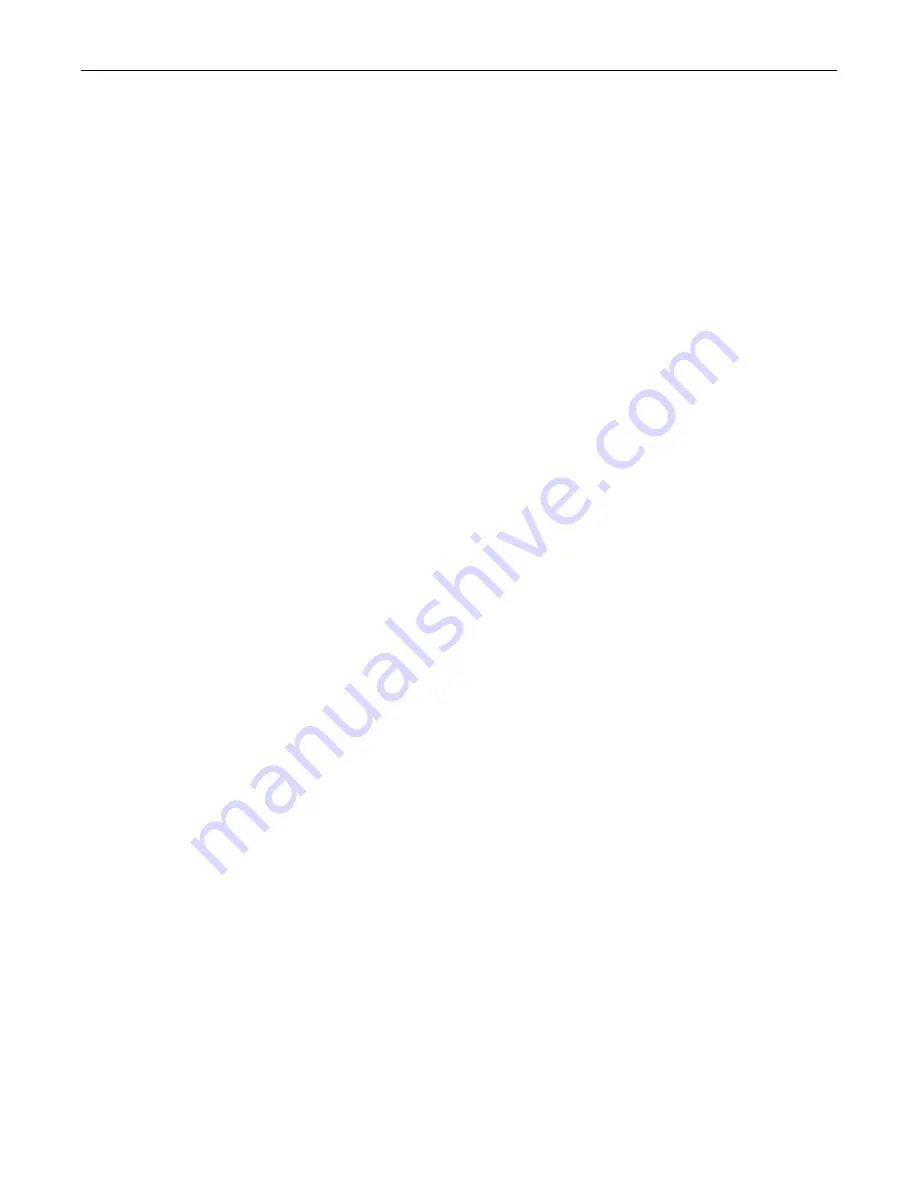
PantherPro/46 Image Recorder
TP8251
October 1995
PrePRESS SOLUTIONS CONFIDENTIAL
6-5
6-2.4 First Cylinder Lens
Material
• Lens cleaning tissue
• 99% minimum purity isopropyl alcohol or Optical Surface Cleaner
Procedure
NOTE: Maintain all Anti static Replacement/Removal Procedures for PC boards
while performing these procedures.
NOTE: Since 99% pure alcohol is to be used, be sure to work in a well ventilated
area.
Step 1.
Power down the system.
Step 2.
Remove the optics cover. Refer to Section 7, if necessary.
Step 3.
Using a flash light, check the first cylinder lens for dirt or imperfections.
Step 4.
While the first cylinder lens is in place, dampen the lens tissue with 99%
pure alcohol and carefully wipe the front and rear side of the lens.
Step 5.
The first cylinder cleaning is now complete.
Step 6.
Run copy quality test and inspect image for artifacts.
6-2.5 Beam Steering Mirror
Material
• Lens cleaning tissue
• 99% minimum purity isopropyl alcohol or Optical Surface Cleaner
Procedure
NOTE: Maintain all Anti static Replacement/Removal Procedures for PC boards
while performing these procedures.
NOTE: Pay attention to the location of any cables that are removed so that they
can be easily re-installed later.
NOTE: Since 99% pure alcohol is to be used, be sure to work in a well ventilated
area.
Step 1.
Power down the system.
Step 2.
Open the supply cassette cover and remove the supply cassette.