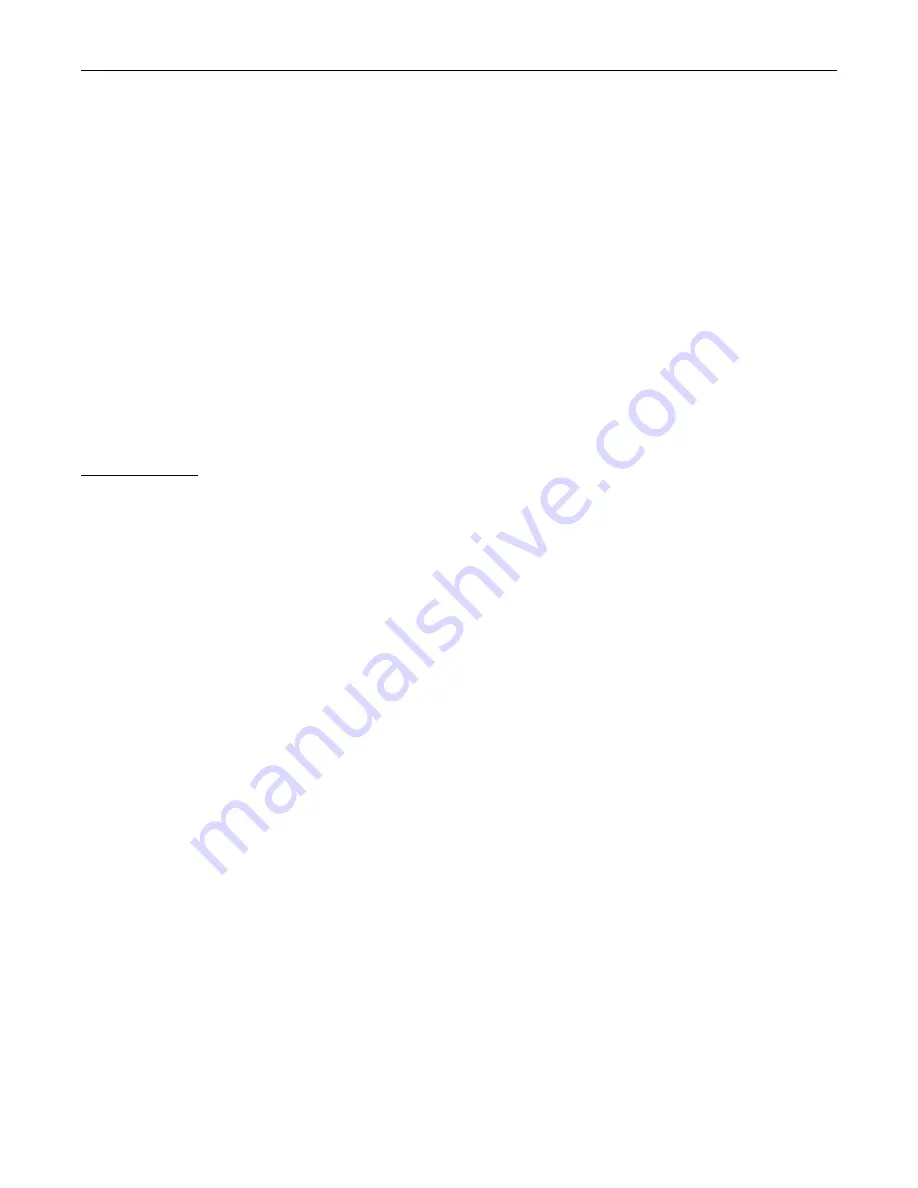
TP8251
PantherPro/46 Image Recorder
3-10
PrePRESS SOLUTIONS CONFIDENTIAL
October 1995
I. PCLK Synchronizer
A clock phase which best matches the START pulse selects each scan line and outputs a
new PCLK. This will minimize left edge jitter, keeping it to within a fraction of a pixel.
J. Intensity Control
A register which drives a D/A converter will set the laser intensity. This is the identical circuit
used on the RCB.
K. Facet Timer
A Facet Timer circuit times the scan line and issues various control signals whose timing is
related to the scan line. Examples of such signals are: Sample/Hold, Enhance, Inhibit Bias,
Speed Hi/Lo/Ok, End of Scan, etc. The decoding of these signals is fixed, and is oriented to a
specific expected polygon rotational rate. The polygon spins at 4444 rotations per minute
(RPM). One facet decoder GAL is used in BOB.
L. End of Scan interrupt
A maskable interrupt is generated once per scan during the inactive portion of a scan line.
Motor Control
M. Polygon Speed control
Polygon Speed Control consists of a 16 bit register and a 16 bit counter. On overflow, the
counter is loaded from the register, creating a programmable time base.
The output of this circuit is the square wave POLYCLK, which is fed to the polygon drive
circuitry and resides on the Polygon Driver PCB.
N. Leading Motor Control and Drive
The Leading Motor Control consists of a paper feed register, an adder/accumulator, and a
Galil GL1200 motor control IC. The adder/accumulator produces a series of pulses at a rate
set by the Paper Feed register. The GL1200 converts this into position information,
comparing with encoder inputs. Also, the GL1200 outputs velocity information. The position
and velocity information are summed with the accelerator information to form the input to the
motor drive. A nearly identical circuit is used on the RCB, HSCB, and WCB.
A leading encoder counter circuit makes a running count of encoder pulses available to
software to provide leading position feedback, which may be used to facilitate punch
positioning. This register can also be enabled to interrupt after the occurrence of a specified
number of encoder pulses.
The analog circuitry which drives the leading motor is virtually identical to the circuit used on
the RCB, HSCB, and WCB.
O. Cutter Motor Control and Drive
The cutter motor is implemented by 5 bits of the Motor Control Register. Cutter power is
programmable in 10% steps from 70% to 100%. The cutter motor is driven as on the RCB.
The cutter motor is removed from the circuit on power down by a relay. This prevents the
cutter motor from acting as a generator when manually operated after powered down. This is
transparent to software.