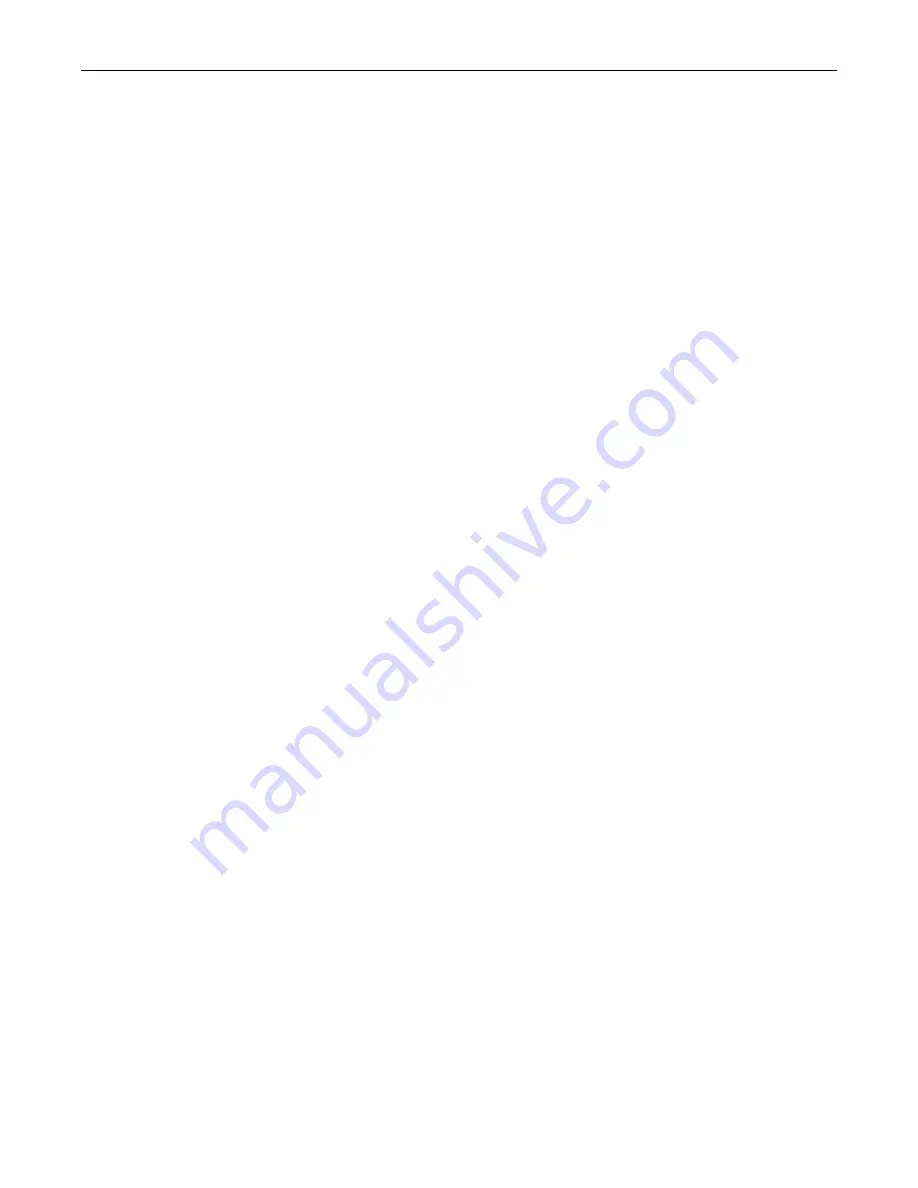
TP8251
PantherPro/46 Image Recorder
3-16
PrePRESS SOLUTIONS CONFIDENTIAL
October 1995
As the gate is closed, both pinch rollers shall contact the drive roller 0.125" before the gate
frame rests against the gate frame stop pins.
3-6.2.7 Pin Registration Punch System
The punch system is capable of punching two to four holes in a single line across the width of
the media. Either head or tail punching is supported (but not on the same page). Punching
takes place after the image is recorded. To achieve a head punch, the image must be rotated
180
°
.
The punch system main components include a front and rear casting, cam bar, stripper plate,
round and/or oval punch pins, a punch motor, roller crank, punch home switch, and yoke.
During a punch cycle, holes are punched after imaging takes place. The punch hole location
is determined by software. Media positioning speed varies with resolution and distance from
image to punch holes. When +12 volts DC is applied to the punch motor, the roller crank,
which is secured to the motor shaft flat with a set screw, will rotate and lift the yoke. The yoke,
which is secured to the cam bar shaft flat, with a set screw, acts like a lever and pivots the
cam bar to extend its mounted punch pins through the media. The punch stripper plate will
apply pressure to the media as the punch motor rotates and pivots the cam bar and punch
pins. When the punch pins are near full extension the media will be punched. The film chaff
will pass through the rear casting and fall into the chaff tray which is attached to the rear
casting with two thumbscrews. As the motor completes one revolution, the switch plate
(attached to the cam bar) will return to its original position and defeat the home switch.
Software recognizes when the punch home switch is closed, and stops the motor.
3-6.2.8 Worm Gear Box Assembly and Spur Gear
The worm gear box assembly contains a servo leading motor/encoder, gear box, and
hardened worm gear.
The "Leading Motor Control" provides closed loop position and velocity control of the servo.
Control signals are amplified to form the input to the leading motor analog drive circuitry.
Leading motor encoder pulses (ENCDRA and ENCDRB) are monitored by the GL1200 IC to
form position information necessary for accurate registration. The media may be moved at
different speeds to accommodate different resolution of the images being output as well as
the high speed preset or manual advance function.
Attached to the leading motor shaft is a worm that meshed with a spur gear attached
(clamped) to the drive roller, which creates a 144 to 1 reduction ratio.
3-6.2.9 Power Knife
The power knife is a spring loaded, rotary knife assembled in a carriage which transverses
across a stationary knife, located behind the media path. A Teflon™ coated worm gear,
secured to the 'flat' of the knife motor shaft, is the mechanism that provides bi-directional
movement for the knife carriage assembly.
Rotation of the knife is provided by an O ring which is mounted axially on the same shaft. The
O ring is rotated due to frictional contact with the spring loaded pressure plate. The bar is
spring-loaded outwards to permit passage of the media. It is compressed downwards by the
O ring holding the paper stationary during the cutting stroke.