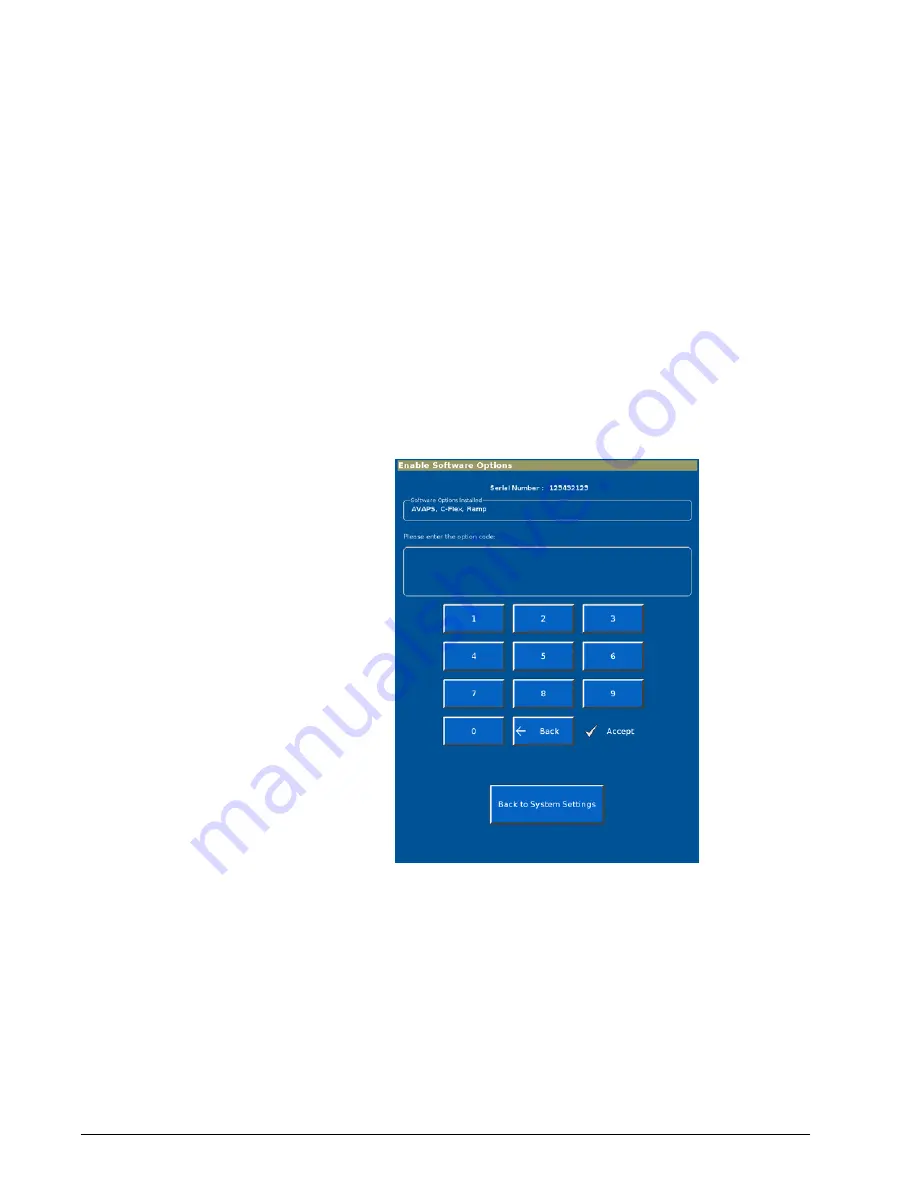
Chapter 5
5-8
V60 Ventilator Service Manual
1049766 Rev A
Diagnostic Mode and Troubleshooting
5.1.5
Enabling Software Options
Every software option has a unique enable code for each ventilator. A unique
option code is required for each software option before it can be enabled.
NOTE:
Do not
install an option until you have verified that the ventilator serial
number on the enclosure matches the serial number shown on the
Ventilator Information screen (section 5.2.1). If a serial number must be
reprogrammed, do so
before
enabling an option.
1. From the System Settings screen, touch
Software Options
.
2. Use the onscreen keypad on the Enable Software Options screen
(Figure 5-8) to enter the option code, then touch
Accept
.
Figure 5-8: Enable Software Options Screen
3. If the option code is invalid, the screen prompts you to reenter.
4. When the software option has been successfully enabled, the screen
displays
Enabled:
followed by the option name.
5. Repeat as needed to enable additional options.
6. To exit the Enable Software Options screen at any time, touch
Back to
System Settings
.