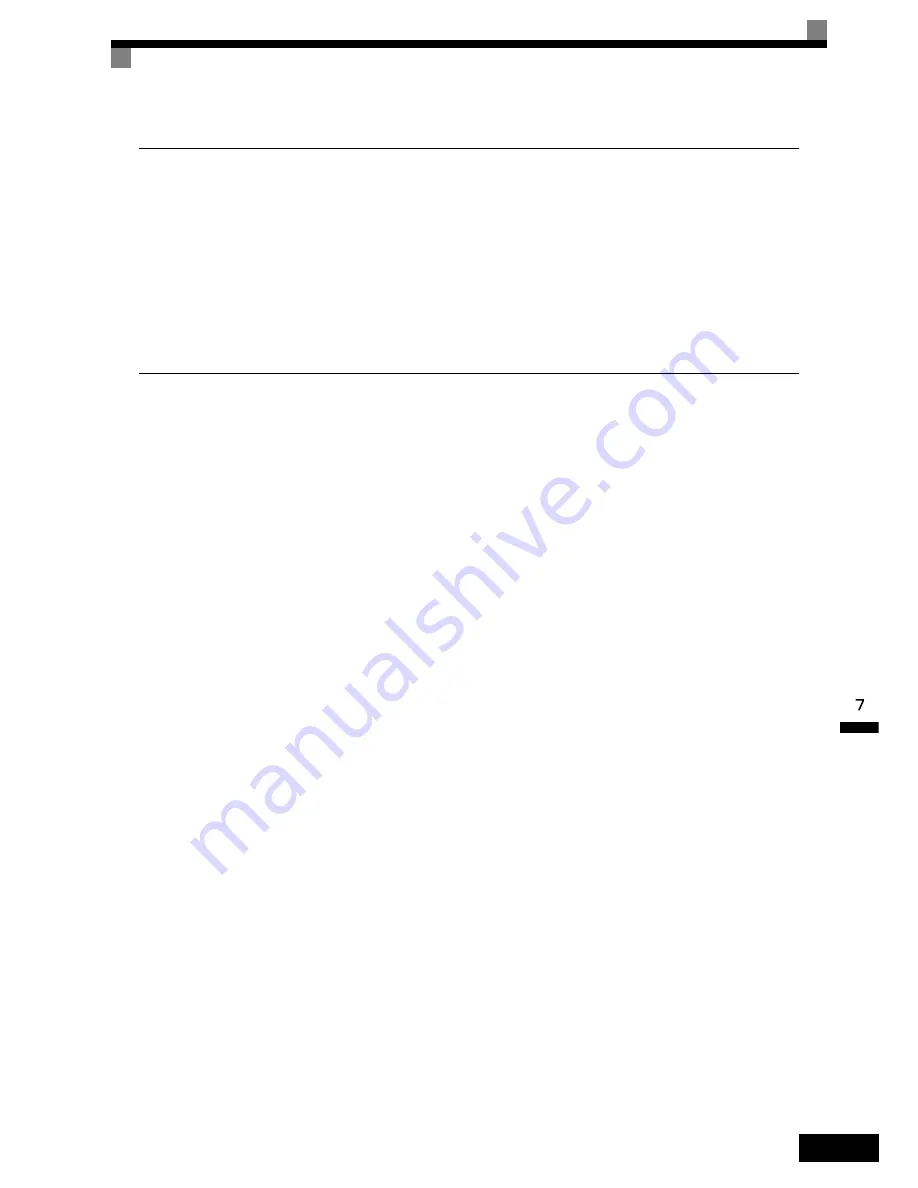
Troubleshooting
7-
21
If There is Low Speed Control Accuracy at High-speed Rotation in Open-
loop Vector Control Mode
The motor's rated voltage is high.
The Inverter's maximum output voltage is determined by its input voltage. (For example, if 200 VAC is input,
then the maximum output voltage will be 200 VAC.) If, as a result of vector control, the output voltage refer-
ence value exceeds the Inverter output voltage maximum value, the speed control accuracy will decrease. Use
a motor with a low rated voltage (i.e., a special motor for use with vector control), or change to flux vector
control.
If Motor Deceleration is Slow
Use the following information when the motor deceleration is slow.
The deceleration time is long even when braking resistor is connected.
The following causes are possible.
“Stall prevention during deceleration enabled” is set.
When braking resistor is connected, set constant L3-04 (Stall Prevention Selection during Deceleration) to 0
(disabled) or 3 (with braking resistor). When this constant is set to 1 (enabled, the factory setting), braking
resistor does not fully function.
The deceleration time setting is too long.
Check the deceleration time setting (constants C1-02, C1-04, C1-06, and C1-08).
Motor torque is insufficient.
If the constants are correct and there is no overvoltage fault, then the motor's power is limited. Consider
increasing the motor capacity.
The torque limit has been reached.
When a torque limit has been set in constants L7-01 to L7-04, no torque will be output beyond that limit. This
can cause the deceleration time to be too long. Check to be sure that the value set for the torque limit is suit-
able.
If torque limits have been set for the multi-function analog input terminal A2 Function H3-09 (set value: 10 to
12 or 15), check to be sure that the analog input value is suitable.
If the Vertical-axis Load Drops When Brake is Applied
The sequence is incorrect. The Inverter goes into DC injection braking status for 0.5 seconds after deceleration
is completed. (This is the factory-set default.)
To ensure that the brake holds, set frequency detection 2 (H2-01 = 5) for the multi-function contact output ter-
minals (M1 and Mw) so that the contacts will turn OFF when the output frequency is greater than L4-01 (3.0
to 5.0 Hz). (The contacts will turn ON below L4-01.)
There is hysteresis in frequency detection 2 (i.e., a frequency detection width, L4-02 = 2.0 Hz). Change the
setting to approximately 0.5 Hz if there are drops during stop. Do not use the multi-function contact output run
signal (H2-01 = 0) for the brake ON/OFF signal.
Summary of Contents for VARISPEED G7 -
Page 3: ......
Page 11: ...viii...
Page 33: ...1 16...
Page 105: ...4 20...
Page 349: ...6 154...
Page 375: ...7 26...
Page 413: ...10 24...
Page 417: ......