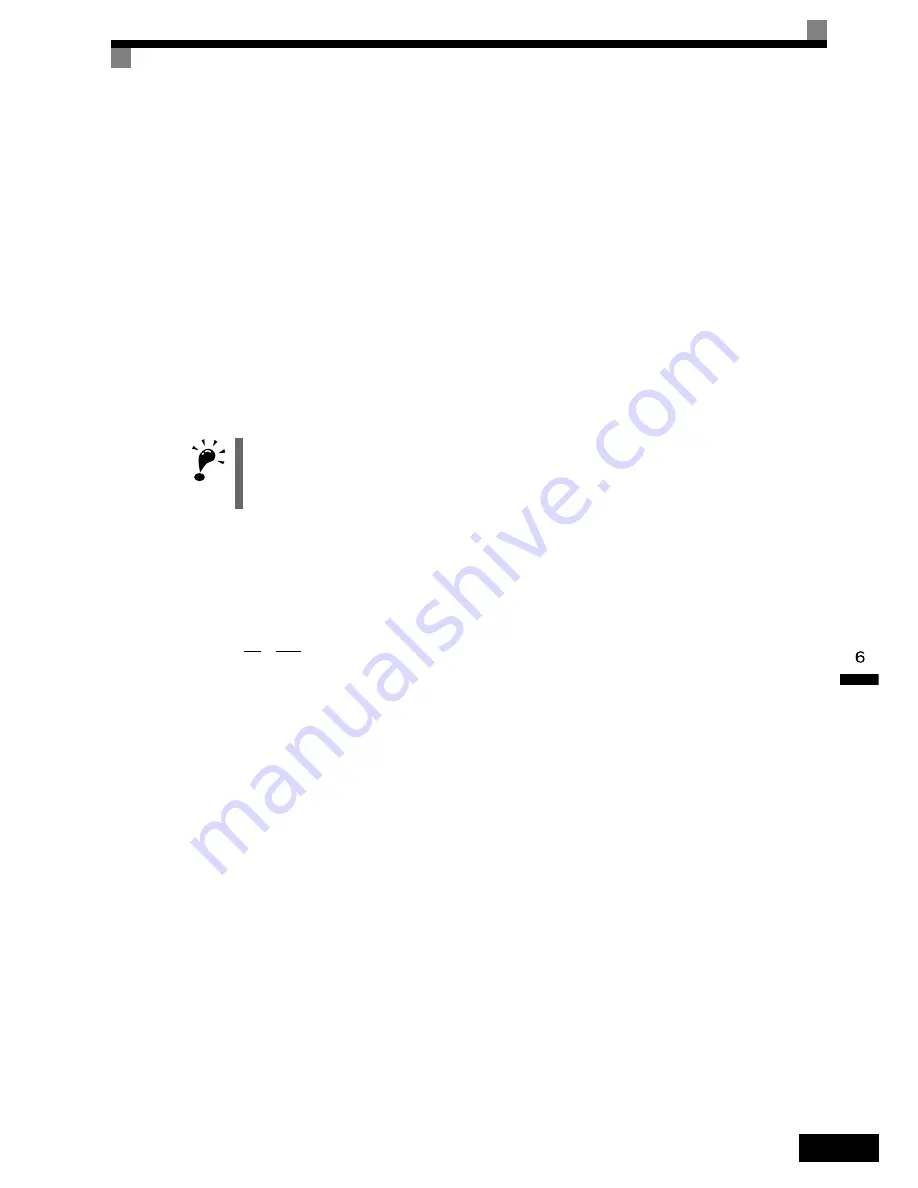
Options
6-
145
Setting Number of Gear Teeth Between PG and Motor
Set the number of PG gear teeth in F1-12 and F1-13. If there are gears between the motor and PG, you can
operate the motor by setting the number of gear teeth.
When the number of gear teeth has been set, the number of motor rotations within the Inverter is calculated
using the following formula.
No. of motor rotations (min
−
1
.) = No. of input pulses from PC
×
60 / F1-01
×
F1-13 (No. of gear teeth on load
side) / F1-12 (No. of gear teeth on motor side)
Matching Motor Speed During Acceleration and Deceleration to Frequency Reference
You can select whether to enable or disable integral operation during acceleration and deceleration when using
flux vector control.
To match the motor speed as closely as possible to the frequency reference even during acceleration and decel-
eration, set F1-07 to 1.
Setting PG Pulse Monitor Output Dividing Ratio
This function is enabled only when using PG speed control card PG-B2. Set the dividing ratio for the PG pulse
monitor output. The set value is expressed as n for the higher place digit, and m for the lower place 2 digits.
The dividing ratio is calculated as follows:
The dividing ratio can be set within the following range: 1/32
≤
F1-06
≤
1. For example, if the dividing ratio is
1/2 (set value 2), half of the number of pulses from the PG are monitor outputs.
Detecting PG Open Circuit
Select the stopping method when PG cable disconnected is detected and the PG open circuit (PGO) detection
time.
When the Inverter is operating with the frequency reference set to 1% minimum (except when operating on
direct current), if the speed feedback from PG is greater than the time setting in F1-14, PGO is detected.
Detecting Motor Overspeed
An error is detected when the number of motor rotations exceeds the regulated limit. An overspeed (OS) is
detected when a frequency that exceeds the set value in F1-08 continues for longer than the time set in F1-09.
After detecting an overspeed (OS), the Inverter stops according to the setting in F1-03.
Detecting Speed Difference between the Motor and Speed Reference
An error is detected when the speed deviation (i.e., the difference between the designated speed and the actual
motor speed) is too great. Speed deviation (DEV) is detected after a speed agreement is detected and when the
speed reference and actual workpiece speed are within the setting of L4-02, if a speed deviation great than the
set value in F1-10 continues for longer than the time set in F1-11. After a speed deviation is detected, the
Inverter stops according to the setting in F1-04.
IMPORTANT
If F1-01 is set to 1, overshoot or undershoot may occur easily immediately after acceleration and decelera-
tion. To minimize the possibility of overshoot or undershoot occurring, set F1-01 to 0.
Dividing ratio = (1 + n)/m (Setting range) n: 0 or 1, m: 1 to 32
F1-06 =
n
m
Summary of Contents for VARISPEED G7 -
Page 3: ......
Page 11: ...viii...
Page 33: ...1 16...
Page 105: ...4 20...
Page 349: ...6 154...
Page 375: ...7 26...
Page 413: ...10 24...
Page 417: ......