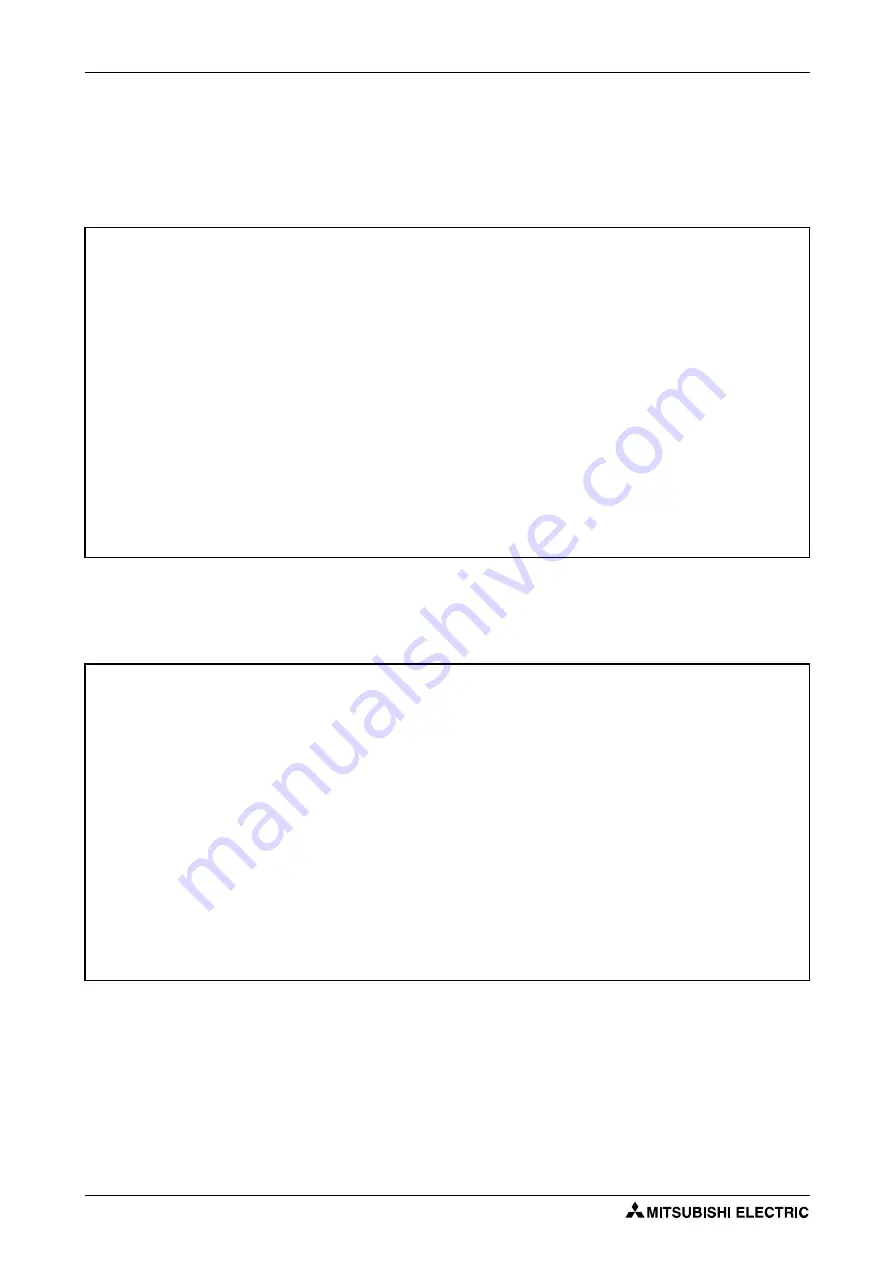
IV
General hazard instructions and safety measures
The following hazard instructions should be understood as general regulations for handling the robot
system. These instructions must always be observed in the planning, installation and operation of the
robot system.
General safety instructions during handling
Detailed information on safety and protection is contained in the safety manual.
P
DANGER:
●
The safety and accident-prevention regulations that apply to the specific use must be ob-
served. Installation, wiring and opening of assemblies, components and devices/units must
be carried out when the system is disconnected (dead).
●
Regularly check the live cable and lines to which the devices/units are connected for insula-
tion faults or breaks. If you detect a fault in the wiring/cable then you must immediately
switch off the devices and disconnect power from the cable and then replace the defective
cable.
●
Before startup, check whether the permissible mains voltage range accords to the local
mains voltage rating.
●
Take appropriate measures to restart any interrupted program after voltage failures and
malfunctions. No hazardous/dangerous operating conditions must arise when doing this,
even temporarily. If necessary, force an "EMERGENCY-STOP".
●
EMERGENCY-STOP equipment compliant to EN 60204/IEC 204 VDE 0113 must remain effec-
tive during all applications. Unlocking the EMERGENCY-STOP equipment must never result
in uncontrolled movements of the robot arm.
P
DANGER:
●
Some of the robot arms are made of plastic. The robot arm does not take attachments of
components or gross force effects in these parts. The covers are oil-resistant.
●
The robot axis are fitted with brakes. You should not apply any manual pressure to the robot
joints to avoid damage to the gear reduction.
●
Even when the robot arm is within its normal working area, the wrist (articulated arm robot)
or spindle (SCARA robot) may nevertheless collide. Pay special attention to this situation in
jog mode.
●
The robot arm is comprised of precision parts that require suitable lubrication. During a cold
start at low temperatures, a servo alarm may be triggered or positional accuracy may be
lost. In such a situation, you should first operate the robot arm in standby.
●
The robot arm and the controller require a class 3 grounding to permanently prevent risk of
electrical shock and disturbances.
●
All details and specifications in the manuals are only valid if you carry out the maintenance
work stipulated in the technical manual.
Summary of Contents for MELFA RH-FRH-D
Page 2: ......
Page 4: ......
Page 6: ......
Page 16: ...Contents X ...
Page 22: ...Environmental conditions for operation Introduction 1 6 ...
Page 70: ...Grounding the robot system Installation 3 32 ...
Page 90: ...Teaching Box connection Connection 4 20 ...
Page 96: ...Switch on the robot system Startup 5 6 ...
Page 128: ...Dimensions Appendix A 18 ...
Page 130: ...A 20 Index Appendix ...
Page 131: ......
Page 132: ......
Page 133: ......
Page 134: ......
Page 135: ......
Page 136: ......
Page 137: ......
Page 138: ......
Page 139: ......
Page 140: ......
Page 141: ......
Page 142: ......
Page 143: ......
Page 144: ......
Page 145: ......
Page 146: ......
Page 147: ......
Page 148: ......
Page 149: ......
Page 150: ......
Page 151: ......
Page 152: ......
Page 153: ......
Page 154: ......
Page 155: ......
Page 156: ......
Page 157: ......
Page 158: ......
Page 159: ......
Page 160: ......
Page 161: ......
Page 162: ......
Page 163: ......
Page 164: ......
Page 165: ......