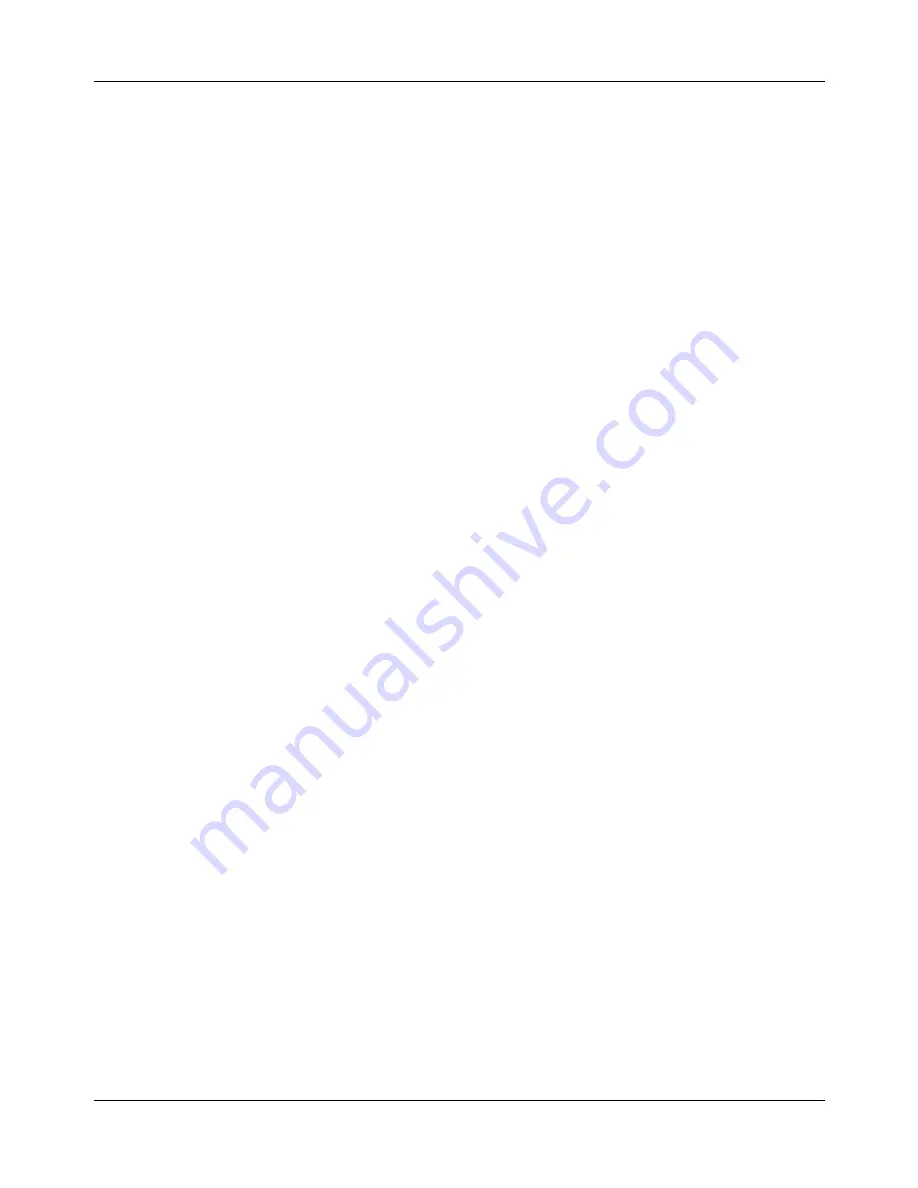
Design Guidelines
Transport System Design
12
MagneMotion
Rockwell Automation Publication MMI-UM002E-EN-P - March 2016
only has half coverage, the effective PID values and peak thrust are halved, and the
system will not perform as well as it does with full coverage.
It is important to note that the Downstream Gap measurement is added to the last motor block
of all MagneMover LITE motors in the transport system. This is important when considering
the motor blocks that a vehicle (puck) owns (refer to
) and also
for determining when vehicles are considered to be at the end of a Path or cleared of a Node
boundary (such as a Terminus Node).
Motor Cogging
Due to the use of epoxy cores in the motor windings, there is no cogging between the Magne-
Mover LITE motor and the magnet array (refer to
Motor Controllers
The motor controller for each MagneMover LITE motor is located inside the MM LITE
motor. Each MM LITE motor has one motor controller, also referred to as the master.
The motor controller is responsible for controlling the thrust applied to each vehicle (puck) by
the motor and reading sensors in the motor to determine vehicle position. The motor control-
lers communicate with each other and a Node Controller via RS-422 serial communication.
Electrical Wiring
The MagneMover LITE motors are designed to operate at a n36 VDC. A block dia-
gram of a MM LITE transport system schematic is provided in
. Note that any part
numbers shown are for reference only and are subject to change.
Power Wiring
All power wiring must be constructed so there is minimal loss between the power supplies and
the motors. Additionally, the power wiring must be able to support power regeneration due to
the active braking or deceleration of vehicles. The preferred architecture for the power bus in
a MagneMover LITE transport system is a number of T-splitters or junction boxes (shown in
) connected in series to form a single, low resistance, power bus with a tap to each
motor.
Vehicle motion will consume power when the vehicle accelerates and regenerate power when
it decelerates. While the vehicle is accelerating, the motor is drawing power from the motor
power supply system, including any excess power being generated from regeneration in other
parts of the transport system connected to the same power supply system. In the worst case, a
single motor can draw up to the value for peak power per vehicle while the vehicle is finishing
its acceleration. In addition to providing the power used to accelerate a vehicle, the wiring
must also be designed to manage power regenerated by a vehicle as it stops. In general, if a
system is designed to support supplying power during acceleration, it will also support excess
power created by regeneration during deceleration.