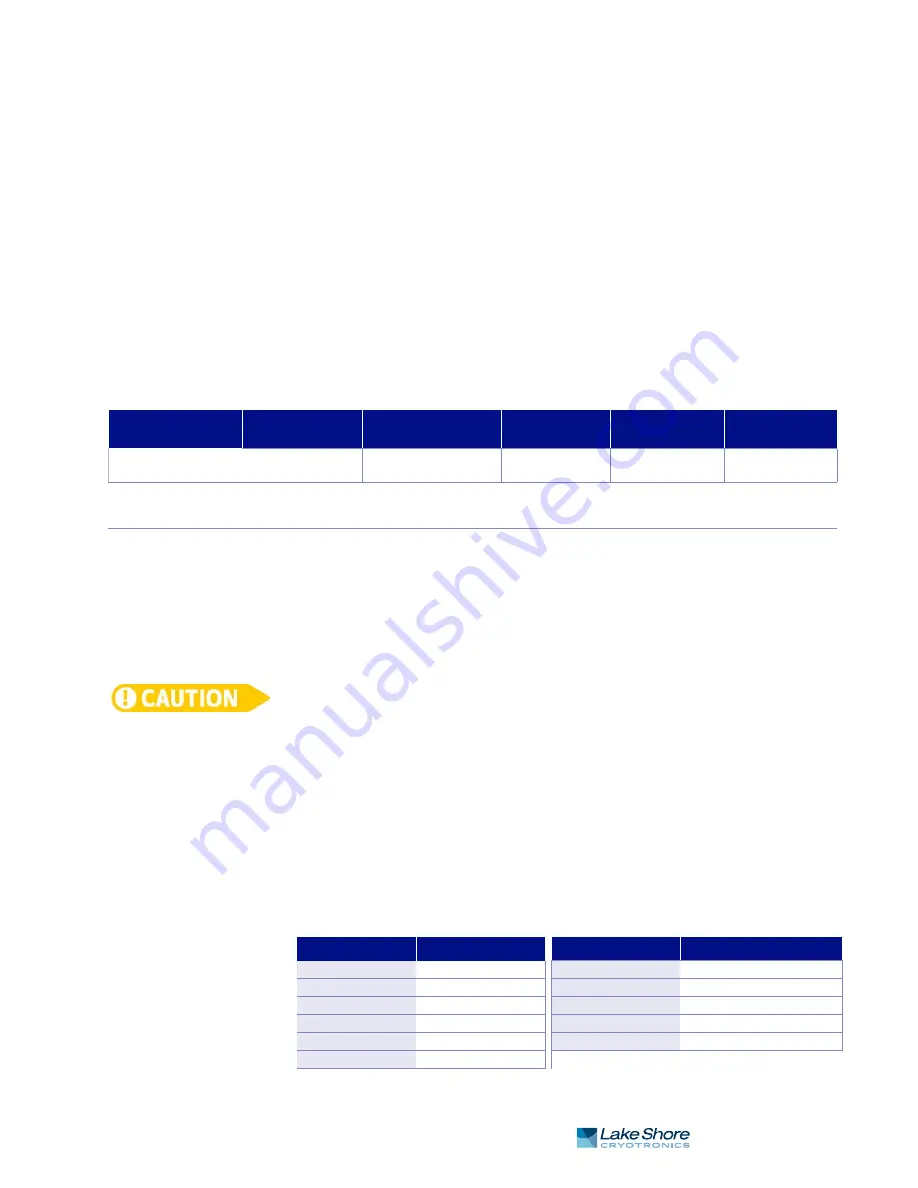
47
|
www.lakeshore.com
3.2.4 Water
Requirements
The CCR compressor needs cooling water even for short periods of operation. Cooling
water is typically available in several ways: from the municipal (tap) water system,
from a large recirculating cooling system sized for the building or lab, or from a small,
dedicated, recirculating chiller sized for the power dissipation of the CCR compressor.
When cooling with tap water, use an accessible shut-off valve. The shut-off valve
helps conserve water by shutting it off when its not in use. Water pressure may be
difficult to control if the probe station uses a shared building water line. Large
seasonal variation in temperature can also cause problems. High water temperatures
in the summer months may exceed the specified temperature requirement. If large
variations in the temperature or pressure of tap water are expected, you should
consider using a dedicated chiller.
3.2.4.1 Water Flow and Temperature
No matter what cooling water source is chosen, the water flow rate and temperature
listed in TABLE 3-3 must be maintained for continuous operation of the CCR. Water
flow must be maintained with the pressure drop listed in the table. Poor or
inconsistent water flow will cause shut down of the CCR compressor.
3.2.4.2 Water Quality
Water quality is important to the long term reliability of the CCR compressor. Poor
water quality may cause clogging of the internal cooling lines or even premature
failure of the cooling lines themselves. Cooling water chemistry must be compatible
with the CCR compressor cooling components; refer to TABLE 3-4 for specific
parameters for the CCR compressor
Do not use demineralized water because it may cause a leakage or malfunction.
When cooling with tap water, chemistry is less of an issue because fresh water is
constantly running through the system diluting any contamination. Use a well
maintained water filter to remove any sediment that could cause a clog.
Recirculating water systems have many advantages in water conservation and
regulation of temperature and pressure, but it is very important to address water
quality issues early in the installation process. Closed loop systems need to be
maintained so that the pH level, amount of dissolved minerals, and biological growth
are kept within acceptable limits for all of the cooling system components. When
setting up a new recirculating water system, begin by reading and understanding the
chiller manufacturer’s recommendations. They typically provide good instructions in
addition to water test and treatment kits.
Inlet temperature
Outlet temperature
Pressure
Flow
Pressure drop at
minimum flow
Cooling capacity
4 °C to 27 °C
(40 °F to 80 °F)
40 °C max
(104 °F max)
210 kPa (30 psig) min
690 kPa (100 psig) max
2.7 L/min
(0.7 gmp) min
100 kPa
(15 psid)
3.2 kW
(11,000 BTU/h)
Alternate Coolant:
Composition: 50% pure ethylene 50% water
Alternate coolant flow rate: 3.5 L/min (0.9 gpm) minimum
TABLE 3-3
Cooling water requirements for CCR compressor
Water component
Specification
Water component
Specification
pH value (25 °C, 77 °F)
6.5 to 8.0
Iron (ppm)
1.0 max
Chloride (ppm)
200 max
Sulfur ion (ppm)
None detectable
Sulfate (ppm)
200 max
Ammonium ion (ppm)
1.0 max
M-alkalinity (ppm)
100 max
Suspended solids (μg/L)
<250
Total hardness (ppm)
200 max
Particle size (μm)
<300
Silica (ppm)
50 max
TABLE 3-4
Water quality specifications for the CCR compressor