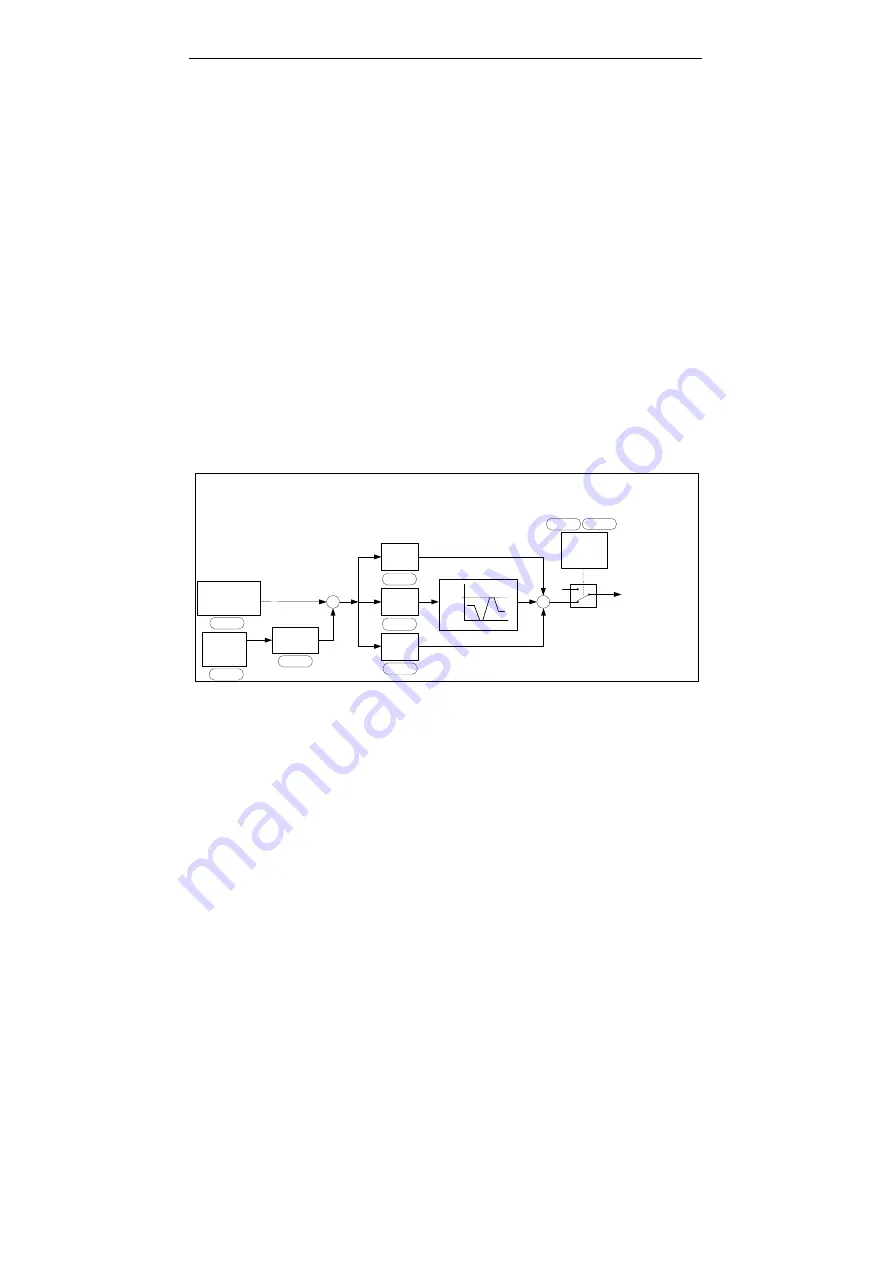
Parameters
Operating manual INVEOR
41
PID process control:
The reference for the PID process control is read in percentage steps as in
the “frequency setting mode”. 100% corresponds to the working range of the
connected sensor, which is read in from the active channel (selected by the
“PID feedback”).
Depending on the control difference, a rotation speed value is output to the
control output with the help of the amplification factors for the propotional
gain (3,050), integral gain (3,051) and derivative gain (3,052). In order to
prevent the integral share from increasing limitlessly in case of uncontrollable
control differences, this value is limited to a specific set value (corresponding
to the “maximum frequency” (1,021)).
PID inverse:
The PID feedback can be inverted using the 3.061 parameter. The feedback is
imported inversely, i.e. 0 V…10 V correspond internally to 100%…0%.
Please note that the reference must also be defined inversely.
An example:
A sensor with an analogue output signal of (0 V…10 V) is to operate as the
source of the feedback channel (at AIx). At an output variable of 7 V (70%),
this is to be regulated inversely. The internal feedback then corresponds to
100% – 70% = 30%. Accordingly, the specified reference is 30%.
Reference
channel
PID
feedback
Inverted
-
KP
KI
KD
Limitation I
part
t
yi
yimax
+
0
PID
stand-by
function
Frequency
reference mode
PID process controller operating mode
3.061
3.060
1.130
3.050
3.051
3.052
3.070
3.071
Fig. 18: PID process control
Summary of Contents for INVEOR MA
Page 1: ...Operating manual INVEOR Betriebsanleitung_INVEOR_A5 indd 1 28 02 11 10 33...
Page 91: ...Guidelines Norms and Standards Operating manual INVEOR 91...
Page 92: ...Guidelines Norms and Standards 92 Operating manual INVEOR...
Page 93: ...Guidelines Norms and Standards Operating manual INVEOR 93...